-
What happened?
A joint of special clearance coupling 9-7/8 inches casing (1100 kg) was being lifted to the rotary center.
The side-door elevators opened, allowing the casing to drop to the rig floor.
Two workers were positioned within the exclusion zone.
No injuries were sustained.
-
Why did it happen?
Side-door elevators were not retrofitted with required secondary safety latch lock pin as per the original equipment manufacturer’s alert.
Processes and procedures allowed the elevator to be run without the secondary safety latch lock-pin.
No clear guidelines on where the rig crew should be positioned during casing lifting operations, when casing running equipment is not operated.
-
What did they learn?
There are many different designs for elevator latching mechanisms.
- Older models require a pin to be inserted after the latch has been closed – to fully close and lock the hatch
- Newer designs use a secondary lock into the latching mechanism.
Operators need to:
- Understand what type of elevators they work with
- Understand where they should be positioned during operations
- Be aware of any manufacturer’s modification recommendations
-
Ask yourself or your crew
What other actions could have been taken?
How can something like this happen here?
Where can you safely stand during lifting operations? Do you find there are times on our site you must enter exclusion zones?
What type of elevators do we use?
How are you responsible for recognising and making any modifications to the original design if necessary?
Add to homescreen
Content name
Select existing category:
Content name
New collection
Edit collection
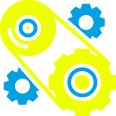
What happened?
A joint of special clearance coupling 9-7/8 inches casing (1100 kg) was being lifted to the rotary center.
The side-door elevators opened, allowing the casing to drop to the rig floor.
Two workers were positioned within the exclusion zone.
No injuries were sustained.

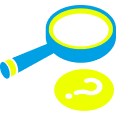
Why did it happen?
Side-door elevators were not retrofitted with required secondary safety latch lock pin as per the original equipment manufacturer’s alert.
Processes and procedures allowed the elevator to be run without the secondary safety latch lock-pin.
No clear guidelines on where the rig crew should be positioned during casing lifting operations, when casing running equipment is not operated.
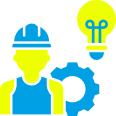
What did they learn?
There are many different designs for elevator latching mechanisms.
- Older models require a pin to be inserted after the latch has been closed – to fully close and lock the hatch
- Newer designs use a secondary lock into the latching mechanism.
Operators need to:
- Understand what type of elevators they work with
- Understand where they should be positioned during operations
- Be aware of any manufacturer’s modification recommendations
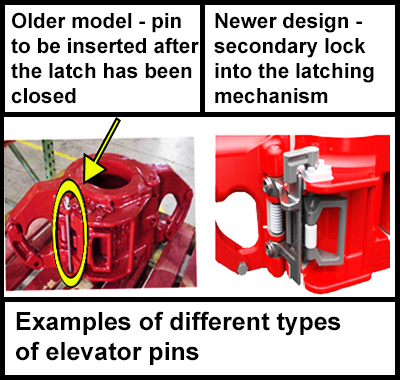
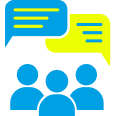
Ask yourself or your crew
What other actions could have been taken?
How can something like this happen here?
Where can you safely stand during lifting operations? Do you find there are times on our site you must enter exclusion zones?
What type of elevators do we use?
How are you responsible for recognising and making any modifications to the original design if necessary?
A joint was being lifted to the rotary center. The side-door elevators opened, allowing the casing to drop to the rig floor. Two workers were positioned in the exclusion zone, but fortunately, no injuries were sustained.