-
What happened?
An excavator was loading a 30cm x 12m (12in x 40ft) uncoated line pipe on a transport trailer.
As the excavator was slewing towards the trailer, the vacuum lifter unit holding the pipe lost suction.
The 1.8Te pipe was dropped 2m (6.5ft) to the ground.
No alarms sounded, and the excavator operator had no warning of the loss of suction.
No injuries occurred as all workers were away from the line of fire.
-
Why did it happen?
Vacuum seal on the ‘shoe’ was worn out after moving over 5000 lengths of line pipe.
Half of the vacuum seal had just been replaced earlier that day - seal was ineffective and inconsistent along the pipe.
A guide tab which helps the operator align the vacuum shoe across the apex and centre line of the line pipe was missing from the unit’s head.
- This caused the unit to seal a few degrees outside of parallel along the centre of the pipe and contributed to loss of suction pressure.
Alarms were tested and functioning during the pre-start checks but did not sound during the incident.
No routine testing performed on the vacuum unit to ensure it was holding pressure.
A full maintenance schedule was not provided by the equipment supplier.
-
What did they learn?
All workers must remain well clear of loads and always consider that the load could move and/or drop.
Workers operating vacuum units should have a full understanding of required maintenance, including replacement of consumables such as shoe rubber seals.
When using lifting devices that use suction pressure to hold the load, daily tests should be completed to confirm integrity:
- e.g. ‘ten for ten’ test where the load is being held for 10 minutes to confirm no greater loss that 10% of pressure.
Regular maintenance should verify that alarms function at correct levels for the work scope.
-
Ask yourself or your crew
Why did they replace only half of the seal?
- Is this normal practice? If not, what is the correct procedure for replacing seals on vacuum lifting units?
How often are consumables (i.e. rubber seals) tested on your equipment? Should we test more often (daily, weekly, other)?
- What tests should we perform?
What reason could there be for the alarms working during the pre-start test but did not sound during the lift?
How are drop zones established on our site?
- Are they clearly marked during lifting operations? If not, how can we improve?
Add to homescreen
Content name
Select existing category:
Content name
New collection
Edit collection
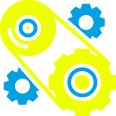
What happened?
An excavator was loading a 30cm x 12m (12in x 40ft) uncoated line pipe on a transport trailer.
As the excavator was slewing towards the trailer, the vacuum lifter unit holding the pipe lost suction.
The 1.8Te pipe was dropped 2m (6.5ft) to the ground.
No alarms sounded, and the excavator operator had no warning of the loss of suction.
No injuries occurred as all workers were away from the line of fire.
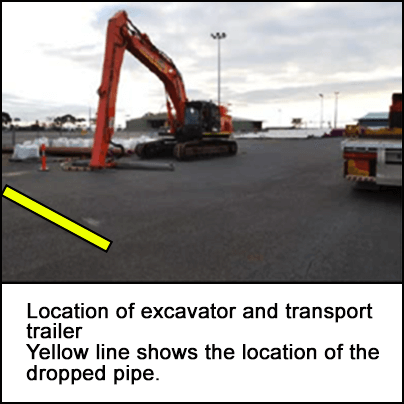
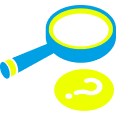
Why did it happen?
Vacuum seal on the ‘shoe’ was worn out after moving over 5000 lengths of line pipe.
Half of the vacuum seal had just been replaced earlier that day - seal was ineffective and inconsistent along the pipe.
A guide tab which helps the operator align the vacuum shoe across the apex and centre line of the line pipe was missing from the unit’s head.
- This caused the unit to seal a few degrees outside of parallel along the centre of the pipe and contributed to loss of suction pressure.
Alarms were tested and functioning during the pre-start checks but did not sound during the incident.
No routine testing performed on the vacuum unit to ensure it was holding pressure.
A full maintenance schedule was not provided by the equipment supplier.
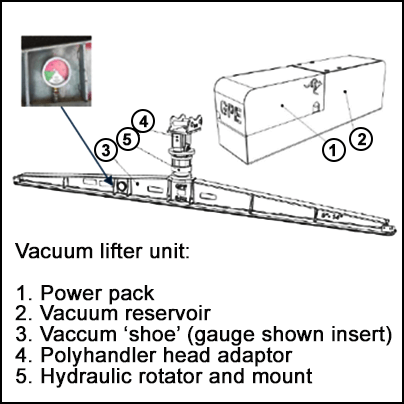
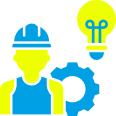
What did they learn?
All workers must remain well clear of loads and always consider that the load could move and/or drop.
Workers operating vacuum units should have a full understanding of required maintenance, including replacement of consumables such as shoe rubber seals.
When using lifting devices that use suction pressure to hold the load, daily tests should be completed to confirm integrity:
- e.g. ‘ten for ten’ test where the load is being held for 10 minutes to confirm no greater loss that 10% of pressure.
Regular maintenance should verify that alarms function at correct levels for the work scope.
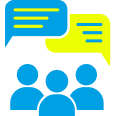
Ask yourself or your crew
Why did they replace only half of the seal?
- Is this normal practice? If not, what is the correct procedure for replacing seals on vacuum lifting units?
How often are consumables (i.e. rubber seals) tested on your equipment? Should we test more often (daily, weekly, other)?
- What tests should we perform?
What reason could there be for the alarms working during the pre-start test but did not sound during the lift?
How are drop zones established on our site?
- Are they clearly marked during lifting operations? If not, how can we improve?
An excavator was being used to load piping on a transport trailer. As the excavator was slewing towards the trailer, the vacuum lifter unit being used to hold the pipe lost suction.