-
What happened?
A field operator noticed a sound from the orifice carrier on a compressor and reported it for review.
Maintenance replaced the O-rings in both the top body area and on the orifice plate.
The compressor was tested after the O-rings were fitted. The orifice compressor held, but a dry gas seal failure occurred after 3 hours.
After a further few weeks of repairs, the compressor was put back online and ran for several hours.
A gas release occurred from orifice carrier orifice plate area. Gas detectors did not pick up the gas release.
Operator heard the leak and reported it to control room.
The compressor was shut down and the O-ring on the orifice plate was replaced again. Top body O-ring was not replaced.
Several hours later, the field operator observed a leak from the top body area of the compressor. Once again, the gas detectors did not pick up the release.
-
Why did it happen?
Insufficient pre-job planning: O-rings used in the original repair were not the ones recommended by the original equipment manufacturer (OEM).
Following testing and failure, only the O-rings on the orifice plate and cover plate were replaced, but not on the top body.
Gas releases were not detected by the gas detectors.
- Gas detectors were not located in the correct place for best coverage
Inspection and testing for orifice carriers was not scheduled as part of a preventative maintenance programme, nor formally documented.
-
What did they learn?
Only use OEM or equivalent parts and materials for installation and repairs.
Confirm that orifice carrier inspection is regularly scheduled and is in line with manufacturer guidance.
Verify that all gas detection systems provide adequate coverage for process areas.
-
Ask yourself or your crew
Where should the gas detections systems have been installed to pick up the gas releases?
What should you do if you if the appropriate OEM parts/materials or their equivalent are not available?
How do you know what is an adequate replacement in line with the OEM specifications?
What is the maintenance schedule for the equipment that you work on? When was it last tested?
What measures do we have in place to prevent this from happening here?
Add to homescreen
Content name
Select existing category:
Content name
New collection
Edit collection
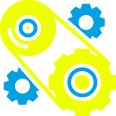
What happened?
A field operator noticed a sound from the orifice carrier on a compressor and reported it for review.
Maintenance replaced the O-rings in both the top body area and on the orifice plate.
The compressor was tested after the O-rings were fitted. The orifice compressor held, but a dry gas seal failure occurred after 3 hours.
After a further few weeks of repairs, the compressor was put back online and ran for several hours.
A gas release occurred from orifice carrier orifice plate area. Gas detectors did not pick up the gas release.
Operator heard the leak and reported it to control room.
The compressor was shut down and the O-ring on the orifice plate was replaced again. Top body O-ring was not replaced.
Several hours later, the field operator observed a leak from the top body area of the compressor. Once again, the gas detectors did not pick up the release.
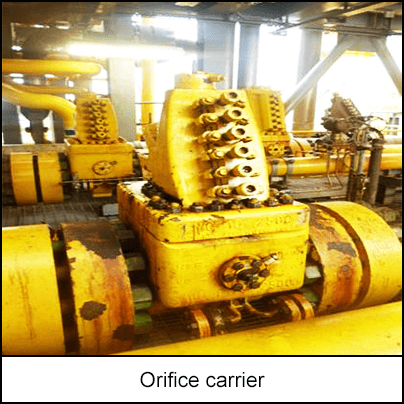
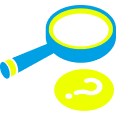
Why did it happen?
Insufficient pre-job planning: O-rings used in the original repair were not the ones recommended by the original equipment manufacturer (OEM).
Following testing and failure, only the O-rings on the orifice plate and cover plate were replaced, but not on the top body.
Gas releases were not detected by the gas detectors.
- Gas detectors were not located in the correct place for best coverage
Inspection and testing for orifice carriers was not scheduled as part of a preventative maintenance programme, nor formally documented.
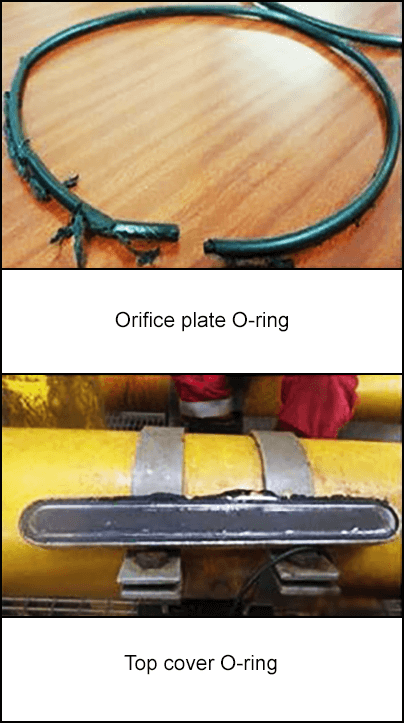
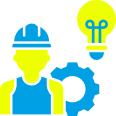
What did they learn?
Only use OEM or equivalent parts and materials for installation and repairs.
Confirm that orifice carrier inspection is regularly scheduled and is in line with manufacturer guidance.
Verify that all gas detection systems provide adequate coverage for process areas.
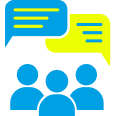
Ask yourself or your crew
Where should the gas detections systems have been installed to pick up the gas releases?
What should you do if you if the appropriate OEM parts/materials or their equivalent are not available?
How do you know what is an adequate replacement in line with the OEM specifications?
What is the maintenance schedule for the equipment that you work on? When was it last tested?
What measures do we have in place to prevent this from happening here?
A field operator noticed a sound from the orifice carrier on a compressor and reported it for review. Following maintenance, the equipment failed twice, allowing for gas to be released.