-
What happened?
A technician was removing a rotor lock.
The turning gear was engaged with the brake off and the nacelle yawed into the wind.
A gust of wind at 15m/s(49 ft/s)
The technician’s glove was cut open and he received a minor friction burn. His hand could have been seriously injured.
-
Why did it happen?
The turning gear handle safety device malfunctioned. It should have automatically disengaged from the motor.
A strip down of the handle revealed that (see items 1,2 and 3 in image):
1. Spring had ridden up
2. Spring had signs of wear from abrasion against cassette
3. Bearing had been bent by the misplaced spring
The turbine was yawed into wind above 12m/s (39.5 ft/s). Investigation revealed this had become a routine breach of procedure on site.
The rotor lock had been removed using the electric motor with the brake off. This was also discovered to be a routine procedural violation.
-
What did they learn?
Introduce pre-use checks on turning gear handles.
Introduce routine maintenance on turning gear handles.
Upgrade all turning gear handles to an improved design where necessary.
Reinforce the procedure for yawing turbines out of the wind.
Consider regular audits to check if turbines are yawed out of the wind.
Review procedure for inserting and removing rotor locks.
Arrange regular workshops for feedback from technicians on effectiveness of procedures.
-
Ask yourself or your crew
What checks do you need to do on your equipment before starting work today? If something is wrong, who do you report it to?
What is the safe way to remove a rotor lock? What is the worst that could happen if the procedure is breached?
What controls do we have to prevent similar incidents on site? What else can we do to improve?
Are there any procedures that we routinely do not follow? Why? What can we do to improve the procedure?
Add to homescreen
Content name
Select existing category:
Content name
New collection
Edit collection
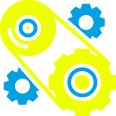
What happened?
A technician was removing a rotor lock.
The turning gear was engaged with the brake off and the nacelle yawed into the wind.
A gust of wind at 15m/s(49 ft/s) made the rotor move, prompting the technician to grab the turning gear handle.
The technician’s glove was cut open and he received a minor friction burn. His hand could have been seriously injured.
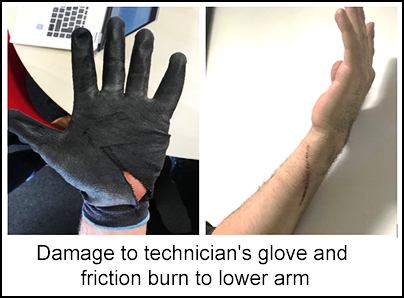
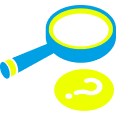
Why did it happen?
The turning gear handle safety device malfunctioned. It should have automatically disengaged from the motor.
A strip down of the handle revealed that (see items 1,2 and 3 in image):
1. Spring had ridden up
2. Spring had signs of wear from abrasion against cassette
3. Bearing had been bent by the misplaced spring
The turbine was yawed into wind above 12m/s (39.5 ft/s). Investigation revealed this had become a routine breach of procedure on site.
The rotor lock had been removed using the electric motor with the brake off. This was also discovered to be a routine procedural violation.
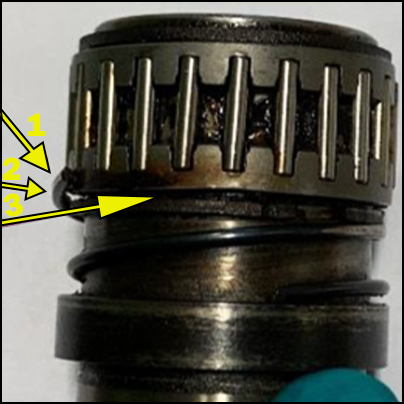
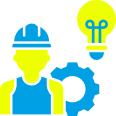
What did they learn?
Introduce pre-use checks on turning gear handles.
Introduce routine maintenance on turning gear handles.
Upgrade all turning gear handles to an improved design where necessary.
Reinforce the procedure for yawing turbines out of the wind.
Consider regular audits to check if turbines are yawed out of the wind.
Review procedure for inserting and removing rotor locks.
Arrange regular workshops for feedback from technicians on effectiveness of procedures.
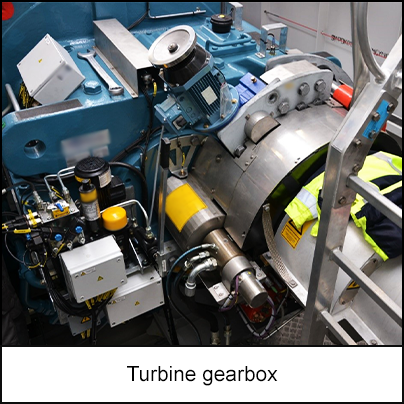
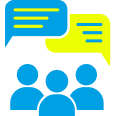
Ask yourself or your crew
What checks do you need to do on your equipment before starting work today? If something is wrong, who do you report it to?
What is the safe way to remove a rotor lock? What is the worst that could happen if the procedure is breached?
What controls do we have to prevent similar incidents on site? What else can we do to improve?
Are there any procedures that we routinely do not follow? Why? What can we do to improve the procedure?
During a rotor lock removal task, a technician’s glove was cut open and he received a minor friction burn. His hand could have been seriously injured.