-
What happened?
A maintenance operator from a services company went to his work area after receiving the appropriate work permit for loosening the discharge valve to drain of a sulphuric acid metering pump.
As the work did not involve contact with the corrosive product, the need to use personal protective equipment (PPE) was not required.
Once this task was finished, the plant operator asked the maintenance worker to also dismantle the piping’s purge valve as it was obstructed.
He checked that the valve was totally open and isolated. However, during the repair an acid splash took place, which caused a burn on the maintenance operator’s chin.
-
Why did it happen?
The process conditions were not identified in the design. There may have been a product in the line because the pump’s discharge line could not be completely purged without opening a flange, as it only had one vent.
There were faults with procedures and the control of operations, as well as a faulty work permit or a poor risk assessment. There was an unplanned dismantling of one of the facility’s components. No work permit had been issued for the risks of this second task.
There were missing or failed safeguards/barriers - Personal protection was insufficient, faulty, or used incorrectly. The PPE worn was inadequate for the risks from this substance.
-
What did they learn?
When performing multiple actions, assess the risks associated with each task and the products involved.
Ensure that you or the person performing the task is fully informed and comprehends the communicated risks specified in the work permit.
Do not undertake additional tasks that have not been previously requested or planned.
Exercise extra caution when dealing with flanges and valves, ensuring proper isolation measures are in place.
Never make exceptions regarding the use of personal protective equipment (PPE), even for seemingly quick tasks.
Adopt a work position that minimizes the potential for personal injury in the event of an incident such as splashing or impact.
When designing facilities, consider using components that allow maintenance to be conducted in a safe manner.
-
Ask yourself or your crew
How can we prevent something like this from happening here?
What measures do we have in place to encourage extra caution when handling flanges and valves, particularly in terms of ensuring proper isolation? What else can we do?
How can we eliminate exceptions in the use of personal protective equipment (PPE), even for tasks that may seem quick or routine?
What strategies can be employed to promote a work position that minimises the potential for personal injury during incidents such as splashing or impact?
Add to homescreen
Content name
Select existing category:
Content name
New collection
Edit collection
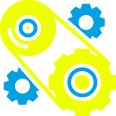
What happened?
A maintenance operator from a services company went to his work area after receiving the appropriate work permit for loosening the discharge valve to drain of a sulphuric acid metering pump.
As the work did not involve contact with the corrosive product, the need to use personal protective equipment (PPE) was not required.
Once this task was finished, the plant operator asked the maintenance worker to also dismantle the piping’s purge valve as it was obstructed.
He checked that the valve was totally open and isolated. However, during the repair an acid splash took place, which caused a burn on the maintenance operator’s chin.
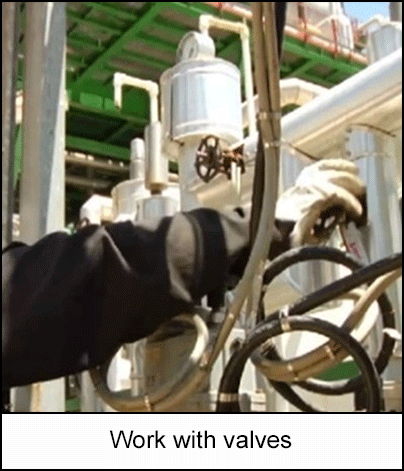
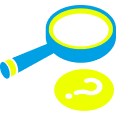
Why did it happen?
The process conditions were not identified in the design. There may have been a product in the line because the pump’s discharge line could not be completely purged without opening a flange, as it only had one vent.
There were faults with procedures and the control of operations, as well as a faulty work permit or a poor risk assessment. There was an unplanned dismantling of one of the facility’s components. No work permit had been issued for the risks of this second task.
There were missing or failed safeguards/barriers - Personal protection was insufficient, faulty, or used incorrectly. The PPE worn was inadequate for the risks from this substance.

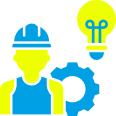
What did they learn?
When performing multiple actions, assess the risks associated with each task and the products involved.
Ensure that you or the person performing the task is fully informed and comprehends the communicated risks specified in the work permit.
Do not undertake additional tasks that have not been previously requested or planned.
Exercise extra caution when dealing with flanges and valves, ensuring proper isolation measures are in place.
Never make exceptions regarding the use of personal protective equipment (PPE), even for seemingly quick tasks.
Adopt a work position that minimizes the potential for personal injury in the event of an incident such as splashing or impact.
When designing facilities, consider using components that allow maintenance to be conducted in a safe manner.
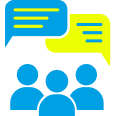
Ask yourself or your crew
How can we prevent something like this from happening here?
What measures do we have in place to encourage extra caution when handling flanges and valves, particularly in terms of ensuring proper isolation? What else can we do?
How can we eliminate exceptions in the use of personal protective equipment (PPE), even for tasks that may seem quick or routine?
What strategies can be employed to promote a work position that minimises the potential for personal injury during incidents such as splashing or impact?
A maintenance operator was for loosening the discharge valve to drain of a sulphuric acid metering pump. Once they had finished, the plant operator asked the maintenance worker to also dismantle an obstructed piping’s purge valve. During the repair an acid splash took place, which caused a burn on the maintenance operator’s chin area.