-
What happened?
Two welders were repairing an external weld on a vertically orientated 34" pipe spool.
After finishing, the first welder used a ladder to enter the pipe to inspect the repair.
The welder collapsed after entering the pipe due to entering an oxygen-depleted atmosphere.
The second welder entered the pipe to rescue the first, but also collapsed.
The safety adviser was alerted, and the site emergency response team (ERT) were called.
Workers positioned a fan blowing fresh air into the pipe.
Against the advice from colleagues, a third worker entered the pipe and tied a rope around one of the welders, hoisting him out.
Site ERT arrived – one of the ERT team entered the pipe and retrieved the second welder.
Both welders lost their lives.
-
Why did it happen?
Entry into the pipe spool was unplanned and unauthorised. The repair was supposed to be carried out externally, so the workers did not have confined space permit controls and had not undertaken risk management processes.
A poor-quality non-proprietary argon purge dam was used.
After removing the argon weld purge dam, no ventilation of the pipe spool occurred.
The pipe spool was not capped.
Neither argon or confined space advisory signs were on the pipe or in the purge area.
Onboarding induction contained limited information on inert gas safety.
-
What did they learn?
Ensure workers understand that entry into pipe spools should only be a last resort and under a confined space permit.
Ensure lockable covers are installed on open pipe ends greater than 18”.
Develop and implement the following training programmes:
- Installation, utilisation, and removal of purge dams.
- Inert gas awareness.
- Line blowing.
Improve safety signage on site.
Investigate other options to negate the need for argon purge welding.
Ensure identified defects are discussed with the welding engineer to determine correct diagnosis and associated repairs.
Ensure workers have the correct tools for their tasks.
Undertake a review of emergency response arrangements.
-
Ask yourself or your crew
Do we expect to need to enter a confined space to complete today’s activity?
Do you have all the correct permits in place for your work?
What do we have in place to prevent or deter people from entering confined spaces? (Think signage, equipment, procedures)
If confined space entry is required:
- Is there a safer way to do the job that doesn’t require confined space entry?
- What precautions have we put in place to ensure it is safe? What more can we do?
- What is our emergency response procedure?
Add to homescreen
Content name
Select existing category:
Content name
New collection
Edit collection
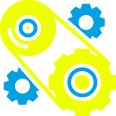
What happened?
Two welders were repairing an external weld on a vertically orientated 34" pipe spool.
After finishing, the first welder used a ladder to enter the pipe to inspect the repair.
The welder collapsed after entering the pipe due to entering an oxygen-depleted atmosphere.
The second welder entered the pipe to rescue the first, but also collapsed.
The safety adviser was alerted, and the site emergency response team (ERT) were called.
Workers positioned a fan blowing fresh air into the pipe.
Against the advice from colleagues, a third worker entered the pipe and tied a rope around one of the welders, hoisting him out.
Site ERT arrived – one of the ERT team entered the pipe and retrieved the second welder.
Both welders lost their lives.
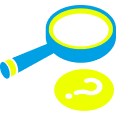
Why did it happen?
Entry into the pipe spool was unplanned and unauthorised. The repair was supposed to be carried out externally, so the workers did not have confined space permit controls and had not undertaken risk management processes.
A poor-quality non-proprietary argon purge dam was used.
After removing the argon weld purge dam, no ventilation of the pipe spool occurred.
The pipe spool was not capped.
Neither argon or confined space advisory signs were on the pipe or in the purge area.
Onboarding induction contained limited information on inert gas safety.
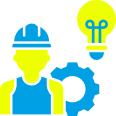
What did they learn?
Ensure workers understand that entry into pipe spools should only be a last resort and under a confined space permit.
Ensure lockable covers are installed on open pipe ends greater than 18”.
Develop and implement the following training programmes:
- Installation, utilisation, and removal of purge dams.
- Inert gas awareness.
- Line blowing.
Improve safety signage on site.
Investigate other options to negate the need for argon purge welding.
Ensure identified defects are discussed with the welding engineer to determine correct diagnosis and associated repairs.
Ensure workers have the correct tools for their tasks.
Undertake a review of emergency response arrangements.
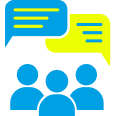
Ask yourself or your crew
Do we expect to need to enter a confined space to complete today’s activity?
Do you have all the correct permits in place for your work?
What do we have in place to prevent or deter people from entering confined spaces? (Think signage, equipment, procedures)
If confined space entry is required:
- Is there a safer way to do the job that doesn’t require confined space entry?
- What precautions have we put in place to ensure it is safe? What more can we do?
- What is our emergency response procedure?
Two welders were repairing an external weld on a pipe spool. One worker entered the pipe to check the weld and collapsed. The second worker tried to recover his colleague and also collapsed.