-
What happened?
Two workers were using a service basket to manually hang a wireline sheave to a derrick beam pad eye plate located 10m above the rig floor.
A worker lost his grip on the sheave swivel and dropped it on the rig floor.
No personnel were in the drop zone at the time, therefore nobody was injured.
Less than a minute before the object was dropped, a worker entered the exclusion zone to retrieve a nylon sling. His story could have been very different.
-
Why did it happen?
Ineffective zone management process for working at heights.
Unusual or different working conditions:
- Non-routine operation with a temporary sheave. Not designed to facilitate safe installation.
- The supervisors left the area to try to solve a problem they were having with some equipment.
- A deck foreman signed off / verified the pre-job risk mitigations but had not been fully trained on the process.
- 28 MPH winds are considered windy conditions for rig floor operations.
There were simultaneous operations going on to set up for wireline operations, meaning lots of people around to potentially get injured or cause distractions.
-
What did they learn?
Effective zone management (red/no-go/exclusion zone) is a critical safeguard when working at height. Ensure the zone is in place and functioning before starting work.
Workers should always maintain a sense of vulnerability and be vigilent.
-
Ask yourself or your crew
How can something like this happen here?
What other operations are taking place near us might impact or be impacted by our work?
Are we using the equipment correctly and in the way it was intended?
What is your role in ensuring that red zones are in place before starting work? How are they identified?
What hazards should we be aware of in today’s task?
Add to homescreen
Content name
Select existing category:
Content name
New collection
Edit collection
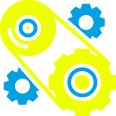
What happened?
Two workers were using a service basket to manually hang a wireline sheave to a derrick beam pad eye plate located 10m above the rig floor.
A worker lost his grip on the sheave swivel and dropped it on the rig floor.
No personnel were in the drop zone at the time, therefore nobody was injured.
Less than a minute before the object was dropped, a worker entered the exclusion zone to retrieve a nylon sling. His story could have been very different.
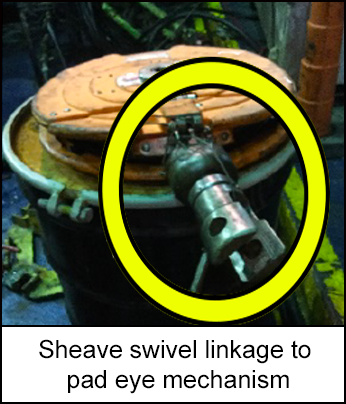
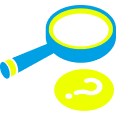
Why did it happen?
Ineffective zone management process for working at heights.
Unusual or different working conditions:
- Non-routine operation with a temporary sheave. Not designed to facilitate safe installation.
- The supervisors left the area to try to solve a problem they were having with some equipment.
- A deck foreman signed off / verified the pre-job risk mitigations but had not been fully trained on the process.
- 28 MPH winds are considered windy conditions for rig floor operations.
There were simultaneous operations going on to set up for wireline operations, meaning lots of people around to potentially get injured or cause distractions.
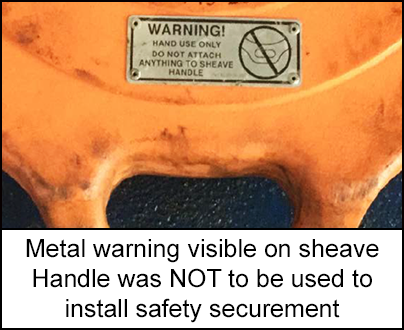
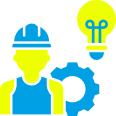
What did they learn?
Effective zone management (red/no-go/exclusion zone) is a critical safeguard when working at height. Ensure the zone is in place and functioning before starting work.
Workers should always maintain a sense of vulnerability and be vigilent.
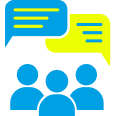
Ask yourself or your crew
How can something like this happen here?
What other operations are taking place near us might impact or be impacted by our work?
Are we using the equipment correctly and in the way it was intended?
What is your role in ensuring that red zones are in place before starting work? How are they identified?
What hazards should we be aware of in today’s task?
Two workers were manually hanging a wireline sheave to a pad eye plate situated 10m above the rig floor. A worker lost his grip on the sheave swivel and dropped it on the rig floor…