-
What happened?
Two workers were on the upper main tensioner level of a pipelay tower, removing dowels from the tensioner gear boxes.
They were using a spanner wrench, dowel removal tool and the 2kg (4.4lb) lump hammer.
The workers were striking the spanner wrench with the lump hammer.
As the hammer hit the spanner wrench, the hammer head detached from the shaft and fell 25 meters (82 feet) down through the tensioner to the deck below.
There were no injuries.
-
Why did it happen?
The hammer was not appropriately designed for the task.
- The shaft of the hammer was fitted with a lanyard to prevent a drop risk, but the head can separate from the shaft and there was no way to secure it.
- The crew should have used a hammer designed for working at height – one where the head cannot separate from the shaft.
The hammer was ordered several years earlier in response to a similar incident involving a dropped wooden hammer shaft. At the time or ordering, it was deemed suitable for working at height.
Despite inspection prior to use, the hammer showed no defects. A hammer designed for working at height would not have failed in this way.
There were no injuries because the area below had been barriered off and sentries were posted to prevent personnel entering the area.
-
What did they learn?
Ensure that only equipment designed for use at height is used.
Confirm that tools used for working at height offer complete dropped object prevention.
Liaise with regulator for advice if new tools are required.
-
Ask yourself or your crew
How can something like this happen here?
How do you know that the equipment you use is designed for working at height?
What checks do you carry out on your equipment before you use it?
How would you request new equipment if yours was not suitable?
Add to homescreen
Content name
Select existing category:
Content name
New collection
Edit collection
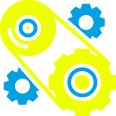
What happened?
Two workers were on the upper main tensioner level of a pipelay tower, removing dowels from the tensioner gear boxes.
They were using a spanner wrench, dowel removal tool and the 2kg (4.4lb) lump hammer.
The workers were striking the spanner wrench with the lump hammer.
As the hammer hit the spanner wrench, the hammer head detached from the shaft and fell 25 meters (82 feet) down through the tensioner to the deck below.
There were no injuries.
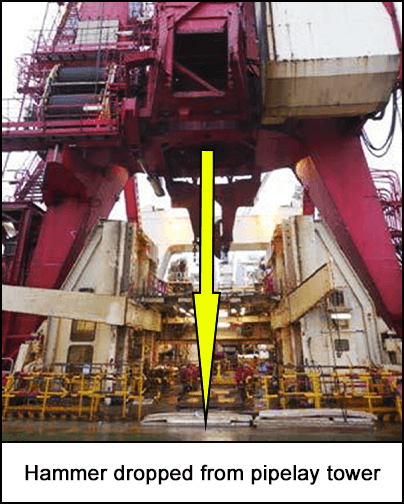
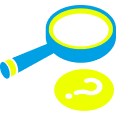
Why did it happen?
The hammer was not appropriately designed for the task.
- The shaft of the hammer was fitted with a lanyard to prevent a drop risk, but the head can separate from the shaft and there was no way to secure it.
- The crew should have used a hammer designed for working at height – one where the head cannot separate from the shaft.
The hammer was ordered several years earlier in response to a similar incident involving a dropped wooden hammer shaft. At the time or ordering, it was deemed suitable for working at height.
Despite inspection prior to use, the hammer showed no defects. A hammer designed for working at height would not have failed in this way.
There were no injuries because the area below had been barriered off and sentries were posted to prevent personnel entering the area.
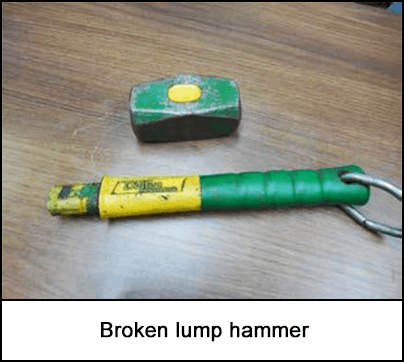
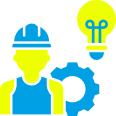
What did they learn?
Ensure that only equipment designed for use at height is used.
Confirm that tools used for working at height offer complete dropped object prevention.
Liaise with regulator for advice if new tools are required.
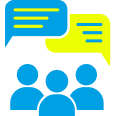
Ask yourself or your crew
How can something like this happen here?
How do you know that the equipment you use is designed for working at height?
What checks do you carry out on your equipment before you use it?
How would you request new equipment if yours was not suitable?
Two workers were working in a pipelay tower, removing dowels from the tensioner gear boxes. As they were striking the spanner wrench with the lump hammer, the hammer head detached from the shaft and fell 25 meters to the deck below.