-
What happened?
A technician inspected a boiler feedwater pump motor. There were no signs of noise, vibration, oil leak, or other problems.
A few hours later there was a problem with a low minimum flow alarm.
The 30 lb (13.6 kg) end of the motor shaft and coupling hub was then ejected and travelled 14 feet (4.2 m), hitting nearby piping.
No one was hurt but the force could have caused disability or a fatality.
-
Why did it happen?
The pipe nipple from the constant level oiler to the bearing housing was thinner than allowed (¼ inches schedule 40 SS).
After years of service, the pipe nipple suffered a sudden fatigue failure due to high stress and stress riser.
The failure allowed the oil to drain from the bearing, which started events that led to the failure of the motor.
-
What did they learn?
Perform an inspection before restarting motors.
Constant levels oilers should be mounted directly to the side of bearing housing.
Proactively upgrade the oil piping on existing motors.
Identify motors with similar design and evaluate need for upgrade – either proactively or at next scheduled overhaul.
-
Ask yourself or your crew
How can something like this happen here?
Do our motors follow a similar design?
How do we know our motors do not have the same issue?
What actions can we take?
Add to homescreen
Content name
Select existing category:
Content name
New collection
Edit collection
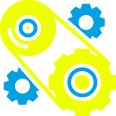
What happened?
A technician inspected a boiler feedwater pump motor. There were no signs of noise, vibration, oil leak, or other problems.
A few hours later there was a problem with a low minimum flow alarm.
The 30 lb (13.6 kg) end of the motor shaft and coupling hub was then ejected and travelled 14 feet (4.2 m), hitting nearby piping.
No one was hurt but the force could have caused disability or a fatality.
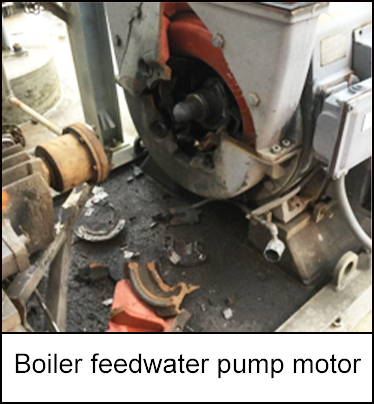
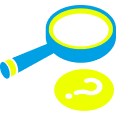
Why did it happen?
The pipe nipple from the constant level oiler to the bearing housing was thinner than allowed (¼ inches schedule 40 SS).
After years of service, the pipe nipple suffered a sudden fatigue failure due to high stress and stress riser.
The failure allowed the oil to drain from the bearing, which started events that led to the failure of the motor.
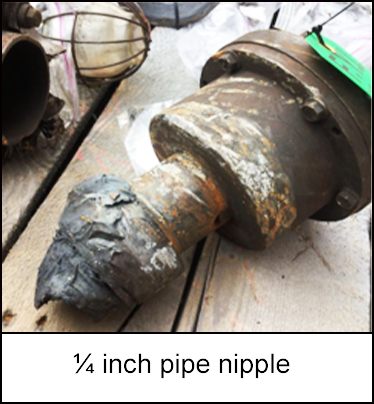
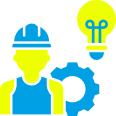
What did they learn?
Perform an inspection before restarting motors.
Constant levels oilers should be mounted directly to the side of bearing housing.
Proactively upgrade the oil piping on existing motors.
Identify motors with similar design and evaluate need for upgrade – either proactively or at next scheduled overhaul.
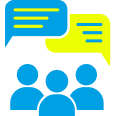
Ask yourself or your crew
How can something like this happen here?
Do our motors follow a similar design?
How do we know our motors do not have the same issue?
What actions can we take?
A few hours after an inspection, a boiler feedwater pump motor failed. The end of the motor shaft and coupling hub was ejected and travelled 14 feet (4.2 m), hitting nearby piping. No one was hurt but the force could have caused disability or a fatality.