-
What happened?
During maintenance of a coke drum actuator, hydrogen sulfide gases vented from a coke drum top head.
Workers’ hydrogen sulfide detectors alarmed at 69 ppm (parts per million).
Four hours earlier, the coke drum was filled with a mixture of steam and fractionator gas when the coke drum feed valve was opened.
Energy isolation had not been maintained when setting the actuator limits, resulting in the fractionator being lined up directly to the open coke drum.
-
Why did it happen?
The coke drum inlet valve interlock was unintentionally defeated without authorisation when a new actuator was installed without safety locks.
Valve lineup to gassed up tower during coker shutdown was not well understood. Shutdown procedures left a single block between fractionator and open coke drum.
Miscommunication between operations and maintenance about the work scope led to the coke drum inlet valve being opened.
The work package was not reviewed by operations.
The work authorisation permit was not updated to allow opening of the valve.
The unit had been shut down for several weeks, so operators became complacent about working on it.
-
What did they learn?
Update shut down procedures to ensure coke drum inlet line is double blocked or blinded when coke drums are left open to atmosphere.
Include a display of coke drum valve positions.
Update coke drum interlock bypass and safety bypass procedures to ensure interlock system cannot be unintentionally defeated.
Revise maintenance interlock actuator procedure to include hold points to ensure safety locks are transferred to new actuator prior to installation and prior to opening or closing the valve. Include detailed steps on how to set limits.
-
Ask yourself or your crew
What is our current shut-down procedure when coke drums are left open to atmosphere? Do we use double block/blind or single block?
When actuators are being replaced, how do you ensure that the safety locks are transferred to the new actuator before installing and accessing the valves?
How can coke drum interlocks be unintentionally defeated?
What would you say are two key prevention safeguards that must be in place before you start a similar task? What about the two key recovery and response safeguards in case an event were to occur?
What can we do to prevent this type of incident happening here?
Add to homescreen
Content name
Select existing category:
Content name
New collection
Edit collection
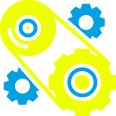
What happened?
During maintenance of a coke drum actuator, hydrogen sulfide gases vented from a coke drum top head.
Workers’ hydrogen sulfide detectors alarmed at 69 ppm (parts per million).
Four hours earlier, the coke drum was filled with a mixture of steam and fractionator gas when the coke drum feed valve was opened.
Energy isolation had not been maintained when setting the actuator limits, resulting in the fractionator being lined up directly to the open coke drum.
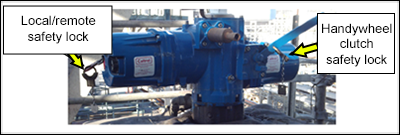
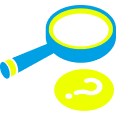
Why did it happen?
The coke drum inlet valve interlock was unintentionally defeated without authorisation when a new actuator was installed without safety locks.
Valve lineup to gassed up tower during coker shutdown was not well understood. Shutdown procedures left a single block between fractionator and open coke drum.
Miscommunication between operations and maintenance about the work scope led to the coke drum inlet valve being opened.
The work package was not reviewed by operations.
The work authorisation permit was not updated to allow opening of the valve.
The unit had been shut down for several weeks, so operators became complacent about working on it.
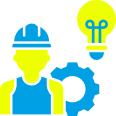
What did they learn?
Update shut down procedures to ensure coke drum inlet line is double blocked or blinded when coke drums are left open to atmosphere.
Include a display of coke drum valve positions.
Update coke drum interlock bypass and safety bypass procedures to ensure interlock system cannot be unintentionally defeated.
Revise maintenance interlock actuator procedure to include hold points to ensure safety locks are transferred to new actuator prior to installation and prior to opening or closing the valve. Include detailed steps on how to set limits.
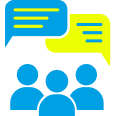
Ask yourself or your crew
What is our current shut-down procedure when coke drums are left open to atmosphere? Do we use double block/blind or single block?
When actuators are being replaced, how do you ensure that the safety locks are transferred to the new actuator before installing and accessing the valves?
How can coke drum interlocks be unintentionally defeated?
What would you say are two key prevention safeguards that must be in place before you start a similar task? What about the two key recovery and response safeguards in case an event were to occur?
What can we do to prevent this type of incident happening here?
2 workers’ hydrogen sulfide detectors alarmed during maintenance of a coke drum actuator. The coke drum inlet valve interlock was unintentionally defeated without authorisation when a new actuator was installed without safety locks.