-
What happened?
Engineers were repairing a cylinder on a main engine of a liquefied natural gas (LNG) carrier.
They were working in a gas valve unit (GVU) room located within the machinery space of the dual fuel, diesel-electric propelled vessel.
The air intake and exhaust system in the GVUs is designed to continuously ventilate and exchange the air within the space to reduce fire, explosion, and hazardous atmosphere risks from developing, if gas leaks should occur from the equipment.
The ventilation system creates a vacuum within the room when the two access doors are shut.
While removing an expansion bellow, an O-ring that was separating its inner and outer sections was damaged.
No one noticed until a crew member was making a round in the GVU room after the engine had been operating.
After entering the GVU room, he was overcome by methane gas and nearly lost consciousness. He was able to leave room safely.
The room atmosphere was measured at 22% methane and 17% oxygen by volume (unsafe levels).
-
Why did it happen?
The installed methane sensor failed to detect the accumulation of gas – although it did not malfunction.
Engineers had rigged a hose from the outlet of the gas evacuation fan, across the GVU room, to the sensor at the entrance exhaust duct.
This unauthorised arrangement disabled the sensor’s ability to detect methane leakages from other components in the GVU room.
-
What did they learn?
Verify that all gas monitors and sensors are working correctly.
Ensure that any modifications have received the proper engineering reviews, approvals, and supporting documentation.
Increase awareness regarding any system modifications, whether deemed potentially hazardous or not.
- Workers should be aware of any system modifications that have been made to their work area.
-
Ask yourself or your crew
What is the worst that could have happened?
How do you check that all the sensors in your equipment rooms are functioning correctly?
Are there any modifications to your work area?
- How do you know they are safe?
- Are they documented?
What other hazards are there when working in vessel engine rooms?
What procedures do we have in place to prevent this from happening here? How can we improve?
Add to homescreen
Content name
Select existing category:
Content name
New collection
Edit collection
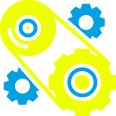
What happened?
Engineers were repairing a cylinder on a main engine of a liquefied natural gas (LNG) carrier.
They were working in a gas valve unit (GVU) room located within the machinery space of the dual fuel, diesel-electric propelled vessel.
The air intake and exhaust system in the GVUs is designed to continuously ventilate and exchange the air within the space to reduce fire, explosion, and hazardous atmosphere risks from developing, if gas leaks should occur from the equipment.
The ventilation system creates a vacuum within the room when the two access doors are shut.
While removing an expansion bellow, an O-ring that was separating its inner and outer sections was damaged.
No one noticed until a crew member was making a round in the GVU room after the engine had been operating.
After entering the GVU room, he was overcome by methane gas and nearly lost consciousness. He was able to leave room safely.
The room atmosphere was measured at 22% methane and 17% oxygen by volume (unsafe levels).
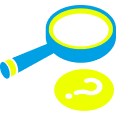
Why did it happen?
The installed methane sensor failed to detect the accumulation of gas – although it did not malfunction.
Engineers had rigged a hose from the outlet of the gas evacuation fan, across the GVU room, to the sensor at the entrance exhaust duct.
This unauthorised arrangement disabled the sensor’s ability to detect methane leakages from other components in the GVU room.
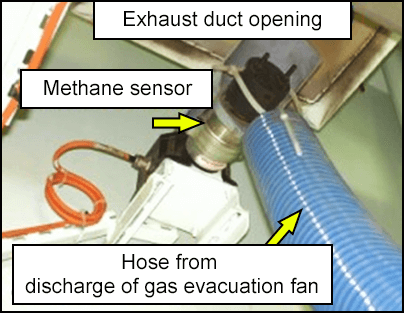
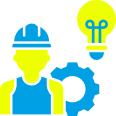
What did they learn?
Verify that all gas monitors and sensors are working correctly.
Ensure that any modifications have received the proper engineering reviews, approvals, and supporting documentation.
Increase awareness regarding any system modifications, whether deemed potentially hazardous or not.
- Workers should be aware of any system modifications that have been made to their work area.
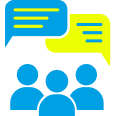
Ask yourself or your crew
What is the worst that could have happened?
How do you check that all the sensors in your equipment rooms are functioning correctly?
Are there any modifications to your work area?
- How do you know they are safe?
- Are they documented?
What other hazards are there when working in vessel engine rooms?
What procedures do we have in place to prevent this from happening here? How can we improve?
Engineers were repairing a cylinder of a main engine vessel, within a gas valve unit (GVU) room. While they were replacing expansion bellows, an O-ring, separating its inner and outer sections, was damaged, allowing methane gas to enter the GVU room.