-
What happened?
At a well pad, a ‘Y’ section of a gas flowline was being replaced using a 40 metric tons crane.
The crane fell laterally on its right side until its boom came to rest on a nearby metallic walkway structure.
The crane boom ended up at a 45° angle.
No one was injured, the only damage was to the walkway. The crane was non-operational for 22 hours.
-
Why did it happen?
The crane load capacity was exceeded. The crane’s load moment indicator (LMI) system was ignored during the operation as it had been intermittently faulty.
The crane was located in an improper position for the hoisting task.
The crane had other maintenance issues that hadn’t been addressed (loose bolts, oil leaks etc).
Lifting procedures were not followed (only a generic lift plan was being used and verification checklists weren’t completed).
Lack of experience of the crane operator – they did not identify the risks associated with the task.
Lack of supervision before and during the task.
The need to finish the task quickly was prioritised over safety.
-
What did they learn?
Ensure all workers (operating company and contractors) understand the need to comply with applicable standards.
Prepare an audit plan to verify the compliance of all workers with applicable standards.
Review the equipment inspection procedure to ensure that all equipment is fit for purpose before use.
Workers should receive training in hazard identification, risk assessment and work control procedures.
Prepare a preventive maintenance plan for securing the provision of spare parts where required.
Review the current competency management framework, especially regarding those positions which require authorising specific permits.
-
Ask yourself or your crew
What should you do about equipment that had an intermittent fault?
What is your maintenance procedure for your cranes and how do you record it?
How is your work plan communicated and what should you do if it’s not clear or you have concerns about the procedure?
Think of a time when you were under pressure to work quickly rather than safely. Why was that?
How can we improve our procedures to avoid similar incidents?
Add to homescreen
Content name
Select existing category:
Content name
New collection
Edit collection
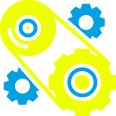
What happened?
At a well pad, a ‘Y’ section of a gas flowline was being replaced using a 40 metric tons crane.
The crane fell laterally on its right side until its boom came to rest on a nearby metallic walkway structure.
The crane boom ended up at a 45° angle.
No one was injured, the only damage was to the walkway. The crane was non-operational for 22 hours.
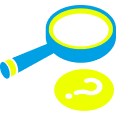
Why did it happen?
The crane load capacity was exceeded. The crane’s load moment indicator (LMI) system was ignored during the operation as it had been intermittently faulty.
The crane was located in an improper position for the hoisting task.
The crane had other maintenance issues that hadn’t been addressed (loose bolts, oil leaks etc).
Lifting procedures were not followed (only a generic lift plan was being used and verification checklists weren’t completed).
Lack of experience of the crane operator – they did not identify the risks associated with the task.
Lack of supervision before and during the task.
The need to finish the task quickly was prioritised over safety.
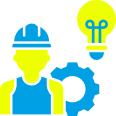
What did they learn?
Ensure all workers (operating company and contractors) understand the need to comply with applicable standards.
Prepare an audit plan to verify the compliance of all workers with applicable standards.
Review the equipment inspection procedure to ensure that all equipment is fit for purpose before use.
Workers should receive training in hazard identification, risk assessment and work control procedures.
Prepare a preventive maintenance plan for securing the provision of spare parts where required.
Review the current competency management framework, especially regarding those positions which require authorising specific permits.
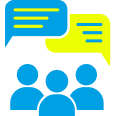
Ask yourself or your crew
What should you do about equipment that had an intermittent fault?
What is your maintenance procedure for your cranes and how do you record it?
How is your work plan communicated and what should you do if it’s not clear or you have concerns about the procedure?
Think of a time when you were under pressure to work quickly rather than safely. Why was that?
How can we improve our procedures to avoid similar incidents?
A section of a gas flowline was being replaced using a crane. The crane fell laterally on its right side until its boom came to rest on a nearby metallic walkway structure.