-
What happened?
An oxygen/ethylene cutting torch and hose was disconnected from a gas manifold at the end of shift.
The torch was stored in a steel toolbox. The hose was left hanging near the manifold.
The hose was later reconnected to the manifold by the nightshift operators. Gas started to accumulate in and around the toolbox.
Nearby gouging work ignited the gas causing an explosion.
The toolbox and deluge skid were damaged.
-
Why did it happen?
Nightshift workers connected the hose nipple to the gas manifold without a pre-check verification.
The gas torch valve had been left in the ‘open’ position. Once the hose nipple was connected to the manifold, gas started to accumulate.
Energy containment: insufficient spark and slag containment for nearby gouging operations.
-
What did they learn?
The following barriers must be in place:
- Hot work procedure
- Spark containment
- Gas testing
- Hose management and identification
-
Ask yourself or your crew
How could something like this happen here?
Why do you think they connected the hoses without checking?
What specific barriers/controls do we have in place that could prevent this? Consider:
- Hot work procedure
- Spark containment
- Gas testing
- Hose management and identification
Add to homescreen
Content name
Select existing category:
Content name
New collection
Edit collection
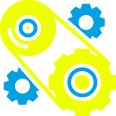
What happened?
An oxygen/ethylene cutting torch and hose was disconnected from a gas manifold at the end of shift.
The torch was stored in a steel toolbox. The hose was left hanging near the manifold.
The hose was later reconnected to the manifold by the nightshift operators. Gas started to accumulate in and around the toolbox.
Nearby gouging work ignited the gas causing an explosion.
The toolbox and deluge skid were damaged.
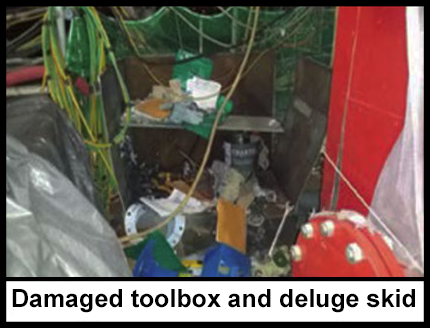
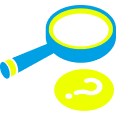
Why did it happen?
Nightshift workers connected the hose nipple to the gas manifold without a pre-check verification.
The gas torch valve had been left in the ‘open’ position. Once the hose nipple was connected to the manifold, gas started to accumulate.
Energy containment: insufficient spark and slag containment for nearby gouging operations.
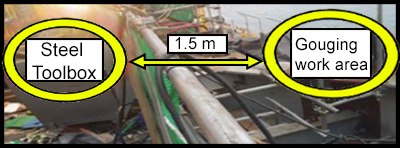
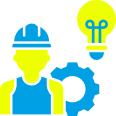
What did they learn?
The following barriers must be in place:
- Hot work procedure
- Spark containment
- Gas testing
- Hose management and identification
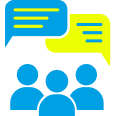
Ask yourself or your crew
How could something like this happen here?
Why do you think they connected the hoses without checking?
What specific barriers/controls do we have in place that could prevent this? Consider:
- Hot work procedure
- Spark containment
- Gas testing
- Hose management and identification
No pre-checks were made before hooking a cutting torch hose a to a manifold, leading to an accumulation of gas close to an area where gouging work was being carried out. The gas ignited, causing an explosion.