-
What happened?
An offshore installation manager (OIM) was doing final checks of an unmanned offshore platform.
The OIM smelled gas in the room of the gas generator.
The generator had tripped, but the fuel gas kept flowing in because the two remote operated valves in the fuel supply line failed to close on demand.
800 kg of fuel gas had leaked through the air inlet to the generator’s enclosure.
The OIM stopped the fuel supply to the gas generator by closing the hand valve in the supply line.
-
Why did it happen?
The remote operated shutdown valves did not close on demand as the actuators of the valves were stuck in the open position.
Humidity in the air caused instrument air system components (actuators, solenoids) to become corroded.
Failures in technical integrity - the instrument air system auto-drain was not operated/maintained properly, and remote operations were functioning poorly.
Failures in operating integrity - ineffective alarm system management - earlier failures in the gas generator were not identified.
Failures in design integrity/management of change - the installation had previously been changed from a manned to unmanned operation. The effects of this change were not fully recognised.
- Incompatibility between the unmanned mode of operation and the design of the installation.
-
What did they learn?
Review the maintenance strategy plan.
Dry and ‘clean’ the instrument air system. Implement performance standard for instrument air.
Periodically check and replace faulty or degraded equipment (actuators, solenoids, cooling and ventilation systems).
Revisit the principles for switching from manned to unmanned operations. Bring systems in line with other normally unmanned installation (NUI) platforms.
Increase knowledge levels on integrated automated systems (IAS) in the NUI team.
-
Ask yourself or your crew
What is the worst that could have happened?
What are the impacts of corrosion on offshore installations? How can this be minimised?
What are the main differences between running a manned vs. unmanned installation?
What is our maintenance and testing strategy for remotely operated offshore platforms equipment? How can it be improved?
What is the emergency response procedure for gas leaks on offshore platforms?
Add to homescreen
Content name
Select existing category:
Content name
New collection
Edit collection
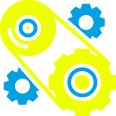
What happened?
An offshore installation manager (OIM) was doing final checks of an unmanned offshore platform.
The OIM smelled gas in the room of the gas generator.
The generator had tripped, but the fuel gas kept flowing in because the two remote operated valves in the fuel supply line failed to close on demand.
800 kg of fuel gas had leaked through the air inlet to the generator’s enclosure.
The OIM stopped the fuel supply to the gas generator by closing the hand valve in the supply line.
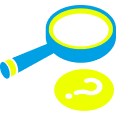
Why did it happen?
The remote operated shutdown valves did not close on demand as the actuators of the valves were stuck in the open position.
Humidity in the air caused instrument air system components (actuators, solenoids) to become corroded.
Failures in technical integrity - the instrument air system auto-drain was not operated/maintained properly, and remote operations were functioning poorly.
Failures in operating integrity - ineffective alarm system management - earlier failures in the gas generator were not identified.
Failures in design integrity/management of change - the installation had previously been changed from a manned to unmanned operation. The effects of this change were not fully recognised.
- Incompatibility between the unmanned mode of operation and the design of the installation.
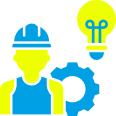
What did they learn?
Review the maintenance strategy plan.
Dry and ‘clean’ the instrument air system. Implement performance standard for instrument air.
Periodically check and replace faulty or degraded equipment (actuators, solenoids, cooling and ventilation systems).
Revisit the principles for switching from manned to unmanned operations. Bring systems in line with other normally unmanned installation (NUI) platforms.
Increase knowledge levels on integrated automated systems (IAS) in the NUI team.
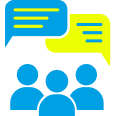
Ask yourself or your crew
What is the worst that could have happened?
What are the impacts of corrosion on offshore installations? How can this be minimised?
What are the main differences between running a manned vs. unmanned installation?
What is our maintenance and testing strategy for remotely operated offshore platforms equipment? How can it be improved?
What is the emergency response procedure for gas leaks on offshore platforms?
An offshore installation manager (OIM) smelled gas on an unmanned offshore platform. The gas generator had tripped, but gas had continued to flow in. 800 kg of fuel gas had leaked through the air inlet to the generator’s enclosure.