-
What happened?
A workover crew was retrieving the test assembly that had been left landed in the tubing head to isolate the well overnight (hanger with two-way-check, 25cm/10in landing joint, and full opening safety valve).
A wireline set packer with plug was run to liner top the previous day to prepare for gas lift.
The blowout preventers (BOPs) were previously opened to ensure pressure was bled off above the test assembly.
The derrick hand began backing out the lockdown pins that retained the hanger, and the test assembly was ejected from the well.
The 122kg (270lbs) test assembly was projected 9m (30ft) into the air.
The floor hand was standing on the rig floor 60cm (2ft) from the well bore at that time of the incident.
They were sprayed with fluid in their eyes and given first aid.
The rig operator shut the well in from the accumulator by closing the blind rams.
-
Why did it happen?
The casing pressure gauge was removed to pump a sweep prior to running the packer and had not been reinstalled.
The operator failed to verify zero pressure on the casing but documented zero pressure on the job safety analysis (JSA) and reported this to the company consultant.
The derrick hand failed to verify zero pressure on the casing and tubing.
Only 3 of 8 lockdown pins were engaged by the wellhead service provider.
The JSA did not note the steps or hazards of backing out the lockdown pins and removing the test assembly.
Non-compliance: The crew broke their company policy by having a man on the floor and one beneath the floor.
The consultant did not meet expectations for use of the wellwork risk assessment, rig up checklist, or being at the wellhead for key activities.
-
What did they learn?
Confirm workers can explain JSA hazard controls and standard operating practices (SOPs) steps. Provide training/refresher as required.
Conduct training sessions (second line supervisor to first line supervisors) on what ‘good’ looks like for SOPs and lifesaving actions, so there is effective oversight and work authorisation.
Perform periodic assessments of wellwork to verify consistent execution of SOPs.
-
Ask yourself or your crew
What could they have done differently to prevent this incident?
Are you fully trained and competent to perform your tasks? What should you do if not?
What are the standard operating practice steps for this type of activity?
What should you do if you see a hazard on the worksite that was not considered?
What procedures and safety measures do we have in place to prevent this from happening here? How can we improve?
Add to homescreen
Content name
Select existing category:
Content name
New collection
Edit collection
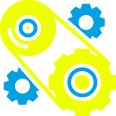
What happened?
A workover crew was retrieving the test assembly that had been left landed in the tubing head to isolate the well overnight (hanger with two-way-check, 25cm/10in landing joint, and full opening safety valve).
A wireline set packer with plug was run to liner top the previous day to prepare for gas lift.
The blowout preventers (BOPs) were previously opened to ensure pressure was bled off above the test assembly.
The derrick hand began backing out the lockdown pins that retained the hanger, and the test assembly was ejected from the well.
The 122kg (270lbs) test assembly was projected 9m (30ft) into the air.
The floor hand was standing on the rig floor 60cm (2ft) from the well bore at that time of the incident.
They were sprayed with fluid in their eyes and given first aid.
The rig operator shut the well in from the accumulator by closing the blind rams.
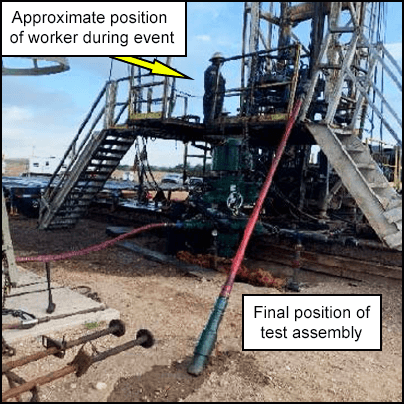
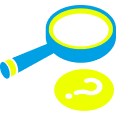
Why did it happen?
The casing pressure gauge was removed to pump a sweep prior to running the packer and had not been reinstalled.
The operator failed to verify zero pressure on the casing but documented zero pressure on the job safety analysis (JSA) and reported this to the company consultant.
The derrick hand failed to verify zero pressure on the casing and tubing.
Only 3 of 8 lockdown pins were engaged by the wellhead service provider.
The JSA did not note the steps or hazards of backing out the lockdown pins and removing the test assembly.
Non-compliance: The crew broke their company policy by having a man on the floor and one beneath the floor.
The consultant did not meet expectations for use of the wellwork risk assessment, rig up checklist, or being at the wellhead for key activities.
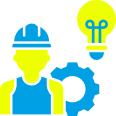
What did they learn?
Confirm workers can explain JSA hazard controls and standard operating practices (SOPs) steps. Provide training/refresher as required.
Conduct training sessions (second line supervisor to first line supervisors) on what ‘good’ looks like for SOPs and lifesaving actions, so there is effective oversight and work authorisation.
Perform periodic assessments of wellwork to verify consistent execution of SOPs.
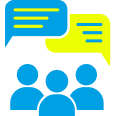
Ask yourself or your crew
What could they have done differently to prevent this incident?
Are you fully trained and competent to perform your tasks? What should you do if not?
What are the standard operating practice steps for this type of activity?
What should you do if you see a hazard on the worksite that was not considered?
What procedures and safety measures do we have in place to prevent this from happening here? How can we improve?
A crew was removing a BOP test assembly when the assembly’s lockdown pins failed and the assembly was projected into the air.