-
What happened?
A work crew were working on fabricating an I-beam.
They used a gantry crane to support the web of the I-beam while the flange was being welded to the web.
They found a gap in the fit-up after completing a few inches of tack welding. The crew removed the beam clamps to address the gap.
The tack welds failed, allowing the beam to topple over.
The beam struck two workers, killing one and injuring another.
-
Why did it happen?
The pre-job planning was not specific enough for this particular fabrication activity.
The crew were not familiar with this type of I-beam fabrication. They assumed the tack welds would hold the beam upright, but they were not strong enough.
The crew deviated from normal practice by removing the beam clamps. However, as they were subcontractors, they were unfamiliar with this as it was not documented in a procedure or code of practice.
-
What did they learn?
Use a written work method/procedure so everyone understands the scope and safety controls associated with their work.
Make sure that training covers ‘line of fire’ awareness. Do not over-rely on tack welds.
Make sure a secondary safety measure is in place to limit the danger when working with structures that could fall or topple.
Ensure that pre-job planning considers the specific hazards of the activity being carried out.
If the situation changes during the job, then reassess any hazards and make sure safety controls are in place before work starts again.
-
Ask yourself or your crew
What would you do differently in this situation?
Think of an example activity where we may (over)rely on tack welds? What can we do differently?
When planning a job, how do we ensure we identify the specific hazards of the activity?
How can we make sure that everyone (including subcontractors and contractors) are aware of our work practices?
If things do not go to plan, or new hazards emerge, what should you do?
Add to homescreen
Content name
Select existing category:
Content name
New collection
Edit collection
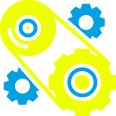
What happened?
A work crew were working on fabricating an I-beam.
They used a gantry crane to support the web of the I-beam while the flange was being welded to the web.
They found a gap in the fit-up after completing a few inches of tack welding. The crew removed the beam clamps to address the gap.
The tack welds failed, allowing the beam to topple over.
The beam struck two workers, killing one and injuring another.

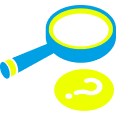
Why did it happen?
The pre-job planning was not specific enough for this particular fabrication activity.
The crew were not familiar with this type of I-beam fabrication. They assumed the tack welds would hold the beam upright, but they were not strong enough.
The crew deviated from normal practice by removing the beam clamps. However, as they were subcontractors, they were unfamiliar with this as it was not documented in a procedure or code of practice.
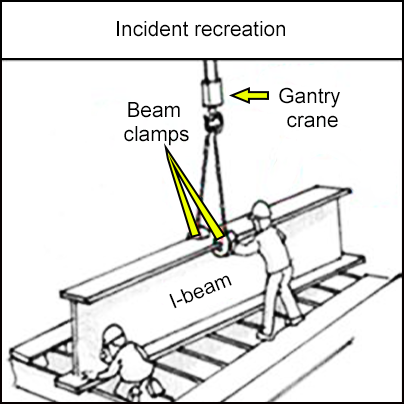
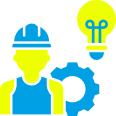
What did they learn?
Use a written work method/procedure so everyone understands the scope and safety controls associated with their work.
Make sure that training covers ‘line of fire’ awareness. Do not over-rely on tack welds.
Make sure a secondary safety measure is in place to limit the danger when working with structures that could fall or topple.
Ensure that pre-job planning considers the specific hazards of the activity being carried out.
If the situation changes during the job, then reassess any hazards and make sure safety controls are in place before work starts again.
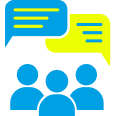
Ask yourself or your crew
What would you do differently in this situation?
Think of an example activity where we may (over)rely on tack welds? What can we do differently?
When planning a job, how do we ensure we identify the specific hazards of the activity?
How can we make sure that everyone (including subcontractors and contractors) are aware of our work practices?
If things do not go to plan, or new hazards emerge, what should you do?
A partially fabricated I-beam (1.5 tons) toppled over and struck two workers. One of the workers was fatally injured, and another received a leg fracture.