-
What happened?
A drilling crew were laying down the cementing pipe string when they discovered a brass thrust washer on the ground of the drill floor.
Washer had fallen from the inside of the top sheave in the crown assembly of the rig derrick, missing the nearest worker by 2m (6.5ft).
Dropped object had a diameter of 25cm (0.8ft) and weighed 0.68kg (1.5lbs)
Crew performed visual inspection from the ground using a telephoto lens and mobilised a crane equipped with a man basket to inspect and repair the crown.
It was identified that:
- Sheave pin (which forms the axle for the sheave) had moved laterally and was noticeably leaning from its normal, vertical position.
- Outer sheave locking plate bolts had sheared and the plate itself was resting on the edge of the crown assembly.
Rig operations were suspended as the conditions identified created potential for a more serious incident.
-
Why did it happen?
Bolts securing the locking plate in place on the crown housing had become loose over time, allowing the locking plate to touch the sheave pin.
Continued movement from the sheave pin onto the locking plates resulted in wear on the locking plate bolts and caused the failure of the bolts.
Restricted access to locking plates did not allow workers to clearly identify the backing off the locking plate bolts.
Product specifications showed no requirement to:
- torque the crown pin keeper plate bolts to a specified range.
- perform regular inspections on this area of the rig.
-
What did they learn?
Ensure each locking plate and bolts are secured before the derrick is raised.
- Lock plate bolts should be torqued.
- Include procedure in all job safety analysis (JSA) and standard operating procedure (SOP) for completing pre-raise derrick inspection, as well as in the inspection itself.
Rig managers should inspect the crown assembly and sheave pins from ground level (with provided binoculars) during daily inspections.
-
Ask yourself or your crew
Has anything like this happened on your worksite?
How do you inspect pieces of equipment that are not easy to access?
What is your preventative maintenance regime for equipment on site?
What equipment is presumed ‘low risk’ or ‘low maintenance’ on our site? Is it actually?
Add to homescreen
Content name
Select existing category:
Content name
New collection
Edit collection
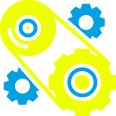
What happened?
A drilling crew were laying down the cementing pipe string when they discovered a brass thrust washer on the ground of the drill floor.
Washer had fallen from the inside of the top sheave in the crown assembly of the rig derrick, missing the nearest worker by 2m (6.5ft).
Dropped object had a diameter of 25cm (0.8ft) and weighed 0.68kg (1.5lbs)
Crew performed visual inspection from the ground using a telephoto lens and mobilised a crane equipped with a man basket to inspect and repair the crown.
It was identified that:
- Sheave pin (which forms the axle for the sheave) had moved laterally and was noticeably leaning from its normal, vertical position.
- Outer sheave locking plate bolts had sheared and the plate itself was resting on the edge of the crown assembly.
Rig operations were suspended as the conditions identified created potential for a more serious incident.
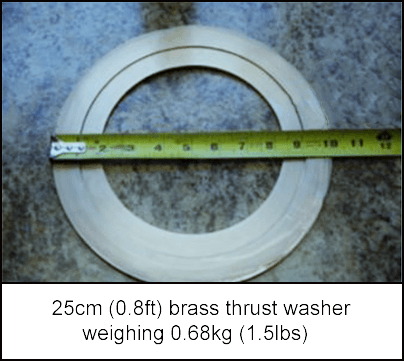
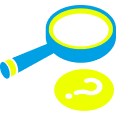
Why did it happen?
Bolts securing the locking plate in place on the crown housing had become loose over time, allowing the locking plate to touch the sheave pin.
Continued movement from the sheave pin onto the locking plates resulted in wear on the locking plate bolts and caused the failure of the bolts.
Restricted access to locking plates did not allow workers to clearly identify the backing off the locking plate bolts.
Product specifications showed no requirement to:
- torque the crown pin keeper plate bolts to a specified range.
- perform regular inspections on this area of the rig.
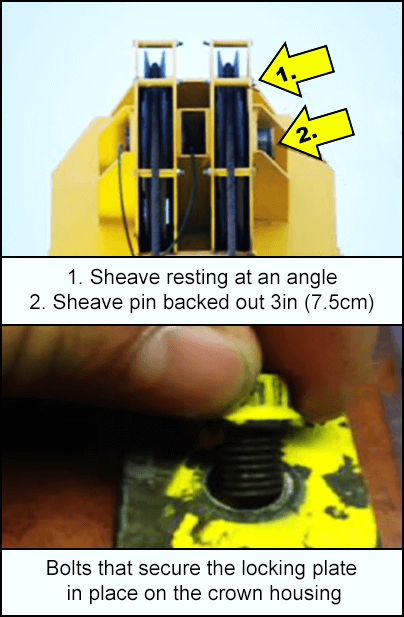
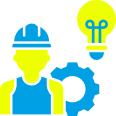
What did they learn?
Ensure each locking plate and bolts are secured before the derrick is raised.
- Lock plate bolts should be torqued.
- Include procedure in all job safety analysis (JSA) and standard operating procedure (SOP) for completing pre-raise derrick inspection, as well as in the inspection itself.
Rig managers should inspect the crown assembly and sheave pins from ground level (with provided binoculars) during daily inspections.
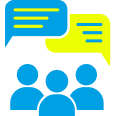
Ask yourself or your crew
Has anything like this happened on your worksite?
How do you inspect pieces of equipment that are not easy to access?
What is your preventative maintenance regime for equipment on site?
What equipment is presumed ‘low risk’ or ‘low maintenance’ on our site? Is it actually?
A drilling crew were laying down the cementing pipe string when they discovered a brass thrust washer on the ground of the drill floor. The washer had fallen from the inside of the top sheave in the crown assembly of the rig derrick.