-
What happened?
A worker was near an oily water pit when his personal gas detector alarm went off.
Gas detector indicated a 100% lower explosive limit (LEL) flammable atmosphere at 150mm from the pit.
Worker identified through elimination that the source of gas was the oily water drain line from the suction scrubber on the screw compressor.
He shut down the unit and informed line supervisor.
Previous check was successfully completed 19 hours before.
1,683 kg of gas could have been released in this time – based on a leak rate of 88.6 kg/h (estimated through process calculation).
No one was hurt or affected by the incident.
-
Why did it happen?
Mechanical instrument failure:
- Compressor scrubber level controller failed at the same time as the low-level safeguard.
- This resulted in a flow path to the oily water drain, which vented to atmosphere.
Inadequate proof testing procedures and proof testing execution.
Risk normalisation:
- Oily water pit was perceived to be a safe release point.
-
What did they learn?
Establish a hard barrier exclusion zone around the oily water pit.
Engineer/re-engineer the scrubber low level safeguarding function to reduce the likelihood of dangerous unrevealed failures.
Develop and execute specific proof test procedures for the scrubber low level safeguarding function.
Don’t normalise risks – the water pit was considered a safe release point.
Learn from previous incidents – a similar incident happened two months before on the same site.
-
Ask yourself or your crew
What is the worst that could have happened?
Have you experienced anything like this before? What happened?
What safety measures do we have on our site for gas leak prevention?
- How do we proof test the scrubber low level safeguarding function?
What risks are considered ‘acceptable’? Should they really be normalised?
Add to homescreen
Content name
Select existing category:
Content name
New collection
Edit collection
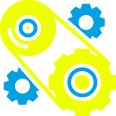
What happened?
A worker was near an oily water pit when his personal gas detector alarm went off.
Gas detector indicated a 100% lower explosive limit (LEL) flammable atmosphere at 150mm from the pit.
Worker identified through elimination that the source of gas was the oily water drain line from the suction scrubber on the screw compressor.
He shut down the unit and informed line supervisor.
Previous check was successfully completed 19 hours before.
1,683 kg of gas could have been released in this time – based on a leak rate of 88.6 kg/h (estimated through process calculation).
No one was hurt or affected by the incident.
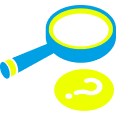
Why did it happen?
Mechanical instrument failure:
- Compressor scrubber level controller failed at the same time as the low-level safeguard.
- This resulted in a flow path to the oily water drain, which vented to atmosphere.
Inadequate proof testing procedures and proof testing execution.
Risk normalisation:
- Oily water pit was perceived to be a safe release point.
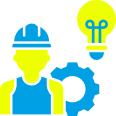
What did they learn?
Establish a hard barrier exclusion zone around the oily water pit.
Engineer/re-engineer the scrubber low level safeguarding function to reduce the likelihood of dangerous unrevealed failures.
Develop and execute specific proof test procedures for the scrubber low level safeguarding function.
Don’t normalise risks – the water pit was considered a safe release point.
Learn from previous incidents – a similar incident happened two months before on the same site.
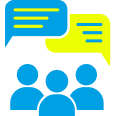
Ask yourself or your crew
What is the worst that could have happened?
Have you experienced anything like this before? What happened?
What safety measures do we have on our site for gas leak prevention?
- How do we proof test the scrubber low level safeguarding function?
What risks are considered ‘acceptable’? Should they really be normalised?
A worker was near an oily water pit when a gas detector indicated a 100% lower explosive limit (LEL) flammable atmosphere at 150mm. The source of gas was the oily water drain line. The unit was shut down.