-
What happened?
After finishing ground survey work at a service station, the contractors began to collect their equipment and material.
The operator who was drilling loosened the casing head of the lower clamp, separating it from the rod. This left the rod secured by the upper clamp and the casing head held by the lower clamp, with a vertical separation of 40 cm (15.5 inches).
The lower clamp was opened by activating the corresponding control located on the machine.
The operator placed his left hand on the casing head to hold it before it fell. With his right hand he accidentally activated the control of the upper clamp, which caused the rod to fall onto the casing head and on his left hand, striking his index finger and severing it instantly.
The worker had to have surgery for amputation and required time off work for recovery.
-
Why did it happen?
The operation lacked a design standard, and the machine had no mechanism to prevent it from being operated by one person.
The distance between the position of the controls and the mobile mechanical parts made it possible for a person to operate alone without assistance.
The standard procedure was not followed. The machine should have been operated by two persons (driller and assistant). In this case, the driller decided to act alone.
There was no mechanical safeguard nor differentiation between the controls for the machine’s various casing head operations (there was no difference between loosening clamps or relocating modules).
There was no safeguard or protection surrounding the rods and the gloves worn made it easier to confuse the position of the right hand, which activated the incorrect control.
Poor leadership led to a rush situation. After finishing work, with a 1100 km (680 miles) journey home right before a long national holiday, there was a hurry to disassemble the equipment. Unfortunately, important safety steps advised by the manufacturer were overlooked.
-
What did they learn?
Study and consider using anti-entrapment protection and safe machine designs. This includes placing a barrier between employees and moving parts that they can't pass while the machine is on.
Always do a thorough job safety assessment (JSA) for tasks involving mobile or energised equipment. Follow a basic operating standard that includes controlling risks for unusual operations.
Plan work in advance to make sure all needed preventive measures are taken. Confirm employee availability and allocate enough time for the task. Avoid rushing through tasks to ensure safety.
-
Ask yourself or your crew
How can something like this happen here?
What measures can be implemented to prevent confusion between machine controls and enhance the differentiation between various casing head operations, such as loosening clamps or relocating modules?
What measures do we have in place to prevent similar incidents happening on our site?
What else can you do to keep safe when working with energised equipment?
Add to homescreen
Content name
Select existing category:
Content name
New collection
Edit collection
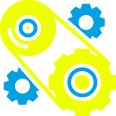
What happened?
After finishing ground survey work at a service station, the contractors began to collect their equipment and material.
The operator who was drilling loosened the casing head of the lower clamp, separating it from the rod. This left the rod secured by the upper clamp and the casing head held by the lower clamp, with a vertical separation of 40 cm (15.5 inches).
The lower clamp was opened by activating the corresponding control located on the machine.
The operator placed his left hand on the casing head to hold it before it fell. With his right hand he accidentally activated the control of the upper clamp, which caused the rod to fall onto the casing head and on his left hand, striking his index finger and severing it instantly.
The worker had to have surgery for amputation and required time off work for recovery.
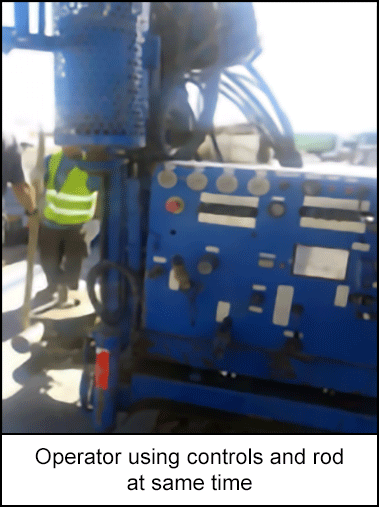
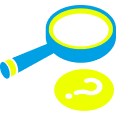
Why did it happen?
The operation lacked a design standard, and the machine had no mechanism to prevent it from being operated by one person.
The distance between the position of the controls and the mobile mechanical parts made it possible for a person to operate alone without assistance.
The standard procedure was not followed. The machine should have been operated by two persons (driller and assistant). In this case, the driller decided to act alone.
There was no mechanical safeguard nor differentiation between the controls for the machine’s various casing head operations (there was no difference between loosening clamps or relocating modules).
There was no safeguard or protection surrounding the rods and the gloves worn made it easier to confuse the position of the right hand, which activated the incorrect control.
Poor leadership led to a rush situation. After finishing work, with a 1100 km (680 miles) journey home right before a long national holiday, there was a hurry to disassemble the equipment. Unfortunately, important safety steps advised by the manufacturer were overlooked.
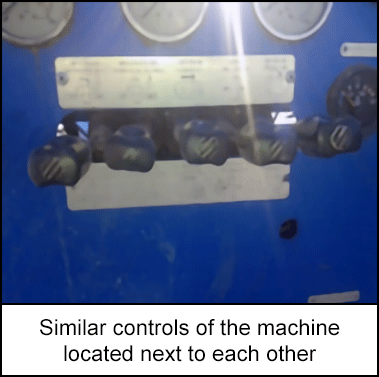
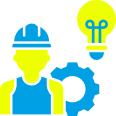
What did they learn?
Study and consider using anti-entrapment protection and safe machine designs. This includes placing a barrier between employees and moving parts that they can't pass while the machine is on.
Always do a thorough job safety assessment (JSA) for tasks involving mobile or energised equipment. Follow a basic operating standard that includes controlling risks for unusual operations.
Plan work in advance to make sure all needed preventive measures are taken. Confirm employee availability and allocate enough time for the task. Avoid rushing through tasks to ensure safety.
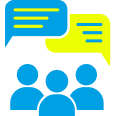
Ask yourself or your crew
How can something like this happen here?
What measures can be implemented to prevent confusion between machine controls and enhance the differentiation between various casing head operations, such as loosening clamps or relocating modules?
What measures do we have in place to prevent similar incidents happening on our site?
What else can you do to keep safe when working with energised equipment?
Following ground survey work at a service station, contractors faced a serious accident when the drilling operator, attempting to secure equipment, inadvertently activated the wrong control, causing a falling rod to sever his index finger. This resulted in the worker undergoing surgery and taking time off for recovery.