-
What happened?
Two operators were lining up high pressure (65 barg/940 psig) liquid oxygen (LOX) injection to an air separation unit.
To equalise the pressure across the gate valve, the operators cracked open a 1 inch globe valve on the bypass around an 8 inch cryogenic gate valve.
A flash fire occurred and the two operators suffered severe burns. They both died from the injuries in the following months.
-
Why did it happen?
Flammable silicon oil from the polytetrafluoroethylene/graphite packing contaminated the internal surfaces of the gate valve.
Flow induced vibration occurred when opening the 1 inch valve. The impact and heating from the vibration generated enough energy to ignite the contaminant in the valve.
The company had design standards for gaseous oxygen valves, but not for liquid oxygen valves and relied on specialist vendor specifications.
-
What did they learn?
Polytetrafluoroethylene/graphite packing materials and hydrocarbon based grease are not suitable for oxygen service at high pressure.
Very little energy is required to ignite oils in pure oxygen (approximately 7 Joules). No severe vibrations or high noise levels should be observed in piping and/or valves.
Protection measures must be in place and adequate for the work:
- protection screens
- valve extensions
- remote valve operations
- escape routes
Operators must have sufficient information to assess actual process conditions (e.g. differential pressure).
Valve identification should be available when process piping is invisible (e.g. located inside a cold box).
High pressure oxygen systems have specific design and operating hazards which require specialist review. Critical operation procedures must be reviewed and signed off and the latest procedures must be used.
Only purpose-designed oxygen throttling valves must be used in throttling service (e.g. during process unit pressurisation).
System components must be tested and certified by recognised authorities. Quality assurance, quality control and cleanliness are critically important.
-
Ask yourself or your crew
What other actions could have been taken?
How can something like this happen here?
How do we recognise when we are working with pure oxygen?
How do we recognise vibrations and/or high noise levels in piping and/or valves?
What protection measures do we have in place? What needs improving?
Add to homescreen
Content name
Select existing category:
Content name
New collection
Edit collection
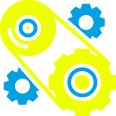
What happened?
Two operators were lining up high pressure (65 barg/940 psig) liquid oxygen (LOX) injection to an air separation unit.
To equalise the pressure across the gate valve, the operators cracked open a 1 inch globe valve on the bypass around an 8 inch cryogenic gate valve.
A flash fire occurred and the two operators suffered severe burns. They both died from the injuries in the following months.
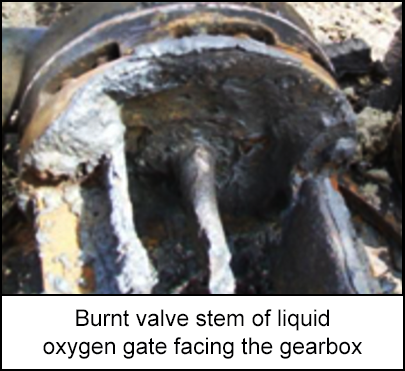
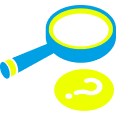
Why did it happen?
Flammable silicon oil from the polytetrafluoroethylene/graphite packing contaminated the internal surfaces of the gate valve.
Flow induced vibration occurred when opening the 1 inch valve. The impact and heating from the vibration generated enough energy to ignite the contaminant in the valve.
The company had design standards for gaseous oxygen valves, but not for liquid oxygen valves and relied on specialist vendor specifications.
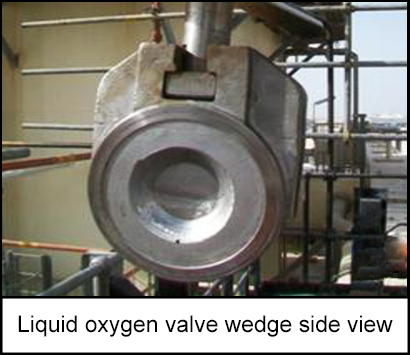
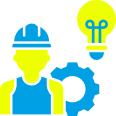
What did they learn?
Polytetrafluoroethylene/graphite packing materials and hydrocarbon based grease are not suitable for oxygen service at high pressure.
Very little energy is required to ignite oils in pure oxygen (approximately 7 Joules). No severe vibrations or high noise levels should be observed in piping and/or valves.
Protection measures must be in place and adequate for the work:
- protection screens
- valve extensions
- remote valve operations
- escape routes
Operators must have sufficient information to assess actual process conditions (e.g. differential pressure).
Valve identification should be available when process piping is invisible (e.g. located inside a cold box).
High pressure oxygen systems have specific design and operating hazards which require specialist review. Critical operation procedures must be reviewed and signed off and the latest procedures must be used.
Only purpose-designed oxygen throttling valves must be used in throttling service (e.g. during process unit pressurisation).
System components must be tested and certified by recognised authorities. Quality assurance, quality control and cleanliness are critically important.
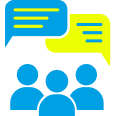
Ask yourself or your crew
What other actions could have been taken?
How can something like this happen here?
How do we recognise when we are working with pure oxygen?
How do we recognise vibrations and/or high noise levels in piping and/or valves?
What protection measures do we have in place? What needs improving?
Two operators were lining up high pressure liquid oxygen injection to an air separation unit. A flash fire occurred, and the two operators suffered severe burns. They both died from the injuries in the following months.