-
What happened?
A crew were being transferred to an offshore wind installation using a walk-to-work (W2W) gangway system.
The weather and sea state at the time were well within the working limits.
After the first person transferred, the gangway system moved up and down, slipping upwards from its push-on point.
It hit a floor grating which came loose, resulting in minor damage.
Transfer was aborted, and further transfers were done using a CTV (crew transfer vessel).
-
Why did it happen?
Investigation of the software control for the system’s active motion compensation (AMC) revealed that the performance for boom motion was not optimal.
- Due to reduced accuracy of the AMC, the vertical force acting on the connection point led to connection failure.
Operator and vessel captain agreed to start operations although during pre-job testing the system seemed to react slower than normal.
- The decision to proceed was based on good performance during previous tests earlier that day.
Slight differences in the push-on point design on this specific installation (a substation) compared to turbine towers (see image).
-
What did they learn?
Active motion compensation (AMC) system performance should be verified during annual inspection.
Before connection, position the gangway approximately 1m (3ft) from connection point, visually verify that AMC is stable and that the control error is within reasonable limits.
Verify that the connection point is designed to fit the gangway with respect to shape and load.
-
Ask yourself or your crew
What was the worst that could have happened?
What procedures do you follow for connecting / using gangway systems?
How can you verify that the connection point is designed to fit the gangway?
How do we check that the software we use for automated systems is performing within parameters?
- How often do we test that? Should we do it more often?
Add to homescreen
Content name
Select existing category:
Content name
New collection
Edit collection
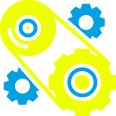
What happened?
A crew were being transferred to an offshore wind installation using a walk-to-work (W2W) gangway system.
The weather and sea state at the time were well within the working limits.
After the first person transferred, the gangway system moved up and down, slipping upwards from its push-on point.
It hit a floor grating which came loose, resulting in minor damage.
Transfer was aborted, and further transfers were done using a CTV (crew transfer vessel).
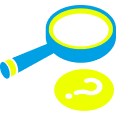
Why did it happen?
Investigation of the software control for the system’s active motion compensation (AMC) revealed that the performance for boom motion was not optimal.
- Due to reduced accuracy of the AMC, the vertical force acting on the connection point led to connection failure.
Operator and vessel captain agreed to start operations although during pre-job testing the system seemed to react slower than normal.
- The decision to proceed was based on good performance during previous tests earlier that day.
Slight differences in the push-on point design on this specific installation (a substation) compared to turbine towers (see image).
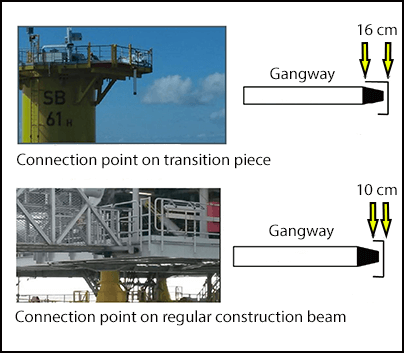
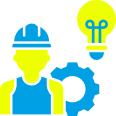
What did they learn?
Active motion compensation (AMC) system performance should be verified during annual inspection.
Before connection, position the gangway approximately 1m (3ft) from connection point, visually verify that AMC is stable and that the control error is within reasonable limits.
Verify that the connection point is designed to fit the gangway with respect to shape and load.
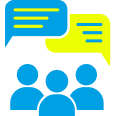
Ask yourself or your crew
What was the worst that could have happened?
What procedures do you follow for connecting / using gangway systems?
How can you verify that the connection point is designed to fit the gangway?
How do we check that the software we use for automated systems is performing within parameters?
- How often do we test that? Should we do it more often?
Workers were being transferred to an offshore wind installation using a walk-to-work (W2W) gangway system. After the first worker transferred safely, the gangway system moved up and down, slipping from its push-on point. The transfer was aborted.