-
What happened?
Rich fuel gas was released into the atmosphere when a 70mm long section of an O-ring was ejected from the sealing area of the filter pot lid.
-
Why did it happen?
The lid was not installed into the correct fully seated position, which allowed the O-ring to be pushed out by process pressure.
The lid would not sit into its correct position due to excessive clearance in the hinge pin.
The failure was not detected because the pressure test was not performed at full operating pressure.
-
What did they learn?
- Redesign lid with a weld-neck flange and spiral wound gasket seal.
- Review all other services on site for similar design.
- Ensure standards require robust design of all filter units in pressurised hydrocarbon service.
- Ensure appropriate reviews are undertaken by reinforcing the use of existing tools (OIS, 5Y, Logs, MRDF, IMPACT, etc.) to highlight recurring return-to-service testing deficiencies.
- Review pressure testing requirements for equipment before returning to service.
-
Ask yourself or your crew
How can something like this happen here?
How do you check if the lid has been installed in the correct fully seated position?
How do you know if the equipment has been adequately pressure tested before returning to service?
Add to homescreen
If you want to add this app to home screen tap and then ‘Add to Home Screen’.
Content name
Select existing category:
Content name
New collection
Edit collection
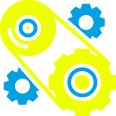
What happened?
Rich fuel gas was released into the atmosphere when a 70mm long section of an O-ring was ejected from the sealing area of the filter pot lid.
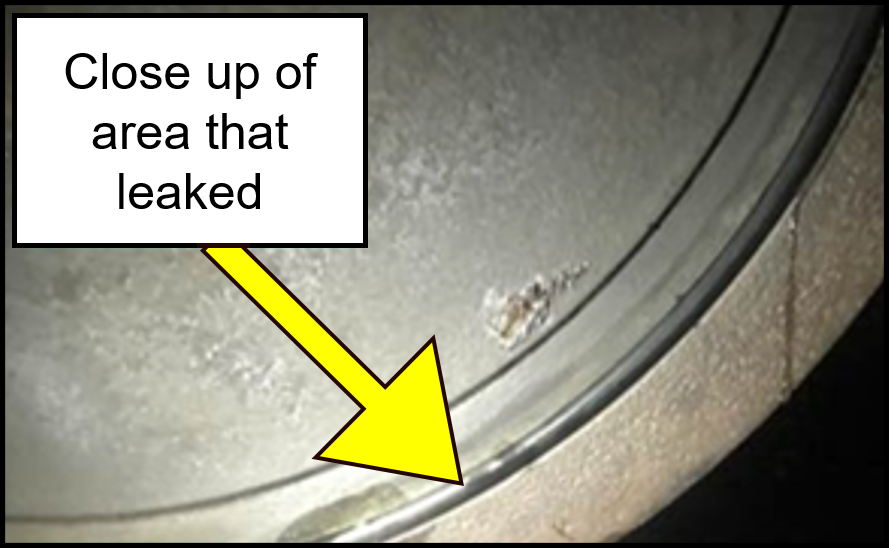
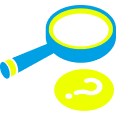
Why did it happen?
The lid was not installed into the correct fully seated position, which allowed the O-ring to be pushed out by process pressure.
The lid would not sit into its correct position due to excessive clearance in the hinge pin.
The failure was not detected because the pressure test was not performed at full operating pressure.
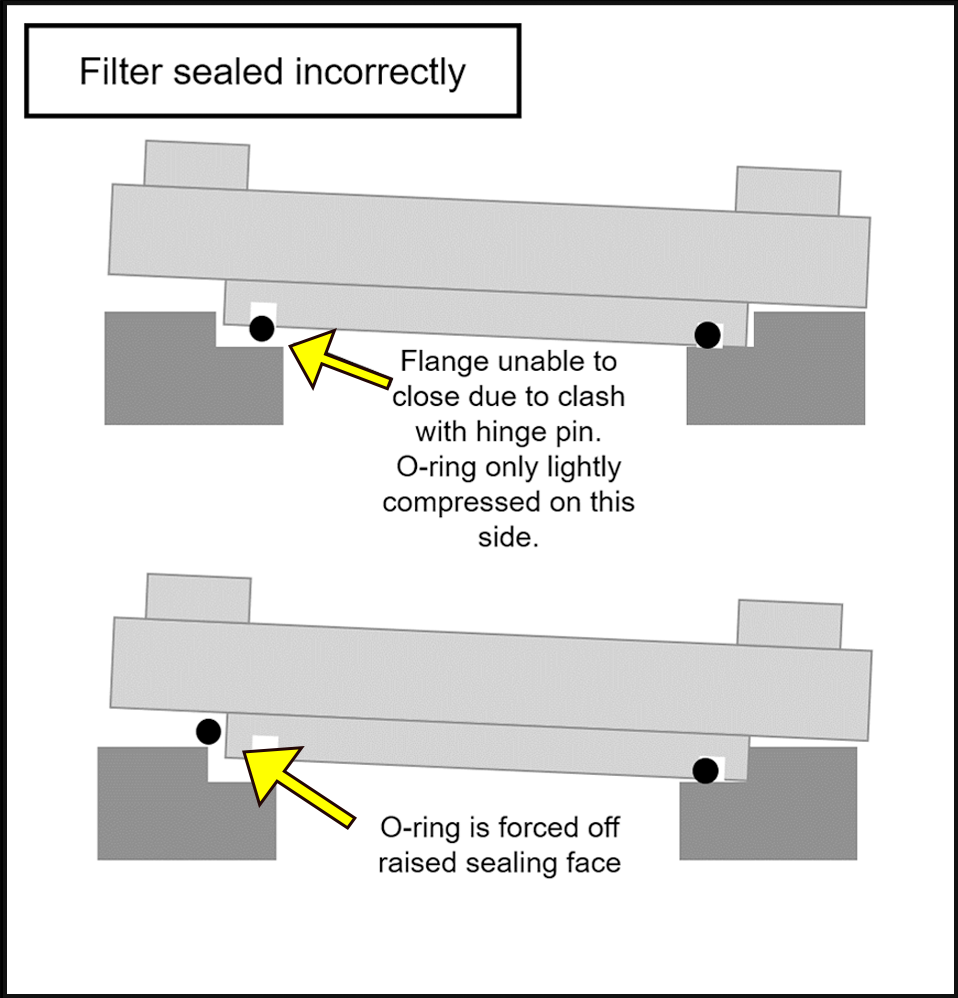
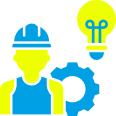
What did they learn?
- Redesign lid with a weld-neck flange and spiral wound gasket seal.
- Review all other services on site for similar design.
- Ensure standards require robust design of all filter units in pressurised hydrocarbon service.
- Ensure appropriate reviews are undertaken by reinforcing the use of existing tools (OIS, 5Y, Logs, MRDF, IMPACT, etc.) to highlight recurring return-to-service testing deficiencies.
- Review pressure testing requirements for equipment before returning to service.
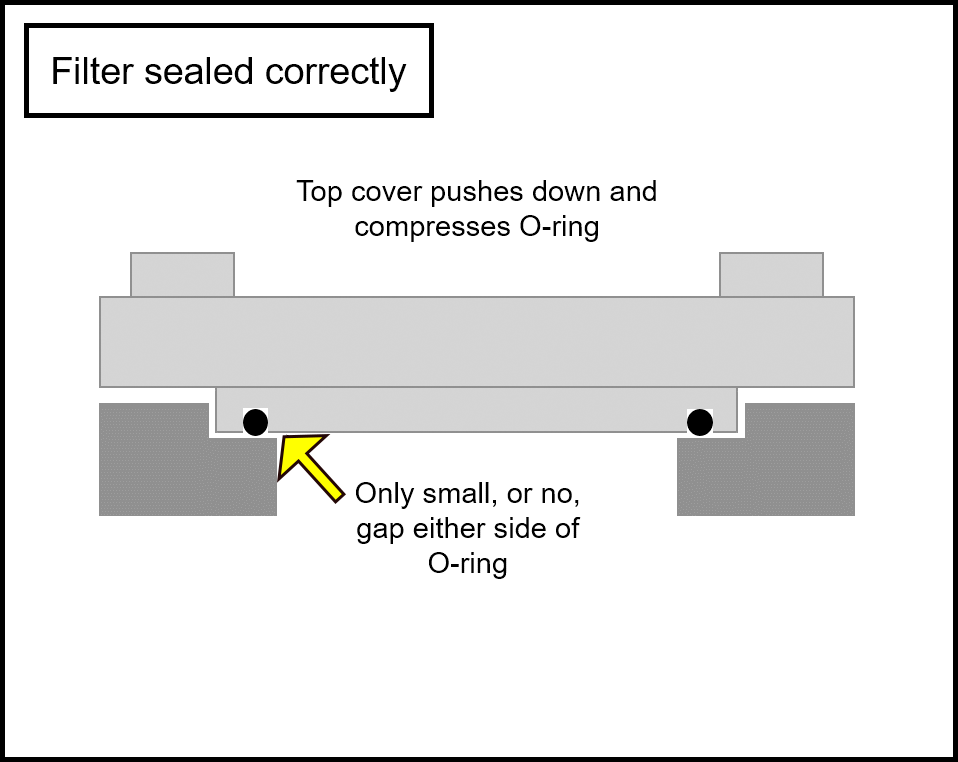
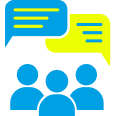
Ask yourself or your crew
How can something like this happen here?
How do you check if the lid has been installed in the correct fully seated position?
How do you know if the equipment has been adequately pressure tested before returning to service?
Published on 15/07/19
3027 Views
Rich fuel gas was released into the atmosphere when an O-ring was ejected from the sealing area of the filter pot lid. Upon investigation, it was revealed that the pressure test was not performed at maximum pressure and the lid was incorrectly installed.