-
What happened?
During pipelaying activities, injection moulded polypropylene (IMPP) equipment (used for field joint coating) became stuck.
Pipelaying activities were stopped and the crew dismantled the machine to investigate. The piston was stuck inside the accumulator chamber (see image).
The heating elements were energised to help pull out the piston. When extracting the piston, a cloud of flammable vapour and fine polypropylene droplets blew out from the accumulator chamber.
The cloud ignited, resulting in a flash fire.
The fire was extinguished by the barge crew. Fourteen people were injured and transferred to hospital. One injured person later died.
-
Why did it happen?
The crew connected the IMPP equipment built-in heating system to an external power supply to extract the piston. This resulted in loss of control of the temperature inside the accumulator and overheated the polypropylene accumulated inside (see image).
The task of extracting the piston was not covered by a procedure nor included in the user manual.
The IMPP equipment was regarded as a ‘foreign’ piece of equipment and not something under the accountability of the vessel management team.
It was unclear who was accountable for the equipment in terms of repair/maintenance activities.
-
What did they learn?
Custom-made production equipment should be always provided with an operation and maintenance manual.
Ensure that the handover of equipment includes a formal transfer of all documentation.
The behaviour of chemicals and fluids processed by the equipment should be fully analysed and reviewed for deviations from operating conditions.
The control of work package should always be consistent with the task in hand and revised if a change occurs or inconsistencies are identified.
-
Ask yourself or your crew
How can something like this happen here?
Identify equipment that we use that is custom-made, or equipment where it is unclear who is responsible for maintaining it.
How do we know we have all the documentation for our equipment?
What should we do if equipment breaks down, or if the plan for the job needs to change?
Add to homescreen
Content name
Select existing category:
Content name
New collection
Edit collection
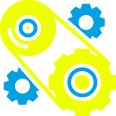
What happened?
During pipelaying activities, injection moulded polypropylene (IMPP) equipment (used for field joint coating) became stuck.
Pipelaying activities were stopped and the crew dismantled the machine to investigate. The piston was stuck inside the accumulator chamber (see image).
The heating elements were energised to help pull out the piston. When extracting the piston, a cloud of flammable vapour and fine polypropylene droplets blew out from the accumulator chamber.
The cloud ignited, resulting in a flash fire.
The fire was extinguished by the barge crew. Fourteen people were injured and transferred to hospital. One injured person later died.
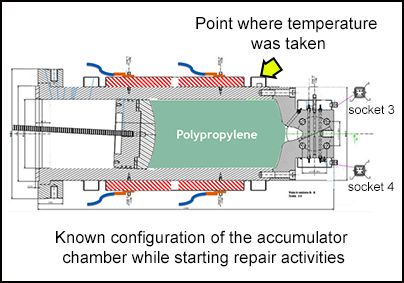
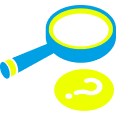
Why did it happen?
The crew connected the IMPP equipment built-in heating system to an external power supply to extract the piston. This resulted in loss of control of the temperature inside the accumulator and overheated the polypropylene accumulated inside (see image).
The task of extracting the piston was not covered by a procedure nor included in the user manual.
The IMPP equipment was regarded as a ‘foreign’ piece of equipment and not something under the accountability of the vessel management team.
It was unclear who was accountable for the equipment in terms of repair/maintenance activities.
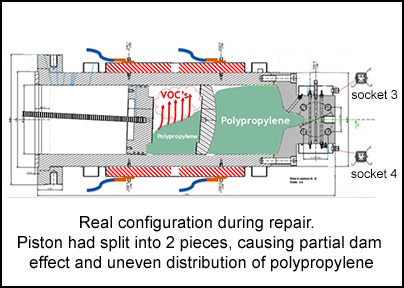
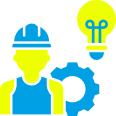
What did they learn?
Custom-made production equipment should be always provided with an operation and maintenance manual.
Ensure that the handover of equipment includes a formal transfer of all documentation.
The behaviour of chemicals and fluids processed by the equipment should be fully analysed and reviewed for deviations from operating conditions.
The control of work package should always be consistent with the task in hand and revised if a change occurs or inconsistencies are identified.
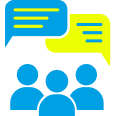
Ask yourself or your crew
How can something like this happen here?
Identify equipment that we use that is custom-made, or equipment where it is unclear who is responsible for maintaining it.
How do we know we have all the documentation for our equipment?
What should we do if equipment breaks down, or if the plan for the job needs to change?
During pipelaying activities, equipment used for field joint coating got stuck inside the accumulator chamber. Using heat to extract it, a cloud of flammable vapour blew out and started a fire.