-
What happened?
A load of polished metal elements was being lifted using a permanent lifting magnet.
The task has been completed previously (around 100 times) without incidents.
The load needed to be lifted up a few centimetres to put supports underneath it.
To avoid damage to metal pieces when lifted, a protective layer had to be placed between the magnet and the metal.
A worker, advised by his colleagues, used paper packing (thickness 0.1mm) as protective layer for the first few loads. For unknown reasons he then switched to foil packing material (1.5-2mm thick).
As the load was lifted, the worker reached over to remove some of the packing material, when the load dropped onto his hand.
-
Why did it happen?
The worker positioned himself in the line of fire.
The holding capacity of a magnet requires an uninterrupted magnetic field. The ‘air gap’ created by using a thicker packing material lessened the holding capacity of the magnet.
The importance of the thickness of the packing material and air gap were not understood by the workers or addressed in the job safety analysis (JSA) and toolbox talks.
The work instructions were not specific enough on how to operate the magnet, the reason for the protective layer, or the thickness or type of material to be used as packing material (merely that it should be 'cloth'). The use of paper was a 'common practice' not documented.
No one challenged this ‘common practice’ or the work instructions.
-
What did they learn?
Circulate all available information (operator’s manuals, lifting plans, work instructions, risk assessments) so that workers are fully aware of it before starting work.
Personnel should fully understand the limitations and precautions to be taken when using lifting magnets – e.g. minimum load thickness and the effect of an air gap.
Consider documenting or share all knowledge on undocumented common practices that might be known to experienced workers, but not to others.
-
Ask yourself or your crew
What are the hazards and limitations of using lifting magnets?
Think of a time when you carried out an undocumented ‘common practice’ during a lifting job. What could have gone wrong?
How would you challenge practices that seem unsafe? How about undocumented ‘common practices’?
What should you do if:
- you observe hazards that have not been covered by the job safety analysis and toolbox talk?
- your process documentation is incomplete/unclear?
What safety measures do we have in place to prevent this from happening here? How can we improve?
Add to homescreen
Content name
Select existing category:
Content name
New collection
Edit collection
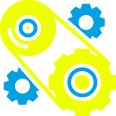
What happened?
A load of polished metal elements was being lifted using a permanent lifting magnet.
The task has been completed previously (around 100 times) without incidents.
The load needed to be lifted up a few centimetres to put supports underneath it.
To avoid damage to metal pieces when lifted, a protective layer had to be placed between the magnet and the metal.
A worker, advised by his colleagues, used paper packing (thickness 0.1mm) as protective layer for the first few loads. For unknown reasons he then switched to foil packing material (1.5-2mm thick).
As the load was lifted, the worker reached over to remove some of the packing material, when the load dropped onto his hand.
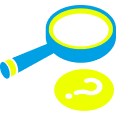
Why did it happen?
The worker positioned himself in the line of fire.
The holding capacity of a magnet requires an uninterrupted magnetic field. The ‘air gap’ created by using a thicker packing material lessened the holding capacity of the magnet.
The importance of the thickness of the packing material and air gap were not understood by the workers or addressed in the job safety analysis (JSA) and toolbox talks.
The work instructions were not specific enough on how to operate the magnet, the reason for the protective layer, or the thickness or type of material to be used as packing material (merely that it should be 'cloth'). The use of paper was a 'common practice' not documented.
No one challenged this ‘common practice’ or the work instructions.
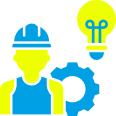
What did they learn?
Circulate all available information (operator’s manuals, lifting plans, work instructions, risk assessments) so that workers are fully aware of it before starting work.
Personnel should fully understand the limitations and precautions to be taken when using lifting magnets – e.g. minimum load thickness and the effect of an air gap.
Consider documenting or share all knowledge on undocumented common practices that might be known to experienced workers, but not to others.
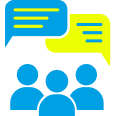
Ask yourself or your crew
What are the hazards and limitations of using lifting magnets?
Think of a time when you carried out an undocumented ‘common practice’ during a lifting job. What could have gone wrong?
How would you challenge practices that seem unsafe? How about undocumented ‘common practices’?
What should you do if:
- you observe hazards that have not been covered by the job safety analysis and toolbox talk?
- your process documentation is incomplete/unclear?
What safety measures do we have in place to prevent this from happening here? How can we improve?
Polished metal elements were being lifted using a permanent lifting magnet. A worker used foil packing material as a protective layer (1.5-2mm thick) between the magnet and the metal. As the load was lifted, it dropped down onto the worker’s hand, injuring him.