-
What happened?
A worker was preparing to transfer concrete from a mixer truck to a concrete pump truck.
He was setting the chute of the mixer truck to the hopper of the pump truck for the transfer when the truck started to move backwards.
The worker was pinched between the mixer truck and the pump truck.
He received first aid treatment on site and was released the same day.
-
Why did it happen?
Worker had to adjust the chute using a temporary handle because the hydraulic system was not working on the mixer truck - putting himself in the line of fire.
Truck driver waited 8 hours before being allocated a delivery that resulted in him losing focus.
- He didn’t engage the handbrake and did not realise the footbrake wasn’t fully engaged.
Miscommunication between truck driver and injured person (IP) regarding the sequence for positioning the two trucks.
Hazard of workers being positioned between two vehicles was not identified.
- Job safety analysis (JSA) only covered activities at the batching plant, not the supply of concrete to each worksite.
-
What did they learn?
Ensure all trucks in use are fully functional – workers should not need to use temporary workarounds.
- Consider tagging and quarantining broken and unsafe equipment - to ensure it will not be operated.
Consider using wheel chocks as a hard barrier to prevent inadvertent vehicle movement.
Consider using spotters for activities done by “lone workers”.
Workers/teams should communicate clearly amongst themselves to avoid misunderstandings (e.g. sequence of steps, position during activity etc.).
Confirm that the JSA covers all activities that need to be undertaken.
- Include supply of concrete to each subcontractor on site in procedures and JSA.
Undertake full risk assessment of all activities – including hazards and human factors.
Ensure all personnel understands the risks associated with their tasks.
-
Ask yourself or your crew
Do our existing procedures and JSAs for concrete operations include supply of concrete on site?
Do you have a process for tagging and quarantining broken/unsafe equipment to ensure they will not be used? If not, should you?
How do you minimise the risks of mental fatigue associated with carrying out repetitive tasks?
What can you do to make your workforce aware of the potential risks of lack of communication?
What measures do we have in place to prevent this from happening here? How can we improve?
Add to homescreen
Content name
Select existing category:
Content name
New collection
Edit collection
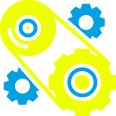
What happened?
A worker was preparing to transfer concrete from a mixer truck to a concrete pump truck.
He was setting the chute of the mixer truck to the hopper of the pump truck for the transfer when the truck started to move backwards.
The worker was pinched between the mixer truck and the pump truck.
He received first aid treatment on site and was released the same day.
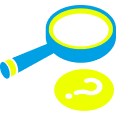
Why did it happen?
Worker had to adjust the chute using a temporary handle because the hydraulic system was not working on the mixer truck - putting himself in the line of fire.
Truck driver waited 8 hours before being allocated a delivery that resulted in him losing focus.
- He didn’t engage the handbrake and did not realise the footbrake wasn’t fully engaged.
Miscommunication between truck driver and injured person (IP) regarding the sequence for positioning the two trucks.
Hazard of workers being positioned between two vehicles was not identified.
- Job safety analysis (JSA) only covered activities at the batching plant, not the supply of concrete to each worksite.
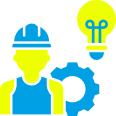
What did they learn?
Ensure all trucks in use are fully functional – workers should not need to use temporary workarounds.
- Consider tagging and quarantining broken and unsafe equipment - to ensure it will not be operated.
Consider using wheel chocks as a hard barrier to prevent inadvertent vehicle movement.
Consider using spotters for activities done by “lone workers”.
Workers/teams should communicate clearly amongst themselves to avoid misunderstandings (e.g. sequence of steps, position during activity etc.).
Confirm that the JSA covers all activities that need to be undertaken.
- Include supply of concrete to each subcontractor on site in procedures and JSA.
Undertake full risk assessment of all activities – including hazards and human factors.
Ensure all personnel understands the risks associated with their tasks.
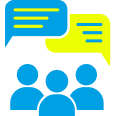
Ask yourself or your crew
Do our existing procedures and JSAs for concrete operations include supply of concrete on site?
Do you have a process for tagging and quarantining broken/unsafe equipment to ensure they will not be used? If not, should you?
How do you minimise the risks of mental fatigue associated with carrying out repetitive tasks?
What can you do to make your workforce aware of the potential risks of lack of communication?
What measures do we have in place to prevent this from happening here? How can we improve?
A worker was preparing to transfer concrete from a mixer truck to a concrete pump truck. He was setting the chute of the mixer truck to the hopper of the pump truck for the transfer when the truck started to move backwards. The worker was pinched between the mixer truck and the pump truck.