-
What happened?
A pump coupling was replaced to eliminate high vibration.
14 months later, the pump's mechanical seal (single seal arrangement) failed, resulting in a fire ignited by jet fuel contacting the hot bearing housing.
The equipment and property were damaged. The incident had the potential for injury and environmental impact.
-
Why did it happen?
A test had not been carried out to confirm the effectiveness of the repairs made 14 months ago.
The seal failed due to a vibration-induced bearing failure caused by one or more of the following:
- The pump had previously operated with high vibration for several days.
- Misalignment of the pump/motor due to:
- pipe strain
- an ineffective previous alignment
- Presence of a foreign object (¾-inch nut) in the pump impeller leading to an imbalance.
-
What did they learn?
Create a rotating equipment return-to-service procedure that includes:
- mechanical personnel involvement
- a reinstallation checklist
- a vibration check as a step on the work order
- operator routine patrols
Evaluate the pump switching programme and validate that all pumps are included in the programme and operated long enough to collect vibration data. Develop a process for managing exceptions to the programme.
Establish requirements to check and document pipe strain and alignment following repairs.
Revise equipment closure procedures to verify the absence of loose hardware and debris.
-
Ask yourself or your crew
How can something like this happen here?
Think of an example where we didn’t verify the effectiveness of a repair.
How do you check for vibrations before return-to-service?
Are you personally responsible for testing? If not, who is and how do you know the equipment passed the tests and is safe to operate?
How can we improve our return-to-service procedures?
Add to homescreen
Content name
Select existing category:
Content name
New collection
Edit collection
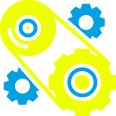
What happened?
A pump coupling was replaced to eliminate high vibration.
14 months later, the pump's mechanical seal (single seal arrangement) failed, resulting in a fire ignited by jet fuel contacting the hot bearing housing.
The equipment and property were damaged. The incident had the potential for injury and environmental impact.
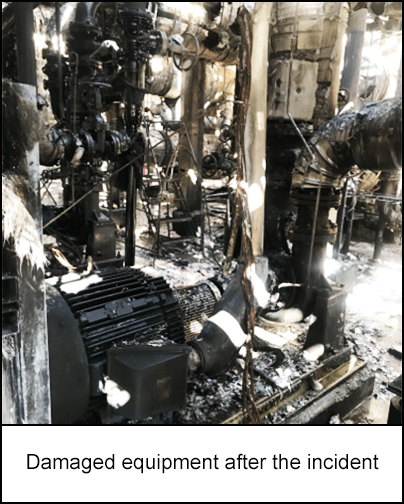
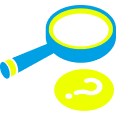
Why did it happen?
A test had not been carried out to confirm the effectiveness of the repairs made 14 months ago.
The seal failed due to a vibration-induced bearing failure caused by one or more of the following:
- The pump had previously operated with high vibration for several days.
- Misalignment of the pump/motor due to:
- pipe strain
- an ineffective previous alignment
- Presence of a foreign object (¾-inch nut) in the pump impeller leading to an imbalance.
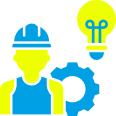
What did they learn?
Create a rotating equipment return-to-service procedure that includes:
- mechanical personnel involvement
- a reinstallation checklist
- a vibration check as a step on the work order
- operator routine patrols
Evaluate the pump switching programme and validate that all pumps are included in the programme and operated long enough to collect vibration data. Develop a process for managing exceptions to the programme.
Establish requirements to check and document pipe strain and alignment following repairs.
Revise equipment closure procedures to verify the absence of loose hardware and debris.
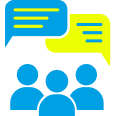
Ask yourself or your crew
How can something like this happen here?
Think of an example where we didn’t verify the effectiveness of a repair.
How do you check for vibrations before return-to-service?
Are you personally responsible for testing? If not, who is and how do you know the equipment passed the tests and is safe to operate?
How can we improve our return-to-service procedures?
Jet fuel was released from a pump mechanical seal and ignited when contacting the hot bearing housing. The equipment and property were damaged.