-
What happened?
A night shift power plant operator was on normal rounds when he heard a hissing sound in the fuel gas filters area.
The noise was a gas leak coming from a gas pipe spool to the flare header.
The supervisor was notified of the gas leak in the pipe rack (which led to the gas turbines).
The line was isolated (by sending gas to flare) ready for repair in the morning.
The plant was secured. All vehicles and personnel were kept clear.
The next day, the pipe spool was isolated and replaced.
When the pipe spool was cut in half, solid residue was found inside.
The incident had high potential, but good practice prevented a significant event.
-
Why did it happen?
Gas leaked on low pressure gas flare piping. Leaking point was upstream of an emergency shutdown (ESD) valve.
When the pipe spool was removed, build-up residue was found inside.
The internal pipe was not protected against dissolved oxygen corrosion.
- Analysis showed the presence of oxygen dissolved in utility water was used as make-up water in the liquid ring vapor recovery unit (VRU) compressors.
There was no fire and gas detection coverage in the area.
-
What did they learn?
Ensure pipes and ESD valves are maintained periodically, preferably monthly. Check if other types of ESD valves might be better suited and consider replacing them.
Evaluate options for removing oxygen from utility water.
If corrosion residue is found:
- Test it using X-ray diffraction (XRD), X-ray fluorescence (XRF) and carbon-hydrogen-nitrogen (CHN) to confirm and address the degradation of the pipe.
- Inspect all similar piping in the plant and identify areas where similar corrosion is found. Replace the piping or include in regular non-destructive testing programmes.
Assess if fire and gas detection coverage might need to be extended to other areas on your site.
-
Ask yourself or your crew
The operator was the last line of defence in this incident – who/what is the last line of defence in your role?
How often is your equipment inspected? Should the tests be more regular?
How do you identify the types of corrosion and how damaging they could be?
What can you or your team do to identify any risks where you work?
Add to homescreen
Content name
Select existing category:
Content name
New collection
Edit collection
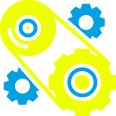
What happened?
A night shift power plant operator was on normal rounds when he heard a hissing sound in the fuel gas filters area.
The noise was a gas leak coming from a gas pipe spool to the flare header.
The supervisor was notified of the gas leak in the pipe rack (which led to the gas turbines).
The line was isolated (by sending gas to flare) ready for repair in the morning.
The plant was secured. All vehicles and personnel were kept clear.
The next day, the pipe spool was isolated and replaced.
When the pipe spool was cut in half, solid residue was found inside.
The incident had high potential, but good practice prevented a significant event.
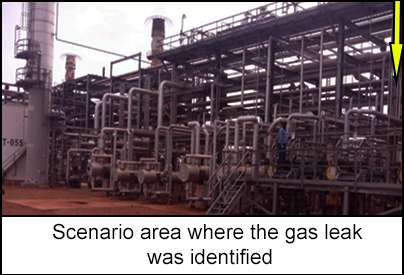
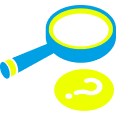
Why did it happen?
Gas leaked on low pressure gas flare piping. Leaking point was upstream of an emergency shutdown (ESD) valve.
When the pipe spool was removed, build-up residue was found inside.
The internal pipe was not protected against dissolved oxygen corrosion.
- Analysis showed the presence of oxygen dissolved in utility water was used as make-up water in the liquid ring vapor recovery unit (VRU) compressors.
There was no fire and gas detection coverage in the area.
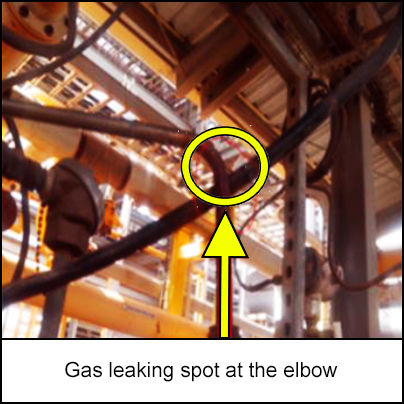
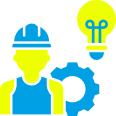
What did they learn?
Ensure pipes and ESD valves are maintained periodically, preferably monthly. Check if other types of ESD valves might be better suited and consider replacing them.
Evaluate options for removing oxygen from utility water.
If corrosion residue is found:
- Test it using X-ray diffraction (XRD), X-ray fluorescence (XRF) and carbon-hydrogen-nitrogen (CHN) to confirm and address the degradation of the pipe.
- Inspect all similar piping in the plant and identify areas where similar corrosion is found. Replace the piping or include in regular non-destructive testing programmes.
Assess if fire and gas detection coverage might need to be extended to other areas on your site.
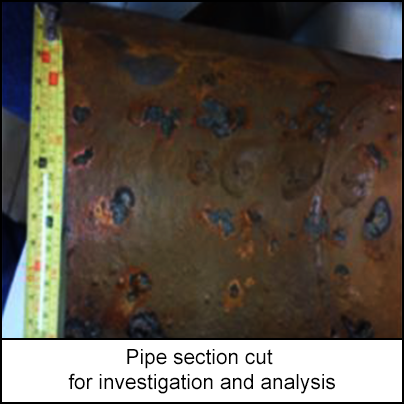
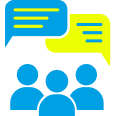
Ask yourself or your crew
The operator was the last line of defence in this incident – who/what is the last line of defence in your role?
How often is your equipment inspected? Should the tests be more regular?
How do you identify the types of corrosion and how damaging they could be?
What can you or your team do to identify any risks where you work?
A plant operator was on normal rounds when they discovered a gas leak. The leak was isolated and repaired the next day. The incident had high potential, but good practice prevented a significant event.