-
What happened?
Following a maintenance overhaul, a fire occurred on a reciprocating compressor at an upstream processing plant.
A lubrication oil line compressor leaked, spraying the engine exhaust, which was hot enough to ignite the lube oil.
Fire detectors activated and initiated an emergency blowdown.
All personnel were safely evacuated.
-
Why did it happen?
Gaskets installed as part of the original facility design failed.
The gaskets were incompatible with the lubricant used due to insufficient material specification in design documentation.
‘Weak signals’, such as previous leaks from lube oil lines, were not identified or not acted upon (the risk was ‘normalised’).
Actions from previous incidents were not fully implemented.
-
What did they learn?
Report, record and repair small leaks and other weak signals. Don’t ‘normalise the risk’ – small leaks are not normal.
Minimise fire risks – and ensure process safety barriers are effective.
Reduce the risk of oil fires by improving shielding of hot surfaces.
Conduct routine operations and maintenance tasks with effective supervision.
Gaps in the site fire detection could lead to delays in fire detection and response.
Learn from previous incidents – don’t dismiss incidents just because they happened elsewhere.
-
Ask yourself or your crew
What other actions could have been taken to prevent this incident?
How can this happen here?
When we see small leaks and spill, do we ignore these? Share your experience.
What other risks are we normalising? What bigger problems can these be signs of?
How can we make sure we learn from past incidents?
Add to homescreen
Content name
Select existing category:
Content name
New collection
Edit collection
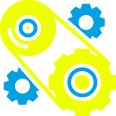
What happened?
Following a maintenance overhaul, a fire occurred on a reciprocating compressor at an upstream processing plant.
A lubrication oil line compressor leaked, spraying the engine exhaust, which was hot enough to ignite the lube oil.
Fire detectors activated and initiated an emergency blowdown.
All personnel were safely evacuated.
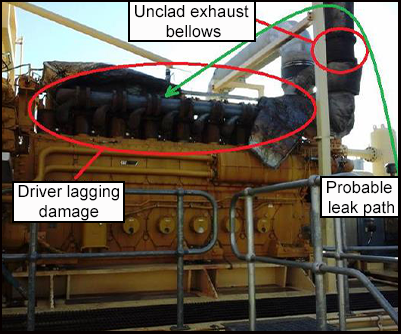
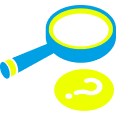
Why did it happen?
Gaskets installed as part of the original facility design failed.
The gaskets were incompatible with the lubricant used due to insufficient material specification in design documentation.
‘Weak signals’, such as previous leaks from lube oil lines, were not identified or not acted upon (the risk was ‘normalised’).
Actions from previous incidents were not fully implemented.
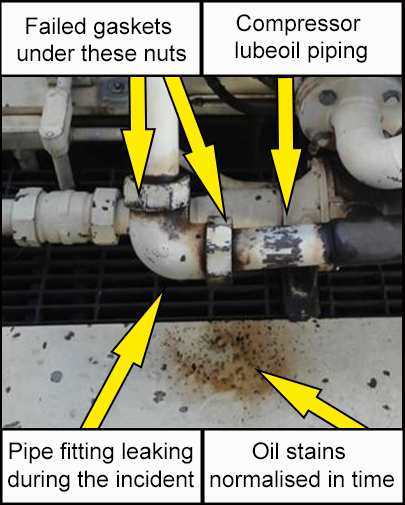
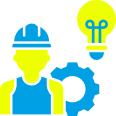
What did they learn?
Report, record and repair small leaks and other weak signals. Don’t ‘normalise the risk’ – small leaks are not normal.
Minimise fire risks – and ensure process safety barriers are effective.
Reduce the risk of oil fires by improving shielding of hot surfaces.
Conduct routine operations and maintenance tasks with effective supervision.
Gaps in the site fire detection could lead to delays in fire detection and response.
Learn from previous incidents – don’t dismiss incidents just because they happened elsewhere.
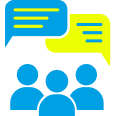
Ask yourself or your crew
What other actions could have been taken to prevent this incident?
How can this happen here?
When we see small leaks and spill, do we ignore these? Share your experience.
What other risks are we normalising? What bigger problems can these be signs of?
How can we make sure we learn from past incidents?
Following a maintenance overhaul, a fire occurred on a reciprocating compressor at an upstream processing plant. Fire detectors activated and initiated an emergency blowdown. All personnel were safely evacuated.