-
What happened?
A multi-stage pump was replaced with a single stage design.
New pump was run for 10 minutes only due to high vibration and cavitation (creation and immediate collapse of small bubbles) on start-up.
Vibration readings were taken and considered OK, so the pump was run for a further 20 minutes and appeared normal.
3 hours later a fire broke out on the pump.
The incident had potential for injury and production interruption.
-
Why did it happen?
Fire started on a ¾in (2cm) block valve on the suction side of the pump.
Valve was not rebuilt correctly when it was replaced.
- Bonnet gasket was not installed.
- Cap screws were used as valve bonnet fasteners – rather than the manufacturer’s studs and nuts.
- Reducing tee had a crack due to a weld defect (caused by lack of fusion).
-
What did they learn?
Review and improve checklists to increase valve rebuild quality.
Include bolt torqueing requirements and gasket verification steps as part of the rebuild process.
-
Ask yourself or your crew
Were there any warning signs indicating the pump should have been checked earlier?
What other actions would you have taken in this situation?
When equipment is updated, how do you know it is ‘better’? How can you check this?
What checklists do you have in place for rebuilding/repairing pumps? Have we missed any steps?
Add to homescreen
Content name
Select existing category:
Content name
New collection
Edit collection
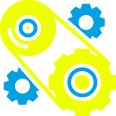
What happened?
A multi-stage pump was replaced with a single stage design.
New pump was run for 10 minutes only due to high vibration and cavitation (creation and immediate collapse of small bubbles) on start-up.
Vibration readings were taken and considered OK, so the pump was run for a further 20 minutes and appeared normal.
3 hours later a fire broke out on the pump.
The incident had potential for injury and production interruption.
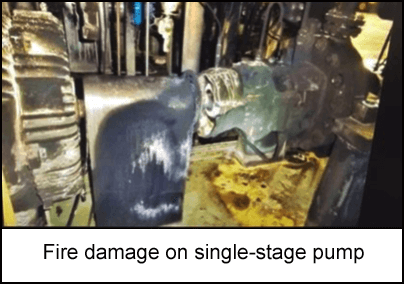
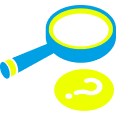
Why did it happen?
Fire started on a ¾in (2cm) block valve on the suction side of the pump.
Valve was not rebuilt correctly when it was replaced.
- Bonnet gasket was not installed.
- Cap screws were used as valve bonnet fasteners – rather than the manufacturer’s studs and nuts.
- Reducing tee had a crack due to a weld defect (caused by lack of fusion).
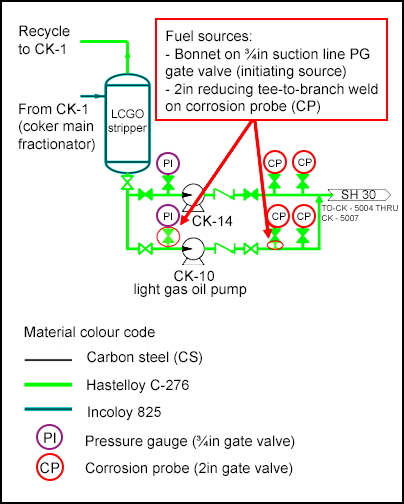
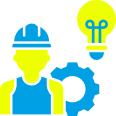
What did they learn?
Review and improve checklists to increase valve rebuild quality.
Include bolt torqueing requirements and gasket verification steps as part of the rebuild process.
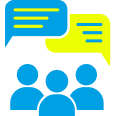
Ask yourself or your crew
Were there any warning signs indicating the pump should have been checked earlier?
What other actions would you have taken in this situation?
When equipment is updated, how do you know it is ‘better’? How can you check this?
What checklists do you have in place for rebuilding/repairing pumps? Have we missed any steps?
A multi-stage pump has been replaced with a single-stage CK-10 pump. On start up, it appeared to run normally, but then 3 hours later a fire broke out on the pump. The incident had potential for injury and production interruption.