-
What happened?
A worker was servicing a top drive assembly. A job safety analysis (JSA) had been developed for the task.
The torque back-up clamp cylinder was too low, so the height needed to be raised.
The worker raised the assembly (weighing 600 lb/272 kg) with a lift cable so the spacers could be adjusted.
The lift cable broke and the assembly fell 7.5cm (3in) on top of the worker’s finger.
The worker received cuts to their finger.
-
Why did it happen?
There was no locking mechanism for the lifting system. The equipment design required the worker to be under a suspended load to adjust the spacers.
The task JSA and last-minute risk assessment did not identify any potential hazards.
Preventative maintenance is not typically carried out on the cable component of the assembly. Routine visual inspections only cover parts of the cable that can be seen.
-
What did they learn?
Identify stored energy sources so workers can recognise and avoid the line of fire if energy is unexpectedly released.
Eliminate stored energy hazards where possible (e.g. a lock mechanism to hold up the assembly).
Include stored energy hazard controls into the JSA.
Supervisors should confirm that all workers can describe task hazard controls and ensure that they are being performed effectively.
-
Ask yourself or your crew
How can something like this happen here?
What risks are there in your maintenance tasks? Does your JSA identify them all?
What do you know about stored energy hazards?
If there is a task you perform that could be done in a safer way, how would you approach this?
Add to homescreen
Content name
Select existing category:
Content name
New collection
Edit collection
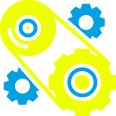
What happened?
A worker was servicing a top drive assembly. A job safety analysis (JSA) had been developed for the task.
The torque back-up clamp cylinder was too low, so the height needed to be raised.
The worker raised the assembly (weighing 600 lb/272 kg) with a lift cable so the spacers could be adjusted.
The lift cable broke and the assembly fell 7.5cm (3in) on top of the worker’s finger.
The worker received cuts to their finger.

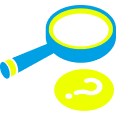
Why did it happen?
There was no locking mechanism for the lifting system. The equipment design required the worker to be under a suspended load to adjust the spacers.
The task JSA and last-minute risk assessment did not identify any potential hazards.
Preventative maintenance is not typically carried out on the cable component of the assembly. Routine visual inspections only cover parts of the cable that can be seen.
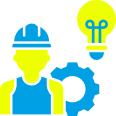
What did they learn?
Identify stored energy sources so workers can recognise and avoid the line of fire if energy is unexpectedly released.
Eliminate stored energy hazards where possible (e.g. a lock mechanism to hold up the assembly).
Include stored energy hazard controls into the JSA.
Supervisors should confirm that all workers can describe task hazard controls and ensure that they are being performed effectively.
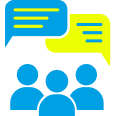
Ask yourself or your crew
How can something like this happen here?
What risks are there in your maintenance tasks? Does your JSA identify them all?
What do you know about stored energy hazards?
If there is a task you perform that could be done in a safer way, how would you approach this?
A worker was servicing a top drive assembly. When raising the torque back-up clamp cylinder, the lift cable broke and the assembly fell on the worker’s finger.