-
What happened?
A worker was using a benchtop heavy drill machine to drill a hole through a wooden plank.
The drill chuck assembly ejected from the spindle hole, hitting the worker’s forehead.
The injured person received a laceration above his eyebrow.
-
Why did it happen?
The bench top drill was not fit to use, as the spindle sleeve was unavailable. The equipment had not been isolated to prevent unauthorised use.
A hexagon bolt had been modified (without authorisation) to use as a spindle sleeve.
The job should have been stopped, but the risk was considered tolerable.
The injured person was not wearing any personal protective equipment (PPE).
The worker was not familiar with the bench top drill assembly, operation, or safety precautions – it was his first time operating the machine.
Lack of appropriate supervision and lack of a safe system of work – the injured person should have not been allowed near the machine.
The worker and the supervisor were not fully aware of the scope or requirements of the job.
No appropriate toolbox talk (TBT) or risk assessment before the work started.
-
What did they learn?
All tools and equipment should be inspected, and unfit equipment should be isolated (so it won’t be utilised).
Ensure that handmade or modified tools are not used.
Verify that workers are trained to use the equipment and are aware of the risks.
Ensure appropriate level of supervision for the work carried out.
When work conditions change, stop the activity, and reassess the risks.
-
Ask yourself or your crew
What inspections do you carry out on your equipment before starting work? What should you do if the equipment / tools are unsuitable for the job?
How do you know what PPE you should wear for your tasks? What should you do if PPE is unavailable?
How do we isolate unfit equipment on site? Do we need to document it?
What measures do we have in place to prevent this from happening on our site?
Add to homescreen
Content name
Select existing category:
Content name
New collection
Edit collection
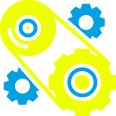
What happened?
A worker was using a benchtop heavy drill machine to drill a hole through a wooden plank.
The drill chuck assembly ejected from the spindle hole, hitting the worker’s forehead.
The injured person received a laceration above his eyebrow.
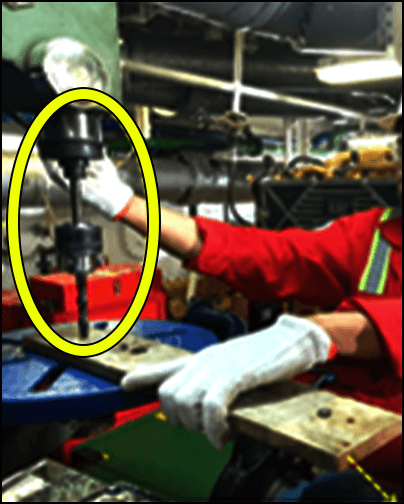
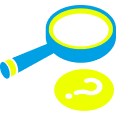
Why did it happen?
The bench top drill was not fit to use, as the spindle sleeve was unavailable. The equipment had not been isolated to prevent unauthorised use.
A hexagon bolt had been modified (without authorisation) to use as a spindle sleeve.
The job should have been stopped, but the risk was considered tolerable.
The injured person was not wearing any personal protective equipment (PPE).
The worker was not familiar with the bench top drill assembly, operation, or safety precautions – it was his first time operating the machine.
Lack of appropriate supervision and lack of a safe system of work – the injured person should have not been allowed near the machine.
The worker and the supervisor were not fully aware of the scope or requirements of the job.
No appropriate toolbox talk (TBT) or risk assessment before the work started.
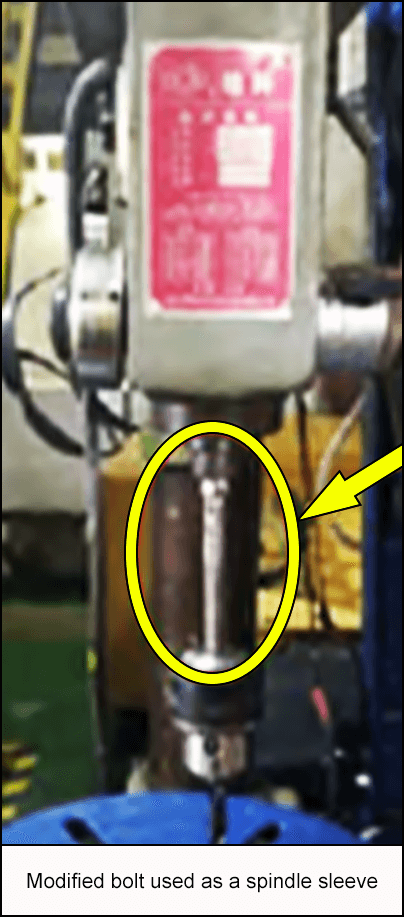
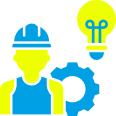
What did they learn?
All tools and equipment should be inspected, and unfit equipment should be isolated (so it won’t be utilised).
Ensure that handmade or modified tools are not used.
Verify that workers are trained to use the equipment and are aware of the risks.
Ensure appropriate level of supervision for the work carried out.
When work conditions change, stop the activity, and reassess the risks.
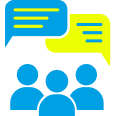
Ask yourself or your crew
What inspections do you carry out on your equipment before starting work? What should you do if the equipment / tools are unsuitable for the job?
How do you know what PPE you should wear for your tasks? What should you do if PPE is unavailable?
How do we isolate unfit equipment on site? Do we need to document it?
What measures do we have in place to prevent this from happening on our site?
A worker was drilling a hole through a wooden plank using a benchtop heavy drill machine. The drill chuck assembly detached and hit the worker’s forehead, causing injury.