-
What happened?
A worker was stripping down a tree actuator as part of a well suspension programme.
The outer can of the actuator was removed, exposing the actuator springs.
These springs can be removed by slowly backing out the spring retainer plate, until all spring tension is released (46 turns). A further 8 turns should unscrew the retainer plate completely and the springs can then be removed without tension.
While backing out the spring retainer plate, the piston downstop (secured with 2 Allen screws) also backed off. By design, the downstop should have stayed in place.
After 7 more turns the downstop was fully unscrewed.
The spring and retainer plate were ejected under tension and landed 8 metres (26 feet) away from the tree, hitting a scaffold platform.
No one was injured as the risk of an uncontrolled spring tension release was identified and no personnel was positioned in front of the actuator.
-
Why did it happen?
The piston downstop Allen screws were not engaged properly – they were confirmed to be tight before the spring removal, but not all the way in.
It is difficult to notice piston downstop movement while backing out the spring retainer plate, especially with springs installed.
-
What did they learn?
Verify that piston downstop Allen screws are fully screwed in prior to spring retainer plate removal.
Continuously monitor for piston downstop movement by installing a small ‘flag’ in an Allen screw hole. This can indicate unintentional rotation.
-
Ask yourself or your crew
How can something like this happen here?
What is our procedure for disassembling actuators?
What are the hazards associated with this type of work, and what mitigation measures do we have in place?
What safety checks do you carry out before, during, and after carrying out your tasks?
Are there any additional safety measures that could be considered for your equipment?
Add to homescreen
Content name
Select existing category:
Content name
New collection
Edit collection
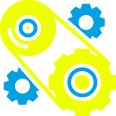
What happened?
A worker was stripping down a tree actuator as part of a well suspension programme.
The outer can of the actuator was removed, exposing the actuator springs.
These springs can be removed by slowly backing out the spring retainer plate, until all spring tension is released (46 turns). A further 8 turns should unscrew the retainer plate completely and the springs can then be removed without tension.
While backing out the spring retainer plate, the piston downstop (secured with 2 Allen screws) also backed off. By design, the downstop should have stayed in place.
After 7 more turns the downstop was fully unscrewed.
The spring and retainer plate were ejected under tension and landed 8 metres (26 feet) away from the tree, hitting a scaffold platform.
No one was injured as the risk of an uncontrolled spring tension release was identified and no personnel was positioned in front of the actuator.
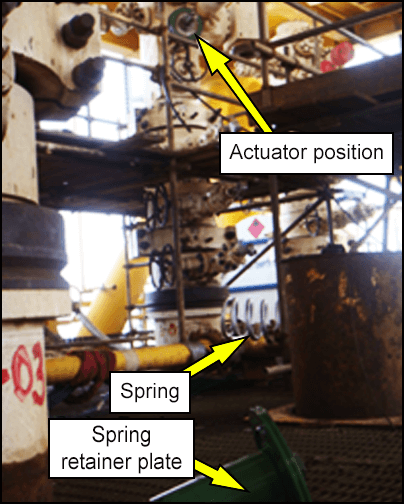
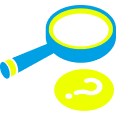
Why did it happen?
The piston downstop Allen screws were not engaged properly – they were confirmed to be tight before the spring removal, but not all the way in.
It is difficult to notice piston downstop movement while backing out the spring retainer plate, especially with springs installed.
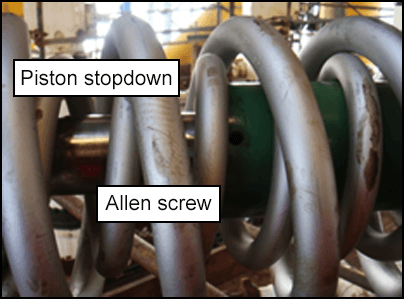
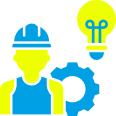
What did they learn?
Verify that piston downstop Allen screws are fully screwed in prior to spring retainer plate removal.
Continuously monitor for piston downstop movement by installing a small ‘flag’ in an Allen screw hole. This can indicate unintentional rotation.
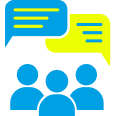
Ask yourself or your crew
How can something like this happen here?
What is our procedure for disassembling actuators?
What are the hazards associated with this type of work, and what mitigation measures do we have in place?
What safety checks do you carry out before, during, and after carrying out your tasks?
Are there any additional safety measures that could be considered for your equipment?
A worker was stripping down a tree actuator. While backing out the spring retainer plate, the piston downstop became unscrewed. The spring and retainer plate were ejected, landing 8 metres (26 feet) away.