-
What happened?
An able seaman (AB) and an inexperienced cadet were closing ventilation flaps.
Each worker closed a vent, winding the handles anti-clockwise.
The cadet felt no more counterweight on his crank handle and communicated his vent was closed.
The AB asked the cadet to check by continuing to turn the handle.
As the cadet carried on turning counter-clockwise, it started raising the vent flap.
The cadet felt weight in the handle and accidently let go.
The handle rotated clockwise, and the crank handle detached, flying through the air, hitting the AB on his right shin.
The AB received cuts to the skin and fractured their leg.
He was evacuated by helicopter for treatment ashore.
-
Why did it happen?
Inadequate maintenance of wires, sheaves, winches locks and handles:
- Emergency release lever was in the wrong position.
- Crank handle securing mechanism was poor.
- Safety locks were stuck open due to a corroded sheave trapping the lock wires.
- Design flaw – two lock wires were passing through the sheave with limited space, causing them to get stuck.
- Shallow indentation and wingnut screw used to secure the handle were not properly secured (see image).
No written risk assessment for the operation. The risk was not fully assessed and was considered tolerable.
Vent house door was padlocked following a port call – there was no visual way to check that the flaps were closing.
The cadet did not trust his initial judgment and followed the instruction to keep turning.
- He was not aware of the proper position of the emergency release and was confused by the AB’s instructions.
-
What did they learn?
Ensure all workers are trained in this operation and are fully aware of the risks and mitigating measures.
Develop a risk assessment for this task. Specify minimum personnel required to do the job safely.
Ensure appropriate maintenance and repair of the wires, sheaves, winches locks and handles.
Ensure all instructions are clear and correct.
-
Ask yourself or your crew
What should the cadet have done when the instructions went against his judgement?
How could the corroded sheave and design flaw have been identified and fixed?
Do you do a risk assessment before all your tasks?
- If not, what are the exceptions and why?
What checks do you perform before you start work?
Add to homescreen
Content name
Select existing category:
Content name
New collection
Edit collection
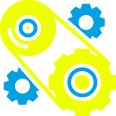
What happened?
An able seaman (AB) and an inexperienced cadet were closing ventilation flaps.
Each worker closed a vent, winding the handles anti-clockwise.
The cadet felt no more counterweight on his crank handle and communicated his vent was closed.
The AB asked the cadet to check by continuing to turn the handle.
As the cadet carried on turning counter-clockwise, it started raising the vent flap.
The cadet felt weight in the handle and accidently let go.
The handle rotated clockwise, and the crank handle detached, flying through the air, hitting the AB on his right shin.
The AB received cuts to the skin and fractured their leg.
He was evacuated by helicopter for treatment ashore.
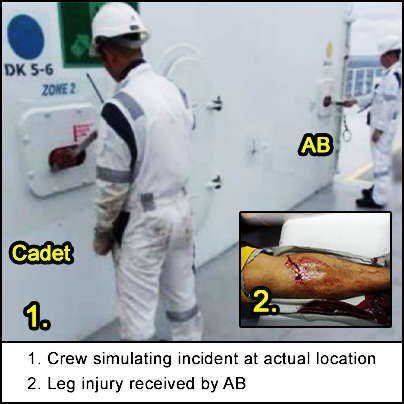
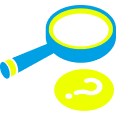
Why did it happen?
Inadequate maintenance of wires, sheaves, winches locks and handles:
- Emergency release lever was in the wrong position.
- Crank handle securing mechanism was poor.
- Safety locks were stuck open due to a corroded sheave trapping the lock wires.
- Design flaw – two lock wires were passing through the sheave with limited space, causing them to get stuck.
- Shallow indentation and wingnut screw used to secure the handle were not properly secured (see image).
No written risk assessment for the operation. The risk was not fully assessed and was considered tolerable.
Vent house door was padlocked following a port call – there was no visual way to check that the flaps were closing.
The cadet did not trust his initial judgment and followed the instruction to keep turning.
- He was not aware of the proper position of the emergency release and was confused by the AB’s instructions.
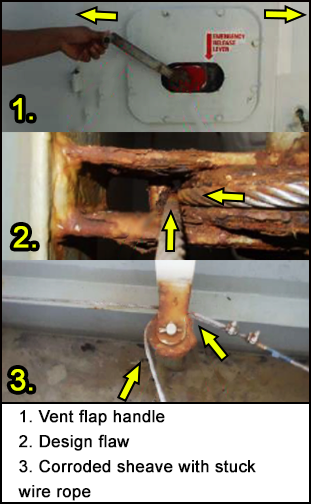
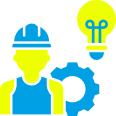
What did they learn?
Ensure all workers are trained in this operation and are fully aware of the risks and mitigating measures.
Develop a risk assessment for this task. Specify minimum personnel required to do the job safely.
Ensure appropriate maintenance and repair of the wires, sheaves, winches locks and handles.
Ensure all instructions are clear and correct.
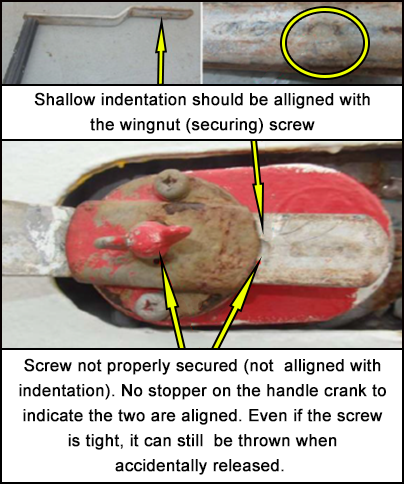
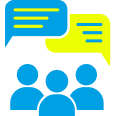
Ask yourself or your crew
What should the cadet have done when the instructions went against his judgement?
How could the corroded sheave and design flaw have been identified and fixed?
Do you do a risk assessment before all your tasks?
- If not, what are the exceptions and why?
What checks do you perform before you start work?
Two crewmen were on the upper deck closing ventilation flaps. One of the crank handles was over rotated, detached and hit one of the crewman, seriously injuring his leg.