-
What happened?
A welding operation was being carried out on stainless steel piping above a vessel.
The subcontracting company had to create an inert atmosphere using argon and 3 plugs.
To do this, they removed the blind on top of the vessel, passed argon hoses through it and installed the plugs.
The vessel was approved for entry, air quality checks had been done and work permit had been approved.
The inspector entered the vessel through the manhole to start the inspection.
As soon as he entered, his gas detector started to alarm. He exited the vessel.
A check indicated an O2 content between 16 – 17%.
Access to the vessel was immediately suspended.
-
Why did it happen?
The subcontracting company had removed the blind on top of the vessel to pass the argon hoses through.
The blind had been removed without the permission of the operator.
The plug installed on top of the vessel was not gastight, allowing argon to flow backwards into the vessel.
-
What did they learn?
Blinds should never be removed without the approval of the operator/owner of the installation.
Always conduct a risk analysis before removing blinds.
Hoses carrying asphyxiant gases may only be used inside vessels with the approval of the operator/owner of the installation and only after a risk assessment.
Reminder: Argon (unlike nitrogen) is an inert gas heavier than air. So it stays at the bottom of confined spaces!
-
Ask yourself or your crew
How can something like this happen here?
Why do you think they removed the blind?
Have we ever deviated from the plan?
If we need to change the plan, how do we do this safely?
What inert gases are we using? So where do we need to check oxygen levels?
How do we know we have managed the risk of a confined space job?
Add to homescreen
Content name
Select existing category:
Content name
New collection
Edit collection
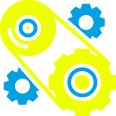
What happened?
A welding operation was being carried out on stainless steel piping above a vessel.
The subcontracting company had to create an inert atmosphere using argon and 3 plugs.
To do this, they removed the blind on top of the vessel, passed argon hoses through it and installed the plugs.
The vessel was approved for entry, air quality checks had been done and work permit had been approved.
The inspector entered the vessel through the manhole to start the inspection.
As soon as he entered, his gas detector started to alarm. He exited the vessel.
A check indicated an O2 content between 16 – 17%.
Access to the vessel was immediately suspended.
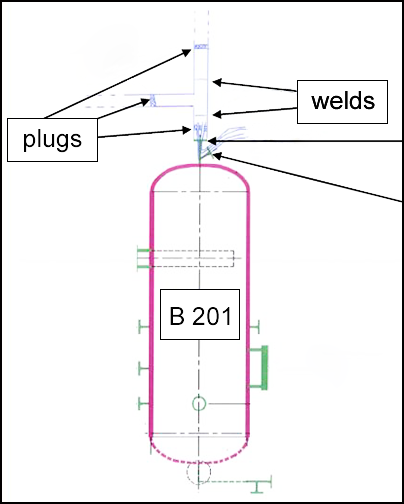
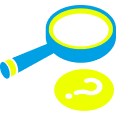
Why did it happen?
The subcontracting company had removed the blind on top of the vessel to pass the argon hoses through.
The blind had been removed without the permission of the operator.
The plug installed on top of the vessel was not gastight, allowing argon to flow backwards into the vessel.
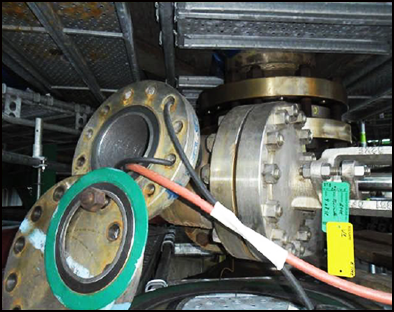
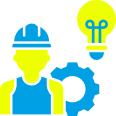
What did they learn?
Blinds should never be removed without the approval of the operator/owner of the installation.
Always conduct a risk analysis before removing blinds.
Hoses carrying asphyxiant gases may only be used inside vessels with the approval of the operator/owner of the installation and only after a risk assessment.
Reminder: Argon (unlike nitrogen) is an inert gas heavier than air. So it stays at the bottom of confined spaces!
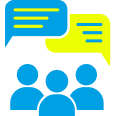
Ask yourself or your crew
How can something like this happen here?
Why do you think they removed the blind?
Have we ever deviated from the plan?
If we need to change the plan, how do we do this safely?
What inert gases are we using? So where do we need to check oxygen levels?
How do we know we have managed the risk of a confined space job?
Workers used argon to inert piping for welding. They removed a blind in a process vessel without authorisation. The inspector was exposed to argon when he entered the vessel. The plug was not gastight.