-
What happened?
The stitch welds between a vertical line packer and the pipe support failed.
The 8kg (17.6 lb) vertical line packer fell 10 metres (33 feet) to grade.
There were no injuries associated with this incident.
-
Why did it happen?
The packer was stitch welded when it should have been full seal welded.
The stitch welds between the vertical packer and the pipe support had crevice corrosion jacking and failed – leading to the dropped packer.
The packer only showed signs of surface corrosion, with no obvious indications that the welds were failing. Inspection procedures were inadequate as they did not detect the potential for failure.
Stitch welds have a life of 20 years but this was exceeded. The quality assurance process should have picked up on the fact that stitch welds had been used.
-
What did they learn?
Ensure that quality assurance processes identify stitch welds and factor in their life expectancy.
Update engineering standards and global piping and inspection procedures to:
- Ensure all packers are full seal welded.
- Specifically identify packers, pipe shoes and other susceptible items that may suffer weld failure.
-
Ask yourself or your crew
How can something like this happen here?
How can you identify corrosion in welds?
Have packers been stitch welded on our site? How can we identify this?
What other items might be subject to weld failure due to corrosion or age?
What else can we do to prevent this happening here?
Add to homescreen
Content name
Select existing category:
Content name
New collection
Edit collection
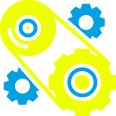
What happened?
The stitch welds between a vertical line packer and the pipe support failed.
The 8kg (17.6 lb) vertical line packer fell 10 metres (33 feet) to grade.
There were no injuries associated with this incident.
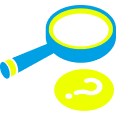
Why did it happen?
The packer was stitch welded when it should have been full seal welded.
The stitch welds between the vertical packer and the pipe support had crevice corrosion jacking and failed – leading to the dropped packer.
The packer only showed signs of surface corrosion, with no obvious indications that the welds were failing. Inspection procedures were inadequate as they did not detect the potential for failure.
Stitch welds have a life of 20 years but this was exceeded. The quality assurance process should have picked up on the fact that stitch welds had been used.
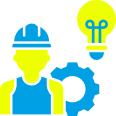
What did they learn?
Ensure that quality assurance processes identify stitch welds and factor in their life expectancy.
Update engineering standards and global piping and inspection procedures to:
- Ensure all packers are full seal welded.
- Specifically identify packers, pipe shoes and other susceptible items that may suffer weld failure.
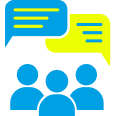
Ask yourself or your crew
How can something like this happen here?
How can you identify corrosion in welds?
Have packers been stitch welded on our site? How can we identify this?
What other items might be subject to weld failure due to corrosion or age?
What else can we do to prevent this happening here?
The stitch welds between a vertical line packer and the pipe support failed. The vertical line packer fell 10 metres to grade.