-
What happened?
During offshore operations, a 600kg (1322lbs) securing pin from a tiltable lay system (TLS) fell 16m (52ft) to the deck.
At the time of the incident there was an umbilical in the tower, but the umbilical was not being deployed.
No one was in was in the immediate area below the adjuster leg and no-one was injured.
If deployment operations had been ongoing and the top tension would have been above the survival capacity of one adjuster leg, there would have been potential for further consequences.
-
Why did it happen?
The keeper bolts slackened off, allowing the securing pin to fall to the deck.
The tower had been kept in operational position at times during transits – this allowed excess movement of the pin due to reduced load and increased dynamic movement.
The design made it difficult to lubricate the pin adequately – which may have caused excess friction.
The planned maintenance and inspection regime of the TLS was inadequate and unclear.
-
What did they learn?
Ensure the tower is kept in survival mode position during all transits (according to manufacturer’s recommendations).
Check the tightness of all critical bolts and pins throughout the tower.
Clearly define accurate inspection criteria for critical pins and securing mechanisms. Ensure planned maintenance requirements are updated.
Should something similar occur, consider:
- Performing a structural non-destructive testing (NDT) of pin connecting parts to verify sufficient load capacity and seaworthiness.
- Installing increased diameter anti-rotation locking key bolts to provide additional bolt shear strength if putting the adjuster leg back in place.
- Installing additional temporary bolt locking mechanisms on both adjuster leg pins locking key bolts to ensure vibration would not loosen the bolts before the permanent solution was ready.
-
Ask yourself or your crew
Is your equipment kept in ‘survival mode’ in transit / when not in use? If not, why is that?
What is our inspection regime for tiltable lay systems / similar equipment?
How often do we check all critical bolts, pins and lubricated lines and how do we record this?
How do we inspect hard to access areas?
What measures do we have in place to prevent this from happening here? How can we improve?
Add to homescreen
Content name
Select existing category:
Content name
New collection
Edit collection
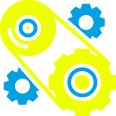
What happened?
During offshore operations, a 600kg (1322lbs) securing pin from a tiltable lay system (TLS) fell 16m (52ft) to the deck.
At the time of the incident there was an umbilical in the tower, but the umbilical was not being deployed.
No one was in was in the immediate area below the adjuster leg and no-one was injured.
If deployment operations had been ongoing and the top tension would have been above the survival capacity of one adjuster leg, there would have been potential for further consequences.
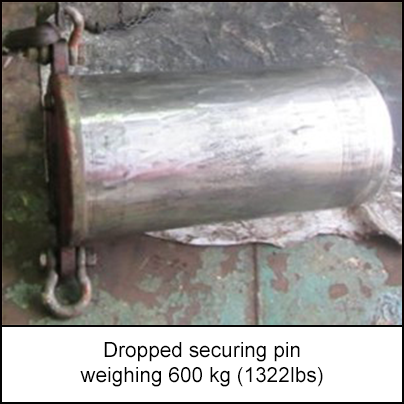
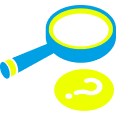
Why did it happen?
The keeper bolts slackened off, allowing the securing pin to fall to the deck.
The tower had been kept in operational position at times during transits – this allowed excess movement of the pin due to reduced load and increased dynamic movement.
The design made it difficult to lubricate the pin adequately – which may have caused excess friction.
The planned maintenance and inspection regime of the TLS was inadequate and unclear.
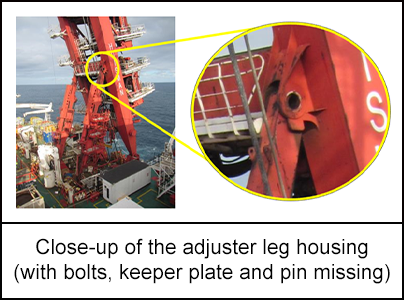
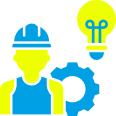
What did they learn?
Ensure the tower is kept in survival mode position during all transits (according to manufacturer’s recommendations).
Check the tightness of all critical bolts and pins throughout the tower.
Clearly define accurate inspection criteria for critical pins and securing mechanisms. Ensure planned maintenance requirements are updated.
Should something similar occur, consider:
- Performing a structural non-destructive testing (NDT) of pin connecting parts to verify sufficient load capacity and seaworthiness.
- Installing increased diameter anti-rotation locking key bolts to provide additional bolt shear strength if putting the adjuster leg back in place.
- Installing additional temporary bolt locking mechanisms on both adjuster leg pins locking key bolts to ensure vibration would not loosen the bolts before the permanent solution was ready.
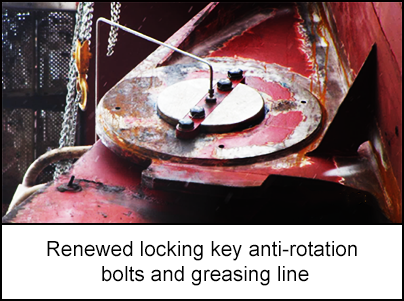
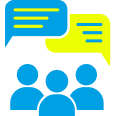
Ask yourself or your crew
Is your equipment kept in ‘survival mode’ in transit / when not in use? If not, why is that?
What is our inspection regime for tiltable lay systems / similar equipment?
How often do we check all critical bolts, pins and lubricated lines and how do we record this?
How do we inspect hard to access areas?
What measures do we have in place to prevent this from happening here? How can we improve?
During offshore operations, a 600kg (1322lbs) securing pin from a tiltable lay system (TLS) fell 16m (52ft) to the deck. No one was in was in the immediate area below the adjuster leg and no-one was injured.