-
What happened?
An operator connected a hose to a pump to begin charging the filter press.
He checked the connections and found no leaks.
He left the pump to check on a vacuum truck working close by.
On returning to the pump, the operator found liquid had leaked into the filter press containment.
The hose to the pump had come loose, allowing potassium hydroxide (KOH) to flow from the tank for 15 minutes.
-
Why did it happen?
The cotter pin used to hold the ‘dog ears’ in place was bent.
Due to the cotter pin failure, the hose to the pump became loose, allowing caustic to flow from the tank.
-
What did they learn?
Velcro straps could be used to keep the ‘dog ears’ in place, ensuring the pump connections are safe.
Flanged design may reduce risk of disconnection.
Consider:
- Repiping the system so that hose connections are a straight run.
- Installing pulsation dampeners to reduce strain on hoses.
- Switching to self-locking cam lock fittings.
Operators should be adequately trained on the use of camlocks.
-
Ask yourself or your crew
Should the worker have left his job to check on the vacuum truck?
What’s the worst that can happen with such incidents? What can you do to prevent it?
What system design changes would make your work safer?
What is the chemical spills response procedure on our site?
Add to homescreen
Content name
Select existing category:
Content name
New collection
Edit collection
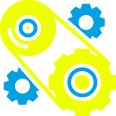
What happened?
An operator connected a hose to a pump to begin charging the filter press.
He checked the connections and found no leaks.
He left the pump to check on a vacuum truck working close by.
On returning to the pump, the operator found liquid had leaked into the filter press containment.
The hose to the pump had come loose, allowing potassium hydroxide (KOH) to flow from the tank for 15 minutes.
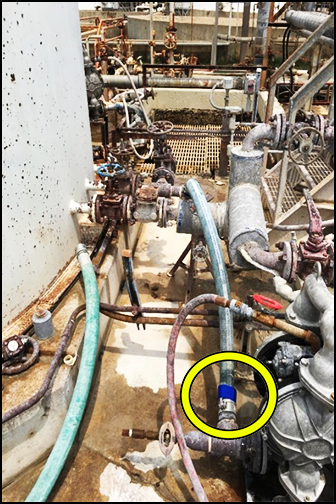
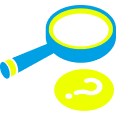
Why did it happen?
The cotter pin used to hold the ‘dog ears’ in place was bent.
Due to the cotter pin failure, the hose to the pump became loose, allowing caustic to flow from the tank.
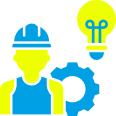
What did they learn?
Velcro straps could be used to keep the ‘dog ears’ in place, ensuring the pump connections are safe.
Flanged design may reduce risk of disconnection.
Consider:
- Repiping the system so that hose connections are a straight run.
- Installing pulsation dampeners to reduce strain on hoses.
- Switching to self-locking cam lock fittings.
Operators should be adequately trained on the use of camlocks.
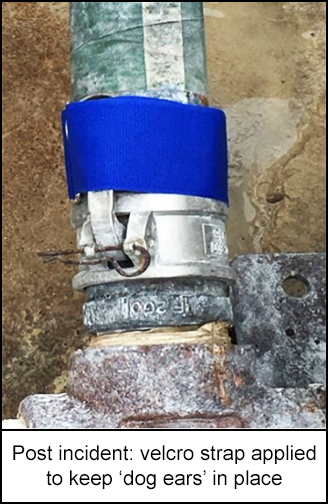
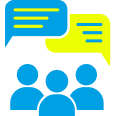
Ask yourself or your crew
Should the worker have left his job to check on the vacuum truck?
What’s the worst that can happen with such incidents? What can you do to prevent it?
What system design changes would make your work safer?
What is the chemical spills response procedure on our site?
An operator was charging a filter press. The connection between the hose and the pump came loose, allowing potassium hydroxide to leak into the filter press containment.