-
What happened?
Internal corrosion caused a pin hole leak in a section of steam condensate piping. It was fixed with a clamp.
After a second pin hole leak was discovered, the piping was removed from service to be replaced.
While loosening bolts on a blind flange to install replacement piping, live steam was released.
Steam could have caused serious burns to personnel.
-
Why did it happen?
Some time before opening the flange, the lock tag try was modified, placing a portion of the piping back in service.
Operators with less than 6 months experience were relied on to identify and verify lock tag try locations.
No try point for the condensate system was identified.
-
What did they learn?
Job site visits must use the energy isolation device list, blind list, and job/system drawings.
Operators with limited experience (e.g. less than 18 months – company dependant) need a second, independent verification and sign off on energy isolation device list.
Use bleeder blind flanges instead of blind flanges when a try point is unavailable or not in line of sight.
Prevent corrosion by:
- improving water sampling and water chemistry control systems.
- adjusting existing reliability operating limits and establish new ones on both boiler feed water and condensate systems to reduce internal corrosion.
-
Ask yourself or your crew
How could something like this happen here?
What other actions could have been taken?
How do we verify that lock tag try procedure is being followed as intended?
Can we use bleeder blind flanges? If not, what can we do to prevent similar events?
How do we know our water chemistry is preventing corrosion?
Add to homescreen
Content name
Select existing category:
Content name
New collection
Edit collection
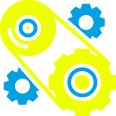
What happened?
Internal corrosion caused a pin hole leak in a section of steam condensate piping. It was fixed with a clamp.
After a second pin hole leak was discovered, the piping was removed from service to be replaced.
While loosening bolts on a blind flange to install replacement piping, live steam was released.
Steam could have caused serious burns to personnel.
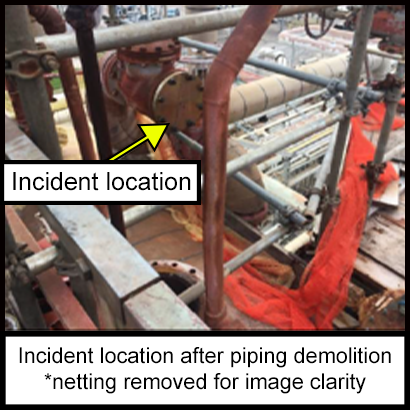
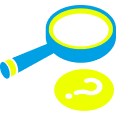
Why did it happen?
Some time before opening the flange, the lock tag try was modified, placing a portion of the piping back in service.
Operators with less than 6 months experience were relied on to identify and verify lock tag try locations.
No try point for the condensate system was identified.
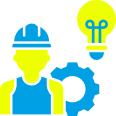
What did they learn?
Job site visits must use the energy isolation device list, blind list, and job/system drawings.
Operators with limited experience (e.g. less than 18 months – company dependant) need a second, independent verification and sign off on energy isolation device list.
Use bleeder blind flanges instead of blind flanges when a try point is unavailable or not in line of sight.
Prevent corrosion by:
- improving water sampling and water chemistry control systems.
- adjusting existing reliability operating limits and establish new ones on both boiler feed water and condensate systems to reduce internal corrosion.
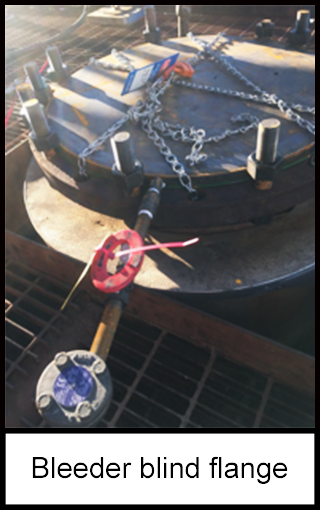
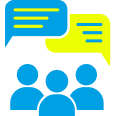
Ask yourself or your crew
How could something like this happen here?
What other actions could have been taken?
How do we verify that lock tag try procedure is being followed as intended?
Can we use bleeder blind flanges? If not, what can we do to prevent similar events?
How do we know our water chemistry is preventing corrosion?
While loosening bolts on a blind flange to install replacement piping, live steam was released. Steam could have caused serious burns to personnel.