-
何が起こったのですか?
メンテナンスの分解検査の後、上流処理プラントにおいて、レシプロコンプレッサーから火災が生じました。
潤滑油ラインのコンプレッサーに漏れが生じ、エンジン排ガスが噴射され、その温度が高かったために、潤滑油が発火しました。
火災探知機が作動し、非常時の圧抜きが始まりました。
作業員は全員無事に避難しました。
-
なぜ、そのようなことが起きたのでしょうか?
当初の設計が一部不良であったため、ガスケットを取り付けました。
そのガスケットは、設計書の材料に関する仕様が不十分であったため、当該潤滑剤に適していませんでした。
前回あった潤滑油ラインからの漏れ等、「弱い信号」 が認識されていなっかたか、もしくはそれに対応していませんでした (そのリスクが 「正常化」 されていた)。
前回インシデントへの対処が充分に行なわれていませんでした。
-
彼らは何を学びましたか?
軽度の漏れ等の弱信号の報告、記録、修理を行います。 「リスクの正常化」 を行なわないこと。漏れは、軽度であっても正常状態ではありません。
リスクを最小限に留め、プロセスの安全バリアが効果的であることを確認します。
熱い表面に覆いをする等、オイル火災のリスクを削減します。
効果的な監督の下で、定期的に操作やメンテナンス作業を行います。
作業現場での検知にズレがある場合、火災の探知や対応に遅れが出ることがあります。
過去のインシデントから教訓を学びます。他の作業場で起こったからといって、そのようなインシデントを無視しません。
-
自問自答するか、クルーに質問してください
このインシデントを防ぐために、他にどのような措置を取ることができたでしょうか?
この作業場で、なぜこのようなことが起こり得るのでしょうか?
軽度の漏れや流出を発見した場合、これを無視しますか?自分の経験をシェアします。
どのようなリスクを 正常化していますか?こういった症状が示唆する大問題は何ですか?
どうすれば過去のインシデントから教訓を学べますか?
ホーム画面に追加する
コンテンツ名
既存のカテゴリーを選択する:
コンテンツ名
新しいコレクション
コレクションを編集する
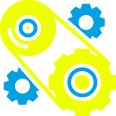
何が起こったのですか?
メンテナンスの分解検査の後、上流処理プラントにおいて、レシプロコンプレッサーから火災が生じました。
潤滑油ラインのコンプレッサーに漏れが生じ、エンジン排ガスが噴射され、その温度が高かったために、潤滑油が発火しました。
火災探知機が作動し、非常時の圧抜きが始まりました。
作業員は全員無事に避難しました。

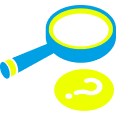
なぜ、そのようなことが起きたのでしょうか?
当初の設計が一部不良であったため、ガスケットを取り付けました。
そのガスケットは、設計書の材料に関する仕様が不十分であったため、当該潤滑剤に適していませんでした。
前回あった潤滑油ラインからの漏れ等、「弱い信号」 が認識されていなっかたか、もしくはそれに対応していませんでした (そのリスクが 「正常化」 されていた)。
前回インシデントへの対処が充分に行なわれていませんでした。
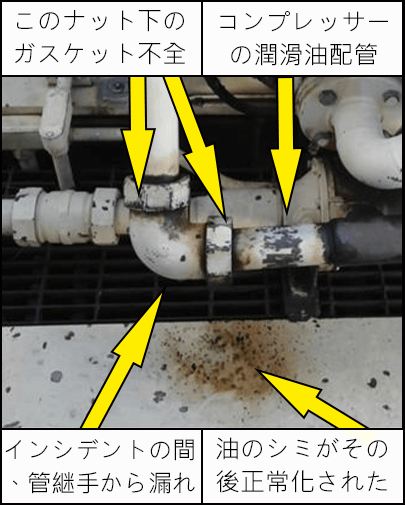
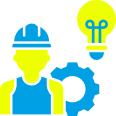
彼らは何を学びましたか?
軽度の漏れ等の弱信号の報告、記録、修理を行います。 「リスクの正常化」 を行なわないこと。漏れは、軽度であっても正常状態ではありません。
リスクを最小限に留め、プロセスの安全バリアが効果的であることを確認します。
熱い表面に覆いをする等、オイル火災のリスクを削減します。
効果的な監督の下で、定期的に操作やメンテナンス作業を行います。
作業現場での検知にズレがある場合、火災の探知や対応に遅れが出ることがあります。
過去のインシデントから教訓を学びます。他の作業場で起こったからといって、そのようなインシデントを無視しません。
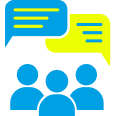
自問自答するか、クルーに質問してください
このインシデントを防ぐために、他にどのような措置を取ることができたでしょうか?
この作業場で、なぜこのようなことが起こり得るのでしょうか?
軽度の漏れや流出を発見した場合、これを無視しますか?自分の経験をシェアします。
どのようなリスクを 正常化していますか?こういった症状が示唆する大問題は何ですか?
どうすれば過去のインシデントから教訓を学べますか?
メンテナンスの分解検査の後、上流処理プラントにおいて、レシプロコンプレッサーから火災が生じました。火災探知機が作動し、非常時の圧抜きが始まりました。作業員は全員無事に避難しました。