-
What happened?
A worker came onboard a vessel to wash mud tanks with a high-pressure washer.
The tanks had been emptied earlier in the day, with the agitators running until the tanks were empty.
The agitators were stopped on the bridge integrated automation system (IAS), but were not isolated or locked out.
The worker was in a tank when the agitator suddenly started at 42 rotations per minute (rpm).
One of the paddles hit the worker in the lower back, knocking him over to the tank floor.
He was able to climb out of the tank but suffered bruises and a broken rib.
-
Why did it happen?
The agitator started by itself (potential technical issue under investigation).
However, the main cause of the incident was that the agitator was not isolated:
- Workers forgot to isolate the agitator, therefore an isolation certificate was never issued.
- There were no properly implemented routines for isolation.
The risk assessment contained a check of isolation but it wasn’t thoroughly reviewed.
Non-compliance and lack of communication - the third-party company had in their procedures to verify isolation, but this was not done as this was considered a vessel responsibility.
No independent sense of responsibility - engine department was not fully involved in tank washing operations, and only acted on bridge initiative.
-
What did they learn?
All those working with agitators should confirm that equipment is isolated before entering the tank.
Improve isolation routines so that all workers lockout/tagout equipment and issue isolation certificates.
Improve communication between bridge and engine departments, particularly relating to tank maintenance operations.
Improve compliance with existing procedures.
Review relevant risk assessments.
-
Ask yourself or your crew
Have you ever had an experience where equipment should have been isolated, but it wasn’t? What happened?
How do you confirm energy isolation on your equipment?
What risk assessments do you carry out before starting work? What more can you do to minimise risk?
How can we improve communications between workers in different departments? How about contractors?
Add to homescreen
Content name
Select existing category:
Content name
New collection
Edit collection
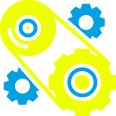
What happened?
A worker came onboard a vessel to wash mud tanks with a high-pressure washer.
The tanks had been emptied earlier in the day, with the agitators running until the tanks were empty.
The agitators were stopped on the bridge integrated automation system (IAS), but were not isolated or locked out.
The worker was in a tank when the agitator suddenly started at 42 rotations per minute (rpm).
One of the paddles hit the worker in the lower back, knocking him over to the tank floor.
He was able to climb out of the tank but suffered bruises and a broken rib.
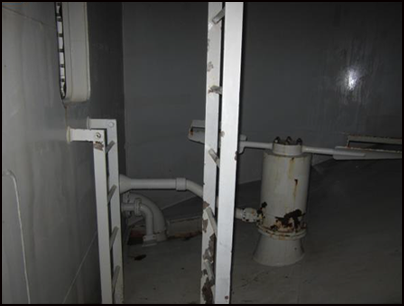
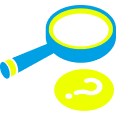
Why did it happen?
The agitator started by itself (potential technical issue under investigation).
However, the main cause of the incident was that the agitator was not isolated:
- Workers forgot to isolate the agitator, therefore an isolation certificate was never issued.
- There were no properly implemented routines for isolation.
The risk assessment contained a check of isolation but it wasn’t thoroughly reviewed.
Non-compliance and lack of communication - the third-party company had in their procedures to verify isolation, but this was not done as this was considered a vessel responsibility.
No independent sense of responsibility - engine department was not fully involved in tank washing operations, and only acted on bridge initiative.
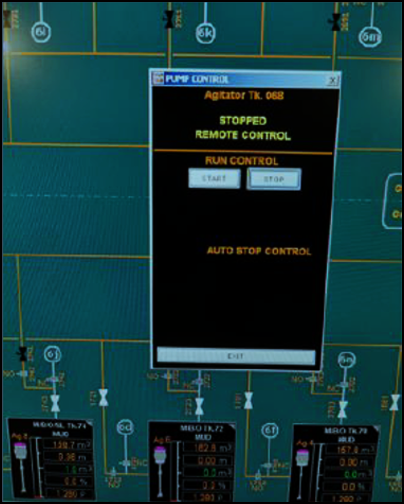
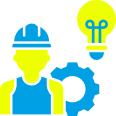
What did they learn?
All those working with agitators should confirm that equipment is isolated before entering the tank.
Improve isolation routines so that all workers lockout/tagout equipment and issue isolation certificates.
Improve communication between bridge and engine departments, particularly relating to tank maintenance operations.
Improve compliance with existing procedures.
Review relevant risk assessments.
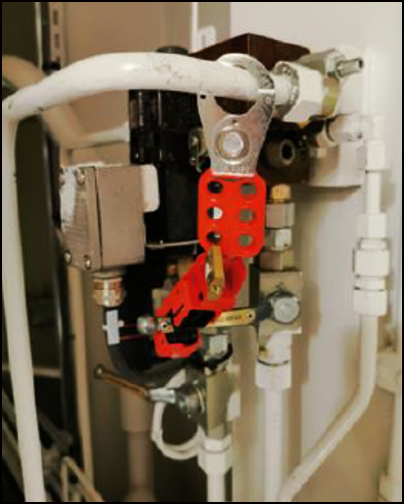
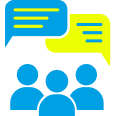
Ask yourself or your crew
Have you ever had an experience where equipment should have been isolated, but it wasn’t? What happened?
How do you confirm energy isolation on your equipment?
What risk assessments do you carry out before starting work? What more can you do to minimise risk?
How can we improve communications between workers in different departments? How about contractors?
An agitator in a mud tank started moving unexpectedly while a worker was in the tank. The worker was hit by the agitator paddle and fell to the tank floor.