-
What happened?
To reduce potential hydrogen sulphide (H2S) exposure during maintenance, 4 temporary pumps were started to drain produced water from a main water injection station. Produced water began to leak from the pumps and associated piping.
When their personal H2S monitors began to alarm, personnel attempted to stop the leaks
Valves were closed and pumps were shut down while evacuating to the muster point.
Under supplied air, 3 contractor employees successfully mitigated the leak.
In total, 13 personal H2S monitors alarmed for up to 18 seconds, with exposure ranging from 74 ppm to more than 100 ppm.
-
Why did it happen?
The drain and vent valves on the temporary pumps were left open when the pumps were started.
Leaks were identified on the threaded discharge fittings assembled by the pump rental company.
Temporary equipment was installed instead of process equipment in a high H2S (~35%) service area.
Pre-startup safety review was not conducted.
-
What did they learn?
Consider using temporary management of change procedures when connecting temporary equipment to process equipment.
Consider developing written procedures for infrequent tasks that involve high risk activities.
Confirm that leak tests have been performed on equipment in high H2S service areas prior to start up.
Ensure personal H2S monitors are inspected, tested and positioned within the breathing zone of the wearer forward of the shoulders.
When evacuating due to an H2S event, immediately proceed to the closest upwind muster point.
-
Ask yourself or your crew
What other actions could have been taken?
How can something like this happen here and what can you do to prevent it?
What is your role in confirming that leak tests have been performed prior to start up?
What do you need to do in case of a similar incident?
Add to homescreen
Content name
Select existing category:
Content name
New collection
Edit collection
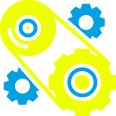
What happened?
To reduce potential hydrogen sulphide (H2S) exposure during maintenance, 4 temporary pumps were started to drain produced water from a main water injection station. Produced water began to leak from the pumps and associated piping.
When their personal H2S monitors began to alarm, personnel attempted to stop the leaks
Valves were closed and pumps were shut down while evacuating to the muster point.
Under supplied air, 3 contractor employees successfully mitigated the leak.
In total, 13 personal H2S monitors alarmed for up to 18 seconds, with exposure ranging from 74 ppm to more than 100 ppm.
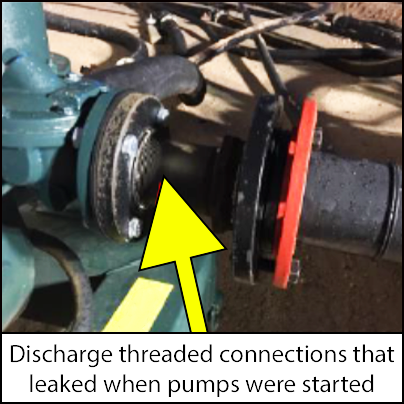
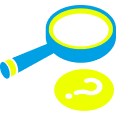
Why did it happen?
The drain and vent valves on the temporary pumps were left open when the pumps were started.
Leaks were identified on the threaded discharge fittings assembled by the pump rental company.
Temporary equipment was installed instead of process equipment in a high H2S (~35%) service area.
Pre-startup safety review was not conducted.
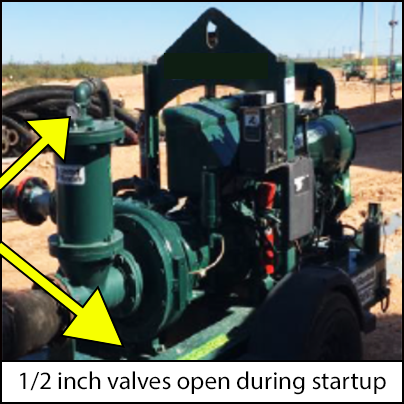
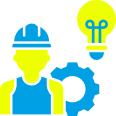
What did they learn?
Consider using temporary management of change procedures when connecting temporary equipment to process equipment.
Consider developing written procedures for infrequent tasks that involve high risk activities.
Confirm that leak tests have been performed on equipment in high H2S service areas prior to start up.
Ensure personal H2S monitors are inspected, tested and positioned within the breathing zone of the wearer forward of the shoulders.
When evacuating due to an H2S event, immediately proceed to the closest upwind muster point.
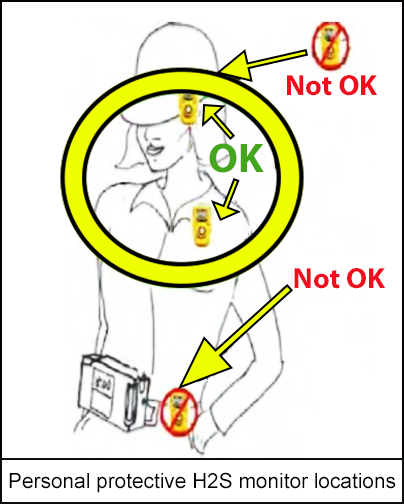
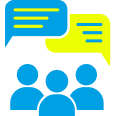
Ask yourself or your crew
What other actions could have been taken?
How can something like this happen here and what can you do to prevent it?
What is your role in confirming that leak tests have been performed prior to start up?
What do you need to do in case of a similar incident?
4 temporary pumps were started to drain produced water from a main water injection station. After starting the pumps, water began to leak and personnel H2S monitors started to alarm.