-
What happened?
Workers were preparing for a welding operation using a plug on a gasoline line in a pipe way.
After connecting to what was believed to be the nitrogen line, the nitrogen flow through the Duchêne blind flange was checked.
They detected a strong smell at the blind flange outlet and at the safety valve on the skid.
The injection was stopped and the skid was isolated.
Presence of explosive and toxic gas mixture was identified using a portable gas detector.
The line was followed and identified. The skid controlling the nitrogen levels for the welding operation had been connected to the fuel gas network instead of the nitrogen circuit.
-
Why did it happen?
Inappropriate design: nitrogen and fuel gas line had the same size and colour.
No identification on the lines was available nearby the works area.
No utility points were available nearby, so the connection to the nitrogen line by vent or purge was authorised.
The nitrogen connection point was not identified in the handover documentation.
Lack of experience and/or insufficient strictness. On location, no verification of the connection point was performed.
What worked well: following the welding with a plug procedure and controls prevented a dangerous situation before the hot work started.
-
What did they learn?
Connect only to a specific nitrogen utility connection point. If one is not available, a rack of nitrogen should be used.
The procedure for the isolation of equipment should specify the utility connection points to use.
Always verify the connection points on site. Follow the line! Include this in the task list for outside operators when preparing for (hot) work.
Procedure for handover operations should include checks to avoid connection errors.
The accurate execution of the checking procedure prevented a potentially serious accident.
-
Ask yourself or your crew
How can something like this happen here?
How do you know which connection points you can use?
How do we know we have connected to the right line?
Think of today’s welding task. What can go wrong and how can you prevent it?
What else can we learn from this incident?
Add to homescreen
Content name
Select existing category:
Content name
New collection
Edit collection
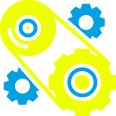
What happened?
Workers were preparing for a welding operation using a plug on a gasoline line in a pipe way.
After connecting to what was believed to be the nitrogen line, the nitrogen flow through the Duchêne blind flange was checked.
They detected a strong smell at the blind flange outlet and at the safety valve on the skid.
The injection was stopped and the skid was isolated.
Presence of explosive and toxic gas mixture was identified using a portable gas detector.
The line was followed and identified. The skid controlling the nitrogen levels for the welding operation had been connected to the fuel gas network instead of the nitrogen circuit.
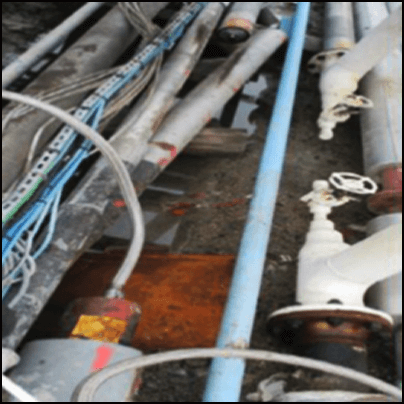
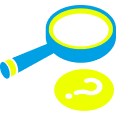
Why did it happen?
Inappropriate design: nitrogen and fuel gas line had the same size and colour.
No identification on the lines was available nearby the works area.
No utility points were available nearby, so the connection to the nitrogen line by vent or purge was authorised.
The nitrogen connection point was not identified in the handover documentation.
Lack of experience and/or insufficient strictness. On location, no verification of the connection point was performed.
What worked well: following the welding with a plug procedure and controls prevented a dangerous situation before the hot work started.
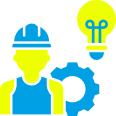
What did they learn?
Connect only to a specific nitrogen utility connection point. If one is not available, a rack of nitrogen should be used.
The procedure for the isolation of equipment should specify the utility connection points to use.
Always verify the connection points on site. Follow the line! Include this in the task list for outside operators when preparing for (hot) work.
Procedure for handover operations should include checks to avoid connection errors.
The accurate execution of the checking procedure prevented a potentially serious accident.

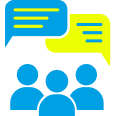
Ask yourself or your crew
How can something like this happen here?
How do you know which connection points you can use?
How do we know we have connected to the right line?
Think of today’s welding task. What can go wrong and how can you prevent it?
What else can we learn from this incident?
During preparations for a welding operations, a mixture of explosive and toxic gas was identified using a portable gas detector. The skid controlling the nitrogen levels for the welding operation had been connected to the fuel gas network instead of the nitrogen circuit.