-
What happened?
A work crew was rigging up slickline equipment within a coiled tubing lift frame (CTLF).
When lowering the main winch wire, they heard a noise from the top of the frame.
A 27kg (60lbs) brake housing unit, a 17kg (37lbs) brake piston and two 4kg (9lbs) bevelled washers dropped 24m (80ft) to the rig floor.
Two of the objects dropped in the red zone, while the other two hit the yellow zone.
No one was injured.
-
Why did it happen?
Main winch brake housing failed due to hydraulic overpressure.
- A secondary brake was installed in the past as an additional measure of overprotection.
- Each brake had its own pressure reducing valve, but there was no secondary overpressure protection on the secondary brake in case the drain hose was blocked or disconnected. This allowed pressure to build up in the reducing valve and brake housing.
No method to alert crew of main winch brake overpressure.
Design was signed off by third party based on drawings only, without a physical check. Quick connect coupling were nor clearly represented in the drawing.
No verification that the system had been installed correctly, apart the function test, which did not last enough for pressure build up.
-
What did they learn?
Undertake full overview and design review of hydraulic system before starting work, including physical verification of the system. Ensure that system design drawings are clear and cover all the equipment.
Implement upgraded design - complete with over pressure protection to all parts of the system.
Update maintenance checklists and associated paperwork.
Implement verifications procedures to ensure the equipment has been installed correctly. Create and
roll out documented verification process for checking system hook up offshore.
Third party companies should undertake physical verification of new systems.
Review exclusion zone procedures.
-
Ask yourself or your crew
How could this happen here? What processes do we have in place to prevent it?
How can you check that the hydraulic braking equipment is properly installed and maintained? What tests do we need to undertake?
How do you know where are the exclusion zones and where is safe to stand during today’s lifting operation?
If something goes wrong, what is the emergency procedure?
Add to homescreen
Content name
Select existing category:
Content name
New collection
Edit collection
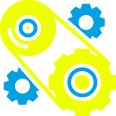
What happened?
A work crew was rigging up slickline equipment within a coiled tubing lift frame (CTLF).
When lowering the main winch wire, they heard a noise from the top of the frame.
A 27kg (60lbs) brake housing unit, a 17kg (37lbs) brake piston and two 4kg (9lbs) bevelled washers dropped 24m (80ft) to the rig floor.
Two of the objects dropped in the red zone, while the other two hit the yellow zone.
No one was injured.
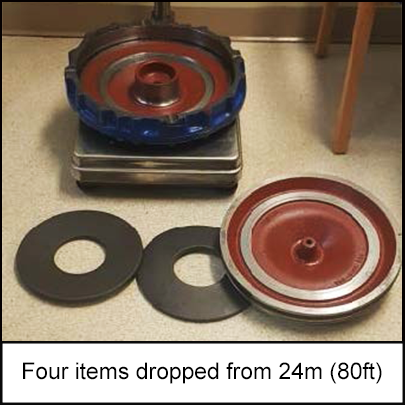
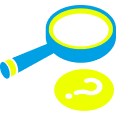
Why did it happen?
Main winch brake housing failed due to hydraulic overpressure.
- A secondary brake was installed in the past as an additional measure of overprotection.
- Each brake had its own pressure reducing valve, but there was no secondary overpressure protection on the secondary brake in case the drain hose was blocked or disconnected. This allowed pressure to build up in the reducing valve and brake housing.
No method to alert crew of main winch brake overpressure.
Design was signed off by third party based on drawings only, without a physical check. Quick connect coupling were nor clearly represented in the drawing.
No verification that the system had been installed correctly, apart the function test, which did not last enough for pressure build up.
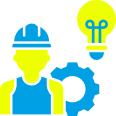
What did they learn?
Undertake full overview and design review of hydraulic system before starting work, including physical verification of the system. Ensure that system design drawings are clear and cover all the equipment.
Implement upgraded design - complete with over pressure protection to all parts of the system.
Update maintenance checklists and associated paperwork.
Implement verifications procedures to ensure the equipment has been installed correctly. Create and
roll out documented verification process for checking system hook up offshore.
Third party companies should undertake physical verification of new systems.
Review exclusion zone procedures.
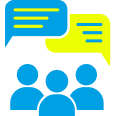
Ask yourself or your crew
How could this happen here? What processes do we have in place to prevent it?
How can you check that the hydraulic braking equipment is properly installed and maintained? What tests do we need to undertake?
How do you know where are the exclusion zones and where is safe to stand during today’s lifting operation?
If something goes wrong, what is the emergency procedure?
A work crew was rigging up slickline equipment within an oiled tubing lift frame (CTLF). Four items dropped 24m (80ft) from the top of the frame to the rig floor. No one was injured.