-
What happened?
The fluid was trapped between a check valve and closed tank valves at a central tank battery.
The check valve top clamp failed, releasing oil to secondary containment.
The release was found by a truck driver and reported.
A production specialist advised pulling the emergency shutdown to stop the release.
The shutdown did not initiate well kill, and the release continued.
The production specialist then contacted a field specialist who instructed how to initiate the good kill process on the human-machine interface (HMI) screen.
The spill was subsequently stopped.
-
Why did it happen?
Facility design did not allow for production into tank 1 (T-1 on diagram) without trapping fluid downstream of a check valve.
The failed check valve was certified up to 720 pounds per square inch (psi). No material defects were identified to cause failure. Testing has shown pressure swings up to 3400 psi due to thermal expansion. Accounting for outside temperature, piping and valve pressure was estimated at ~ 2000 psi.
Trapped fluid combined with the increased outside temperature of 32 degrees C (90 degrees F), created a thermal expansion hazard, causing the check valve top clamp failure.
Procedures did not caution that valve configurations can create thermal expansion hazards.
Personnel did not identify the trapped fluid on the system or the consequences of thermal expansion.
Emergency shutdown button was not configured into the programmable logic controller to initiate well kill the process.
-
What did they learn?
Review facility designs to determine if all existing check valves are needed.
Ensure correct placement of the check valve and block valve to eliminate trapped fluid and conditions for thermal expansion hazard.
Ensure operating procedures caution against valve configurations that can trap fluid and create conditions for thermal expansion hazard.
Consider including notes defining thermal expansion, associated hazards and how to eliminate them.
Ensure equipment inspection/testing programmes are in place and include verification of emergency shutdown testing and functionality.
-
Ask yourself or your crew
How can something like this happen here?
If in doubt of the facility design, where can you find all the necessary diagrams?
What thermal expansion hazards might we encounter today?
What improvements to procedures or ways of working can we make to account for thermal expansion hazards?
How is the good kill procedure initiated on your site? How do you know that it works?
Add to homescreen
Content name
Select existing category:
Content name
New collection
Edit collection
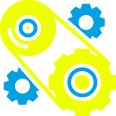
What happened?
The fluid was trapped between a check valve and closed tank valves at a central tank battery.
The check valve top clamp failed, releasing oil to secondary containment.
The release was found by a truck driver and reported.
A production specialist advised pulling the emergency shutdown to stop the release.
The shutdown did not initiate well kill, and the release continued.
The production specialist then contacted a field specialist who instructed how to initiate the good kill process on the human-machine interface (HMI) screen.
The spill was subsequently stopped.
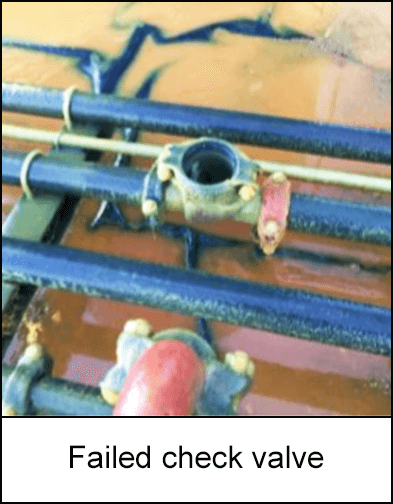
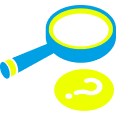
Why did it happen?
Facility design did not allow for production into tank 1 (T-1 on diagram) without trapping fluid downstream of a check valve.
The failed check valve was certified up to 720 pounds per square inch (psi). No material defects were identified to cause failure. Testing has shown pressure swings up to 3400 psi due to thermal expansion. Accounting for outside temperature, piping and valve pressure was estimated at ~ 2000 psi.
Trapped fluid combined with the increased outside temperature of 32 degrees C (90 degrees F), created a thermal expansion hazard, causing the check valve top clamp failure.
Procedures did not caution that valve configurations can create thermal expansion hazards.
Personnel did not identify the trapped fluid on the system or the consequences of thermal expansion.
Emergency shutdown button was not configured into the programmable logic controller to initiate well kill the process.
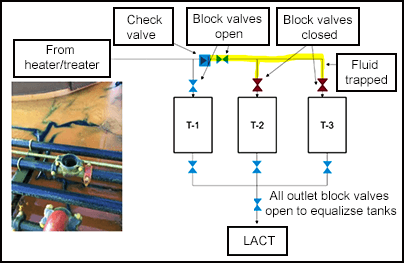
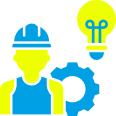
What did they learn?
Review facility designs to determine if all existing check valves are needed.
Ensure correct placement of the check valve and block valve to eliminate trapped fluid and conditions for thermal expansion hazard.
Ensure operating procedures caution against valve configurations that can trap fluid and create conditions for thermal expansion hazard.
Consider including notes defining thermal expansion, associated hazards and how to eliminate them.
Ensure equipment inspection/testing programmes are in place and include verification of emergency shutdown testing and functionality.
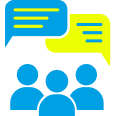
Ask yourself or your crew
How can something like this happen here?
If in doubt of the facility design, where can you find all the necessary diagrams?
What thermal expansion hazards might we encounter today?
What improvements to procedures or ways of working can we make to account for thermal expansion hazards?
How is the good kill procedure initiated on your site? How do you know that it works?
A check valve top clamp located at a central tank battery failed, releasing oil to secondary containment. The emergency shutdown did not stop the release. The spill was subsequently stopped by activating the well kill on the human-machine interface (HMI) screen.