-
What happened?
A temporary stairway between a rig and a flotel was being removed.
It was being dismantled and lifted to the deck using a beam clamp on a monorail, an air tucker and winch, and rigging.
The load got stuck in a gap.
As the rigging supervisor tried to unblock it, the beam clamp came off the end of the monorail, striking his head and shattering his hard hat.
-
Why did it happen?
The load was too big to fit through the gap.
The worker put himself in the line of fire between the winch and beam clamp.
The beam clamp was pulled off the end due to side loading imparted by the winch. Beam clamps are not designed to withstand side-loading of more than 3 degrees.
The end stops were designed for the trolley hoist, not the beam clamp. Beam clamps do not require end stops if properly used.
The job was not stopped when things did not go to plan.
-
What did they learn?
Do not use beam clamps for lifting. Use the right equipment for the planned task.
When circumstances change, stop, think and reassess the risk.
Always consider rigging failure - never put yourself in the line of fire.
Winch operations should be smooth and controlled – if you need to toggle the load up and down then it means the task needs to be stopped.
-
Ask yourself or your crew
What other actions could have been taken?
How can something like this happen here?
Why do you think the rigging supervisor acted as he did?
What lessons from this incident can we apply to our lifting operations?
Add to homescreen
Content name
Select existing category:
Content name
New collection
Edit collection
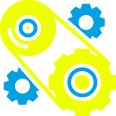
What happened?
A temporary stairway between a rig and a flotel was being removed.
It was being dismantled and lifted to the deck using a beam clamp on a monorail, an air tucker and winch, and rigging.
The load got stuck in a gap.
As the rigging supervisor tried to unblock it, the beam clamp came off the end of the monorail, striking his head and shattering his hard hat.
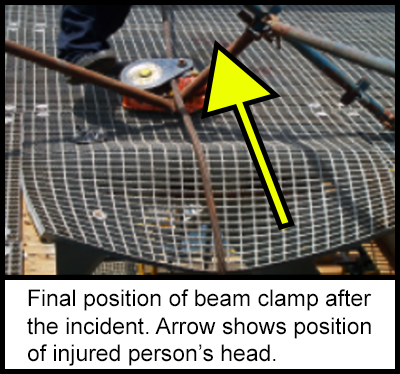
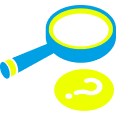
Why did it happen?
The load was too big to fit through the gap.
The worker put himself in the line of fire between the winch and beam clamp.
The beam clamp was pulled off the end due to side loading imparted by the winch. Beam clamps are not designed to withstand side-loading of more than 3 degrees.
The end stops were designed for the trolley hoist, not the beam clamp. Beam clamps do not require end stops if properly used.
The job was not stopped when things did not go to plan.
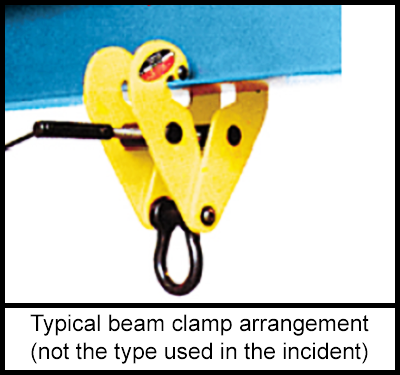
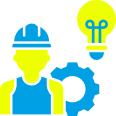
What did they learn?
Do not use beam clamps for lifting. Use the right equipment for the planned task.
When circumstances change, stop, think and reassess the risk.
Always consider rigging failure - never put yourself in the line of fire.
Winch operations should be smooth and controlled – if you need to toggle the load up and down then it means the task needs to be stopped.
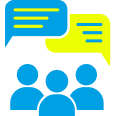
Ask yourself or your crew
What other actions could have been taken?
How can something like this happen here?
Why do you think the rigging supervisor acted as he did?
What lessons from this incident can we apply to our lifting operations?
A temporary stairway between a rig and a flotel was being removed. The load got stuck in a gap. As the rigging supervisor tried to unblock it, the beam clamp came off the end of the monorail, striking his head and shattering his hard hat.