-
What happened?
On the 7th floor of a building under construction, a 6-tonne concrete wall panel was fixed into place and attached to the floor.
It was fixed using two ‘L’ brackets and two braces.
Four hours later, the panel’s fixings failed and it fell two levels to the 5th floor of the building.
No workers were injured, but it caused substantial damage to the scaffolding and formwork of the building.
-
Why did it happen?
The wall panel was not fully stable as it was not yet tied into the floor above.
The only things holding the panel in place were ‘L’ brackets (which were welded to the panel and the floor) and braces to stabilise the wall panel. This is common practice – often the wall panels are not secured to the floor above until days or weeks later.
The braces are only designed to prevent sideways movement of the wall panel and failed as the panel fell.
The integrity of the welds on the ‘L’ brackets was not strong enough to keep the wall panel upright.
-
What did they learn?
Welding is not a suitable way to attach panel brackets to concrete wall panels:
- Unable to prevent the panels moving during welding.
- Difficult for the welder to insert the electrode correctly.
- Difficult to gauge the correct heat to weld (too hot or too cold causes the weld to fail).
- Lack of testing to confirm the weld is structurally sound.
Bolted connections should be used between panels, brackets, and the building.
Any system for attaching walls to buildings should undergo a full design process by a competent engineer, follow this process for installation, be inspected and signed off.
-
Ask yourself or your crew
How can something like this happen here? What could the consequences be?
Is welding panels common practice here? Does that mean it is safe?
What alternative process should we use for fixing wall panels into place?
How would we respond to an incident like this?
Add to homescreen
Content name
Select existing category:
Content name
New collection
Edit collection
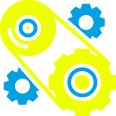
What happened?
On the 7th floor of a building under construction, a 6-tonne concrete wall panel was fixed into place and attached to the floor.
It was fixed using two ‘L’ brackets and two braces.
Four hours later, the panel’s fixings failed and it fell two levels to the 5th floor of the building.
No workers were injured, but it caused substantial damage to the scaffolding and formwork of the building.
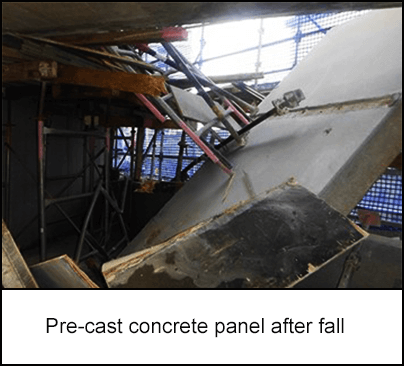
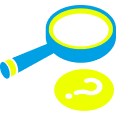
Why did it happen?
The wall panel was not fully stable as it was not yet tied into the floor above.
The only things holding the panel in place were ‘L’ brackets (which were welded to the panel and the floor) and braces to stabilise the wall panel. This is common practice – often the wall panels are not secured to the floor above until days or weeks later.
The braces are only designed to prevent sideways movement of the wall panel and failed as the panel fell.
The integrity of the welds on the ‘L’ brackets was not strong enough to keep the wall panel upright.
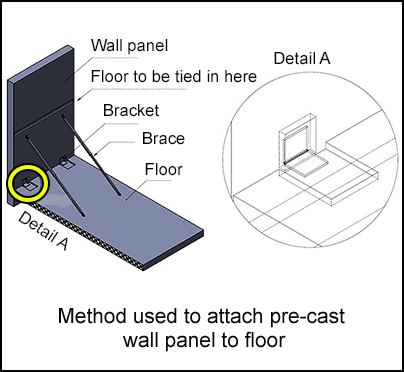
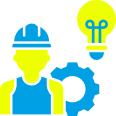
What did they learn?
Welding is not a suitable way to attach panel brackets to concrete wall panels:
- Unable to prevent the panels moving during welding.
- Difficult for the welder to insert the electrode correctly.
- Difficult to gauge the correct heat to weld (too hot or too cold causes the weld to fail).
- Lack of testing to confirm the weld is structurally sound.
Bolted connections should be used between panels, brackets, and the building.
Any system for attaching walls to buildings should undergo a full design process by a competent engineer, follow this process for installation, be inspected and signed off.
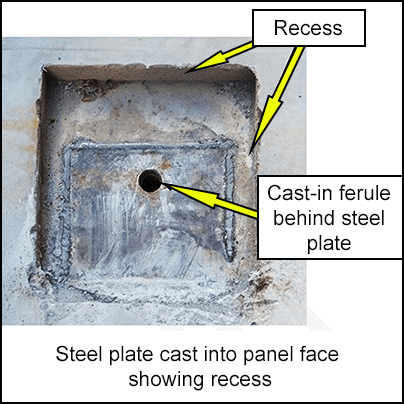
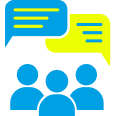
Ask yourself or your crew
How can something like this happen here? What could the consequences be?
Is welding panels common practice here? Does that mean it is safe?
What alternative process should we use for fixing wall panels into place?
How would we respond to an incident like this?
A 6-tonne concrete wall panel fell from the seventh floor of a building under construction. The panel fell to the fifth level floor slab, with scaffolding and formwork sustaining damage.