-
What happened?
Workers were replacing an electrical submersible pump (ESP) at a well.
After completing the rig up, spudding the well and reading the casing and tubing pressures (0 bar) the well was opened, and circulation commenced by pumping water down the tubing taking returns from the annulus.
A worker was posted to the drain tank to listen for gas entering the tank.
Gas vented up the drain line (a flexible hose pushed through a grill on the drain) and into the tank. Before the worker realised that gas was present, it started to diffuse out of the tank.
The mix of gas and air was drawn into the circulation pump caused the motor to ‘race’.
Unsuccessful attempts were made to shut off the circulation pump and the tree valve.
The gas cloud ignited. The blast set fire to the bleed-off tank, rig and pump.
Three workers died from burn injuries and one worker broke their legs trying to escape.
-
Why did it happen?
The wind blew the gas from the drain tank towards the circulation pump.
Uncontrolled bleeding off (no use of choke manifold, bleed off not vented through a separator with flare off).
Insufficient distance between drain tank, rig and circulation pump.
Insufficient gas detection methods.
Contractor violated their own instructions for equipment layout, set up and operations.
Unsafe work practices due to normalisation
General poor implementation of process (bridging document, safety rules), lack of procedural supervision, unsafe working practices, lack of risk management for country-specific challenges and weak safety culture.
Failure to learn from previous similar incidents.
-
What did they learn?
Ensure an effective process for overseeing safety critical activities.
Update the well engineering technical standard to include additional information for well in workover/water injection (WO/WI) minimum requirements.
Develop site-specific work instructions for preparation and execution of WO/WI operations.
Ensure competent workers and contractors are employed to fulfil their duties.
Establish a formal process for lessons learnt from incidents.
-
Ask yourself or your crew
Is all your equipment set up appropriately (correct distances apart, gas detection instruments etc.)?
What should you do if you did not feel the working practices are safe?
What impact can the weather have on your activities? How are external factors included in your risk assessments?
How can we improve supervision during your tasks?
What controls do we have in place for preventing this happening on our site? What else should we consider?
Add to homescreen
Content name
Select existing category:
Content name
New collection
Edit collection
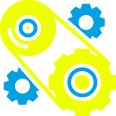
What happened?
Workers were replacing an electrical submersible pump (ESP) at a well.
After completing the rig up, spudding the well and reading the casing and tubing pressures (0 bar) the well was opened, and circulation commenced by pumping water down the tubing taking returns from the annulus.
A worker was posted to the drain tank to listen for gas entering the tank.
Gas vented up the drain line (a flexible hose pushed through a grill on the drain) and into the tank. Before the worker realised that gas was present, it started to diffuse out of the tank.
The mix of gas and air was drawn into the circulation pump caused the motor to ‘race’.
Unsuccessful attempts were made to shut off the circulation pump and the tree valve.
The gas cloud ignited. The blast set fire to the bleed-off tank, rig and pump.
Three workers died from burn injuries and one worker broke their legs trying to escape.
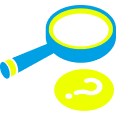
Why did it happen?
The wind blew the gas from the drain tank towards the circulation pump.
Uncontrolled bleeding off (no use of choke manifold, bleed off not vented through a separator with flare off).
Insufficient distance between drain tank, rig and circulation pump.
Insufficient gas detection methods.
Contractor violated their own instructions for equipment layout, set up and operations.
Unsafe work practices due to normalisation
General poor implementation of process (bridging document, safety rules), lack of procedural supervision, unsafe working practices, lack of risk management for country-specific challenges and weak safety culture.
Failure to learn from previous similar incidents.
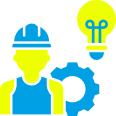
What did they learn?
Ensure an effective process for overseeing safety critical activities.
Update the well engineering technical standard to include additional information for well in workover/water injection (WO/WI) minimum requirements.
Develop site-specific work instructions for preparation and execution of WO/WI operations.
Ensure competent workers and contractors are employed to fulfil their duties.
Establish a formal process for lessons learnt from incidents.
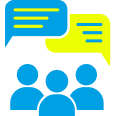
Ask yourself or your crew
Is all your equipment set up appropriately (correct distances apart, gas detection instruments etc.)?
What should you do if you did not feel the working practices are safe?
What impact can the weather have on your activities? How are external factors included in your risk assessments?
How can we improve supervision during your tasks?
What controls do we have in place for preventing this happening on our site? What else should we consider?
Workers were replacing an electrical submersible pump (ESP) at a well. Gas vented into the tank and diffused out, igniting and setting fire to the bleed-off tank, rig and pump. Three workers died from burn injuries and one worker broke their legs trying to escape.