-
What happened?
A cable laying vessel was laying array cable. The first end of the cable had been pulled into the tower and the cable pull-in team had installed the temporary hand off clamp.
At the same time the vessel continued to lay towards the next foundation. At 880m (~0.5 miles) from the foundation the dynamic positioning operator noticed a warning coming from the dynamic positioning (DP) system and requested a controlled stop. At the same time, the DP system accelerated the vessel ahead 30m (~100ft).
The cable tension increased up to a recorded 19.8Te and was held for a period of 25 seconds. This corresponds to a tension of 197kN, which is above the supplier’s cable handling parameters of 150kN.
When the cable was checked on the pulled in end it was found that it had been pulled through the temporary hang-off by 2m (~6.5ft). In addition, some secondary rigging straps had broken, both with clear damage to the cable. There was also minor damage to the structure and the cabling could have easily injured the work crew who were still on the turbine tower (but were not in the structure at the time).
-
Why did it happen?
The tower team were still on the turbine and packing away kit on the external platform at the time of the incident. It was not planned for the team to still be within the structure at this time.
The dynamic positioning trial findings and subsequent reports from the dynamic positioning auditor showed that the run-off issue was related to the dynamic positioning routine being used at the time of the incident.
-
What did they learn?
Hazard identification risk assessment (HIRA) reviews resulted in changes to:
- the cable lay vessel and tower team procedures
- the tensioner pressure settings.
The tower teams should not be within the transition piece structure when the vessel is in motion.
The dynamic positioning routine used at the time of the incident will not be used in the future.
-
Ask yourself or your crew
How could something like this happen during our cable laying routine?
How can we ensure all persons that could be in ‘harm’s way’ are outside the exclusion zone?
What systems do we have in place to notify all personnel and make them aware of operations taking place in their area (that might impact on their work, or put them at risk)?
Add to homescreen
Content name
Select existing category:
Content name
New collection
Edit collection
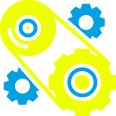
What happened?
A cable laying vessel was laying array cable. The first end of the cable had been pulled into the tower and the cable pull-in team had installed the temporary hand off clamp.
At the same time the vessel continued to lay towards the next foundation. At 880m (~0.5 miles) from the foundation the dynamic positioning operator noticed a warning coming from the dynamic positioning (DP) system and requested a controlled stop. At the same time, the DP system accelerated the vessel ahead 30m (~100ft).
The cable tension increased up to a recorded 19.8Te and was held for a period of 25 seconds. This corresponds to a tension of 197kN, which is above the supplier’s cable handling parameters of 150kN.
When the cable was checked on the pulled in end it was found that it had been pulled through the temporary hang-off by 2m (~6.5ft). In addition, some secondary rigging straps had broken, both with clear damage to the cable. There was also minor damage to the structure and the cabling could have easily injured the work crew who were still on the turbine tower (but were not in the structure at the time).
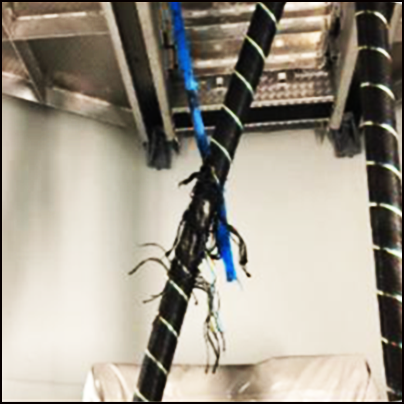
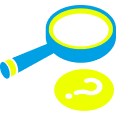
Why did it happen?
The tower team were still on the turbine and packing away kit on the external platform at the time of the incident. It was not planned for the team to still be within the structure at this time.
The dynamic positioning trial findings and subsequent reports from the dynamic positioning auditor showed that the run-off issue was related to the dynamic positioning routine being used at the time of the incident.
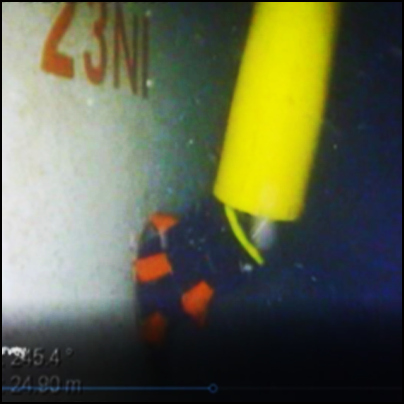
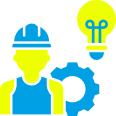
What did they learn?
Hazard identification risk assessment (HIRA) reviews resulted in changes to:
- the cable lay vessel and tower team procedures
- the tensioner pressure settings.
The tower teams should not be within the transition piece structure when the vessel is in motion.
The dynamic positioning routine used at the time of the incident will not be used in the future.
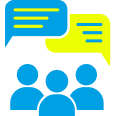
Ask yourself or your crew
How could something like this happen during our cable laying routine?
How can we ensure all persons that could be in ‘harm’s way’ are outside the exclusion zone?
What systems do we have in place to notify all personnel and make them aware of operations taking place in their area (that might impact on their work, or put them at risk)?
While laying array cable, the cable laying vessel experienced a dynamic positioning (DP) runoff. The first end of the cable had been pulled into the tower and the cable pull-in team installed the temporary hang off clamp. At the time of the incident the tower team were still on the turbine and packing away kit on the external platform. At the same time, the vessel continued to lay towards the next foundation.