-
What happened?
On a flare field, flare pulsations were noted by the control room operator via closed circuit television (CCTV).
Marine technicians reported loud banging coming from the same location (around the same time pulsations were noted).
Field operator investigated and noted irregular activity on flare field A’s wet gas runners.
Shortly after this, the same operator reported hot pipework on the flare field’s wet gas common header.
Emergency response protocols were initiated. The flare header reverse burn was extinguished by diverting wet CO2 from the acid gas incinerator.
Wet gas common flare header sustained paint blistering.
No injuries to workers, loss of containment, or environmental impacts.
-
Why did it happen?
Both 24VDC redundant power supply units used for the programmable logic controller input/output (PLC I/O) modules shut down.
- This meant that the wet gas system staging valves failed ‘open’ as designed, and the flare field A blower tripped.
- This reduced flare header pressure to neutral or slightly negative, which allowed reverse burn to occur.
- Power loss affected PLC I/O chassis communication to the distributed control system (DCS) - it indicated normal status.
Weak signals such as minor flare irregularities (27 hours before the larger pulsation and noise from deflagration) were ignored.
Process operating guidelines did not cover response to staging valves failing open.
Operator round sheet did not include line items for staging valve position or blower status.
A previous hazard analysis considered it unlikely that the two PSUs would fail simultaneously.
-
What did they learn?
Personnel should NOT ignore warning signals – however minor they may seem.
Ensure that workers are aware of the appropriate responses to weak signals.
Ensure warning systems are in place and fully operational (power failure alarms, remote valve indicators, operator rounds etc.).
Be aware of the consequences of equipment failures (and what could happen if more systems fail simultaneously).
-
Ask yourself or your crew
What could they have done differently?
Have you ever ignored a warning sign/critical alarm? Why was that?
How can you stop yourself and your team from ignoring minor warning signs/alarms?
How well do you understand critical systems that you have not designed?
- Should the systems receive additional verifications? If yes, what type?
How do we update our warning systems to prevent significant incidents? How can we improve?
Add to homescreen
Content name
Select existing category:
Content name
New collection
Edit collection
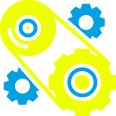
What happened?
On a flare field, flare pulsations were noted by the control room operator via closed circuit television (CCTV).
Marine technicians reported loud banging coming from the same location (around the same time pulsations were noted).
Field operator investigated and noted irregular activity on flare field A’s wet gas runners.
Shortly after this, the same operator reported hot pipework on the flare field’s wet gas common header.
Emergency response protocols were initiated. The flare header reverse burn was extinguished by diverting wet CO2 from the acid gas incinerator.
Wet gas common flare header sustained paint blistering.
No injuries to workers, loss of containment, or environmental impacts.
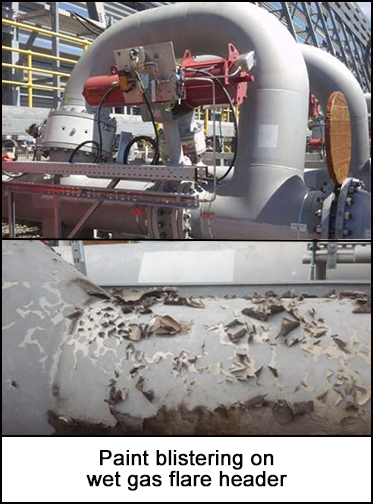
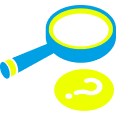
Why did it happen?
Both 24VDC redundant power supply units used for the programmable logic controller input/output (PLC I/O) modules shut down.
- This meant that the wet gas system staging valves failed ‘open’ as designed, and the flare field A blower tripped.
- This reduced flare header pressure to neutral or slightly negative, which allowed reverse burn to occur.
- Power loss affected PLC I/O chassis communication to the distributed control system (DCS) - it indicated normal status.
Weak signals such as minor flare irregularities (27 hours before the larger pulsation and noise from deflagration) were ignored.
Process operating guidelines did not cover response to staging valves failing open.
Operator round sheet did not include line items for staging valve position or blower status.
A previous hazard analysis considered it unlikely that the two PSUs would fail simultaneously.
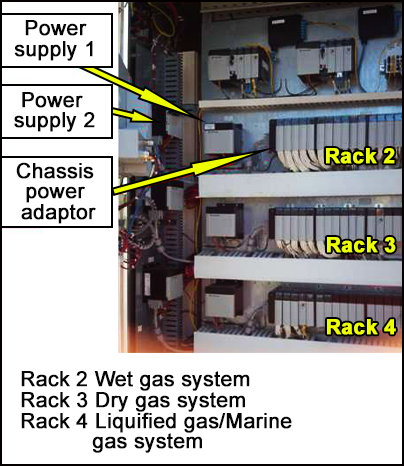
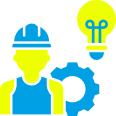
What did they learn?
Personnel should NOT ignore warning signals – however minor they may seem.
Ensure that workers are aware of the appropriate responses to weak signals.
Ensure warning systems are in place and fully operational (power failure alarms, remote valve indicators, operator rounds etc.).
Be aware of the consequences of equipment failures (and what could happen if more systems fail simultaneously).
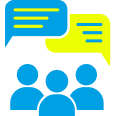
Ask yourself or your crew
What could they have done differently?
Have you ever ignored a warning sign/critical alarm? Why was that?
How can you stop yourself and your team from ignoring minor warning signs/alarms?
How well do you understand critical systems that you have not designed?
- Should the systems receive additional verifications? If yes, what type?
How do we update our warning systems to prevent significant incidents? How can we improve?
Flare pulsations and banging noises were noted in flare field A. Personnel investigated and discovered flare header reverse burn which was quickly extinguished.