-
What happened?
Following pipe connection work on a steam-cracker unit, a blind was being removed on a regeneration effluents line.
When opening the circuit, a flash (flame and detonation) occurred.
A contractor was positioning the joint on to the flange when the flash happened. He was using flameproof tools (bronze wrench).
Luckily, no one was injured.
Work was immediately stopped.
The ignition energy source is not known. The electrical continuity was checked and was correct.
-
Why did it happen?
It was suspected the flash occurred due to inflammation of pyrophoric particles stuck in the flange.
Lines were plugged by coke and refractory fragments on the bottom side, and green-oils present in lines could have released light hydrocarbons.
This incident was linked to inadequate:
Design.
Maintenance and inspections (including poor planning).
Engineering and management of change.
Critical task analysis and procedures.
-
What did they learn?
Add a nitrogen purge/injection nozzle on recovery lines for regeneration effluents.
Include cleaning and unblocking of effluents admission lines during works on furnaces.
Systematically seal the holes of effluents in the furnace’s bottom with sandbags to avoid sending waste material to the manifolds when working in the radiation area.
Check the handover of circuits.
In case of risk of lines plugging, protect these exposed zones from a potential accumulation of materials during maintenance works.
-
Ask yourself or your crew
How can something like this happen here?
What do you think happened?
Before starting work, how do you know if lines have been cleaned and unblocked?
What changes can we make to our operations today to prevent something like this?
Add to homescreen
Content name
Select existing category:
Content name
New collection
Edit collection
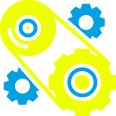
What happened?
Following pipe connection work on a steam-cracker unit, a blind was being removed on a regeneration effluents line.
When opening the circuit, a flash (flame and detonation) occurred.
A contractor was positioning the joint on to the flange when the flash happened. He was using flameproof tools (bronze wrench).
Luckily, no one was injured.
Work was immediately stopped.
The ignition energy source is not known. The electrical continuity was checked and was correct.
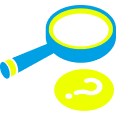
Why did it happen?
It was suspected the flash occurred due to inflammation of pyrophoric particles stuck in the flange.
Lines were plugged by coke and refractory fragments on the bottom side, and green-oils present in lines could have released light hydrocarbons.
This incident was linked to inadequate:
Design.
Maintenance and inspections (including poor planning).
Engineering and management of change.
Critical task analysis and procedures.
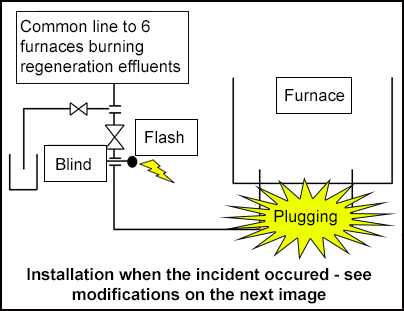
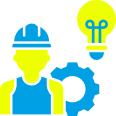
What did they learn?
Add a nitrogen purge/injection nozzle on recovery lines for regeneration effluents.
Include cleaning and unblocking of effluents admission lines during works on furnaces.
Systematically seal the holes of effluents in the furnace’s bottom with sandbags to avoid sending waste material to the manifolds when working in the radiation area.
Check the handover of circuits.
In case of risk of lines plugging, protect these exposed zones from a potential accumulation of materials during maintenance works.
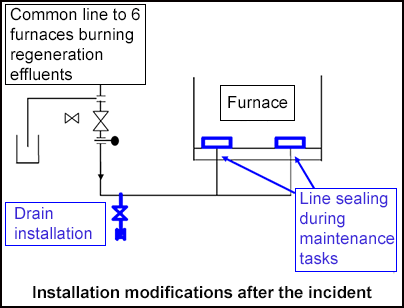
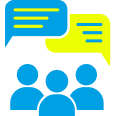
Ask yourself or your crew
How can something like this happen here?
What do you think happened?
Before starting work, how do you know if lines have been cleaned and unblocked?
What changes can we make to our operations today to prevent something like this?
Following pipe connection work on a steam-cracker unit, during the blind removal on a regeneration effluents line, a flash (flame and detonation) occurred when opening the circuit.